Deck 21: Material Requirements Planning
سؤال
سؤال
سؤال
سؤال
سؤال
سؤال
سؤال
سؤال
سؤال
سؤال
سؤال
سؤال
سؤال
سؤال
سؤال
سؤال
سؤال
سؤال
سؤال
سؤال
سؤال
سؤال
سؤال
سؤال
سؤال
سؤال
سؤال
سؤال
سؤال
سؤال
سؤال
سؤال
سؤال
سؤال
سؤال
سؤال
سؤال
سؤال
سؤال
سؤال
سؤال
سؤال
سؤال
سؤال
سؤال
سؤال
سؤال
سؤال
سؤال
سؤال
سؤال
سؤال
فتح الحزمة
قم بالتسجيل لفتح البطاقات في هذه المجموعة!
Unlock Deck
Unlock Deck
1/52
العب
ملء الشاشة (f)
Deck 21: Material Requirements Planning
1
Initially, assume that Phil wants to minimize his inventory requirements. Assume that each order will be only for what is required for a single period. Using the following forms, calculate the net requirements and planned order releases for the gear boxes and input shafts. Assume that lot sizing is done using lot-for-lot (L4L).
Lot-for-Lot for Reference:
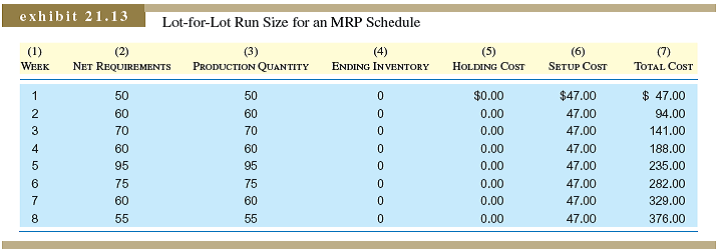
Lot-for-Lot for Reference:
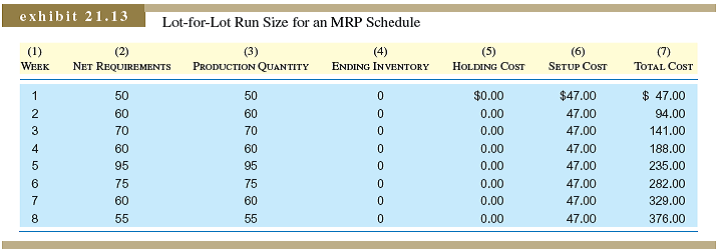
Companies should make a Material Requirement Plan (MRP) to tackle the market demands efficiently and make good profits.
Consider the following details for model 1000:
Master schedule:
1 engine = 1 gearbox
1 gearbox = 2 shafts
Gearbox:
Beginning inventory for gearboxes in week 1 = 17
Scheduled receipt in week 2 = 5
Lead time = 2 weeks
Input shafts:
Beginning inventory in week 1 = 40
Scheduled receipt in week 2 = 22
Lead time = 3 weeks
Calculate the net requirements and planned order release for the gearbox and shaft using the formulas as shown below:
• Insert the values into an excel spreadsheet as shown below:
Thus, the MRP for gear box and input shaft is shown above.
Consider the following details for model 1000:
Master schedule:

1 gearbox = 2 shafts
Gearbox:
Beginning inventory for gearboxes in week 1 = 17
Scheduled receipt in week 2 = 5
Lead time = 2 weeks
Input shafts:
Beginning inventory in week 1 = 40
Scheduled receipt in week 2 = 22
Lead time = 3 weeks
Calculate the net requirements and planned order release for the gearbox and shaft using the formulas as shown below:

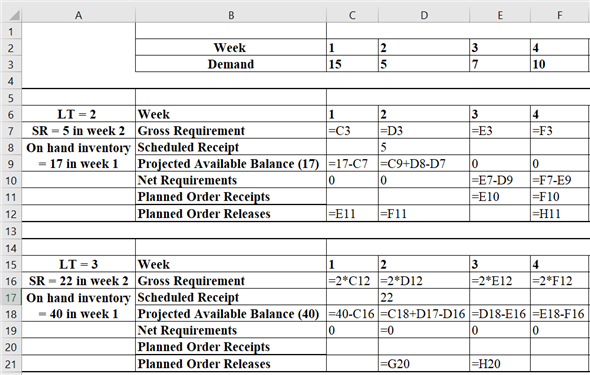
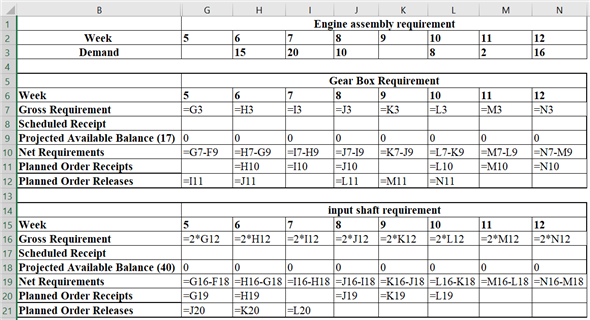
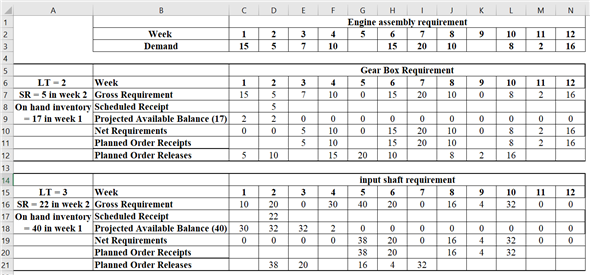
2
What do we mean when we say that MRP is based on dependent demand?
MRP, Materials requirement planning determines the number of components or parts that are required to make a particular product.
This is why MRP is based on dependent demand, where the requirement of one product directly results in the demand of another product. This product may be a part or subpart of the original product.
Besides that, dependent demand is caused by the demand for a high-level item. For example, tires, wheels and engines are all dependent items that are based on the demand for automobiles.
This is why MRP is based on dependent demand, where the requirement of one product directly results in the demand of another product. This product may be a part or subpart of the original product.
Besides that, dependent demand is caused by the demand for a high-level item. For example, tires, wheels and engines are all dependent items that are based on the demand for automobiles.
3
Match the industry type to the expected benefits from an MRP system as High, Medium, or Low.
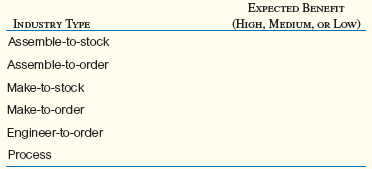
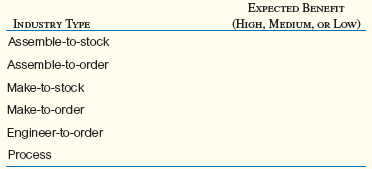
The details of the industry type and expected benefits from an MRP are shown below:
Industry Type Expected benefits (High, Medium or Low)Assemble-to-stock High
Assemble-to-order High
Make-to-stock Medium
Make-to-order Low
Engineer-to-order High
Process Medium
Match the industry type to the expected benefits from an MRP system. These are listed below:
Assemble-to-stock: The expected benefits from an MRP system are high in this industry type, as it involves assembling various multiple components to make a particular finished product. These components are stocked on a satisfactory level to meet the customer demand. Assemble-to-order: The expected benefits from an MRP system are high in this industry type because the final assembly of products results from standard options. It is from where customer chooses the products.
Make-to-stock: In this industry type, the product is directly manufactured by machine and does not involve any assembly of parts and hence, benefits from an MRP system are medium. As per the expected consumer demand, these items are stocked at a specified level.
Make-to-order: In this industry type, the product is manufactured by machine as per the customer order and is generally considered as industrial orders. Hence, benefits from an MRP system are low.
Engineer-to-order: In this industry type, the fabrication and assembly of products are totally based on specification provided by the customer. This is why the expected benefits from an MRP system are high in this industry type. Process: The expected benefits from an MRP system are medium in this industry type like paper industry, chemicals industry etc.
Industry Type Expected benefits (High, Medium or Low)Assemble-to-stock High
Assemble-to-order High
Make-to-stock Medium
Make-to-order Low
Engineer-to-order High
Process Medium
Match the industry type to the expected benefits from an MRP system. These are listed below:
Assemble-to-stock: The expected benefits from an MRP system are high in this industry type, as it involves assembling various multiple components to make a particular finished product. These components are stocked on a satisfactory level to meet the customer demand. Assemble-to-order: The expected benefits from an MRP system are high in this industry type because the final assembly of products results from standard options. It is from where customer chooses the products.
Make-to-stock: In this industry type, the product is directly manufactured by machine and does not involve any assembly of parts and hence, benefits from an MRP system are medium. As per the expected consumer demand, these items are stocked at a specified level.
Make-to-order: In this industry type, the product is manufactured by machine as per the customer order and is generally considered as industrial orders. Hence, benefits from an MRP system are low.
Engineer-to-order: In this industry type, the fabrication and assembly of products are totally based on specification provided by the customer. This is why the expected benefits from an MRP system are high in this industry type. Process: The expected benefits from an MRP system are medium in this industry type like paper industry, chemicals industry etc.
4
Term used for a computer system that integrates application programs for the different functions in a fi rm.
فتح الحزمة
افتح القفل للوصول البطاقات البالغ عددها 52 في هذه المجموعة.
فتح الحزمة
k this deck
5
Phil would like to consider the costs that his accountants are currently using for inventory carrying and setup for the gear boxes and input shafts. These costs are as follows:
Given the cost structure, evaluate the cost of the schedule from question 1. Assume inventory is valued at the end of each week.
Question 1 for Reference:
Initially, assume that Phil wants to minimize his inventory requirements. Assume that each order will be only for what is required for a single period. Using the following forms, calculate the net requirements and planned order releases for the gear boxes and input shafts. Assume that lot sizing is done using lot-for-lot (L4L).
Lot-for-Lot for Reference:
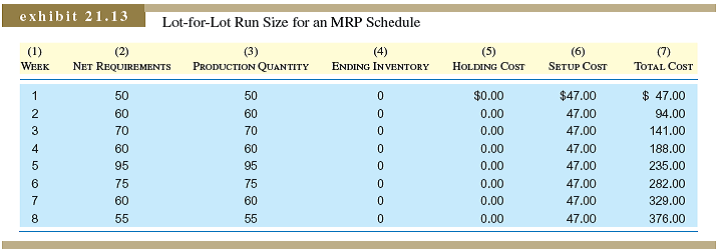
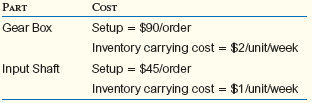
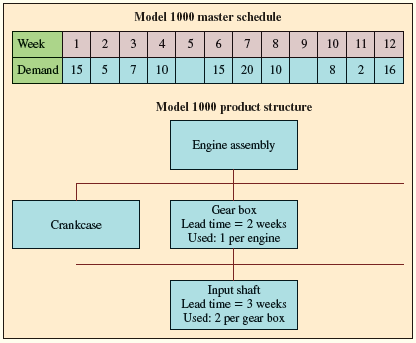
Given the cost structure, evaluate the cost of the schedule from question 1. Assume inventory is valued at the end of each week.
Question 1 for Reference:
Initially, assume that Phil wants to minimize his inventory requirements. Assume that each order will be only for what is required for a single period. Using the following forms, calculate the net requirements and planned order releases for the gear boxes and input shafts. Assume that lot sizing is done using lot-for-lot (L4L).
Lot-for-Lot for Reference:
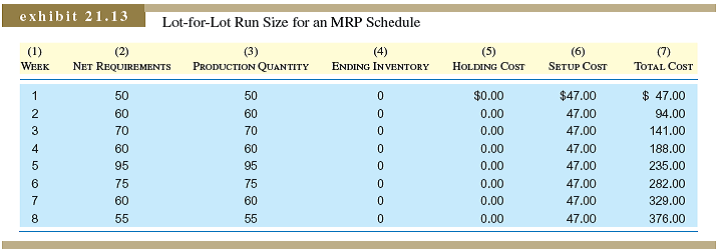
فتح الحزمة
افتح القفل للوصول البطاقات البالغ عددها 52 في هذه المجموعة.
فتح الحزمة
k this deck
6
Discuss the importance of the master production schedule in an MRP system.
فتح الحزمة
افتح القفل للوصول البطاقات البالغ عددها 52 في هذه المجموعة.
فتح الحزمة
k this deck
7
MRP is based on what type of demand?
فتح الحزمة
افتح القفل للوصول البطاقات البالغ عددها 52 في هذه المجموعة.
فتح الحزمة
k this deck
8
Logic used to calculate the needed parts, components, and other materials needed to produce an end item.
فتح الحزمة
افتح القفل للوصول البطاقات البالغ عددها 52 في هذه المجموعة.
فتح الحزمة
k this deck
9
Find a better schedule by reducing the number of orders and carrying some inventory. What are the savings with this new schedule?
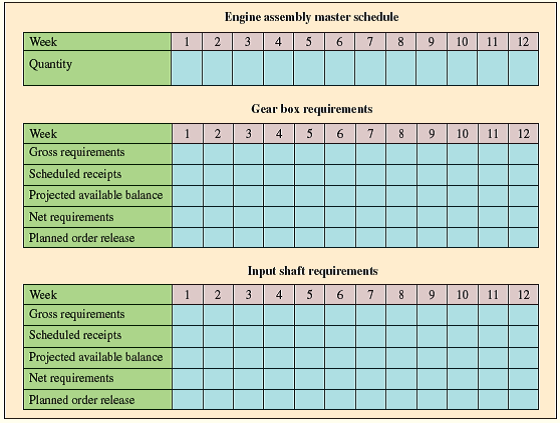
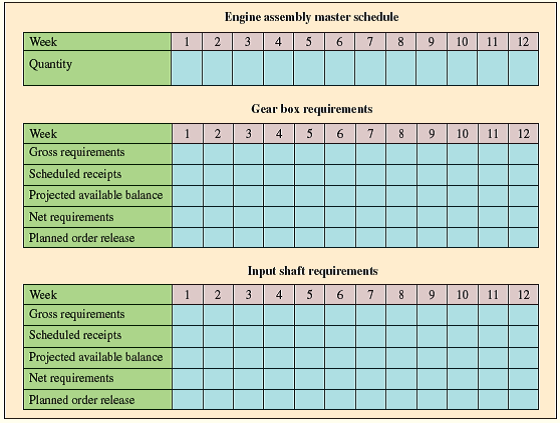
فتح الحزمة
افتح القفل للوصول البطاقات البالغ عددها 52 في هذه المجموعة.
فتح الحزمة
k this deck
10
Explain the need for time fences in the master production schedule.
فتح الحزمة
افتح القفل للوصول البطاقات البالغ عددها 52 في هذه المجموعة.
فتح الحزمة
k this deck
11
Which scheduling process drives requirements in the MRP process?
فتح الحزمة
افتح القفل للوصول البطاقات البالغ عددها 52 في هذه المجموعة.
فتح الحزمة
k this deck
12
This drives the MRP calculations and is a detailed plan for how we expect to meet demand.
فتح الحزمة
افتح القفل للوصول البطاقات البالغ عددها 52 في هذه المجموعة.
فتح الحزمة
k this deck
13
"MRP just prepares shopping lists. It does not do the shopping or cook the dinner." Comment.
فتح الحزمة
افتح القفل للوصول البطاقات البالغ عددها 52 في هذه المجموعة.
فتح الحزمة
k this deck
14
What term is used to identify the difference between the number of units of an item listed on the master schedule and the number of firm customer orders?
فتح الحزمة
افتح القفل للوصول البطاقات البالغ عددها 52 في هذه المجموعة.
فتح الحزمة
k this deck
15
Period of time during which a customer has a specified level of opportunity to make changes.
فتح الحزمة
افتح القفل للوصول البطاقات البالغ عددها 52 في هذه المجموعة.
فتح الحزمة
k this deck
16
What are the sources of demand in an MRP system? Are these dependent or independent, and how are they used as inputs to the system?
فتح الحزمة
افتح القفل للوصول البطاقات البالغ عددها 52 في هذه المجموعة.
فتح الحزمة
k this deck
17
What are the three primary data sources used by the MRP system?
فتح الحزمة
افتح القفل للوصول البطاقات البالغ عددها 52 في هذه المجموعة.
فتح الحزمة
k this deck
18
This identifies the specific materials used to make each item and the correct quantities of each.
فتح الحزمة
افتح القفل للوصول البطاقات البالغ عددها 52 في هذه المجموعة.
فتح الحزمة
k this deck
19
State the types of data that would be carried in the bill-of-materials fi le and the inventory record file.
فتح الحزمة
افتح القفل للوصول البطاقات البالغ عددها 52 في هذه المجموعة.
فتح الحزمة
k this deck
20
What is another common name for the bill-of-materials?
فتح الحزمة
افتح القفل للوصول البطاقات البالغ عددها 52 في هذه المجموعة.
فتح الحزمة
k this deck
21
If an item is used in two places in a bill-of-materials, say level 3 and level 4, what low-level code would be assigned to the item?
فتح الحزمة
افتح القفل للوصول البطاقات البالغ عددها 52 في هذه المجموعة.
فتح الحزمة
k this deck
22
Discuss the meaning of MRP terms such as planned order release and scheduled order receipt.
فتح الحزمة
افتح القفل للوصول البطاقات البالغ عددها 52 في هذه المجموعة.
فتح الحزمة
k this deck
23
What is the process used to ensure that all of the needs for a particular item are calculated at the same time in the MRP process?
فتح الحزمة
افتح القفل للوصول البطاقات البالغ عددها 52 في هذه المجموعة.
فتح الحزمة
k this deck
24
One unit of Part C is used in item A and in item B. Currently, we have 10 As, 20 Bs, and 100 Cs in inventory. We want to ship 60 As and 70 Bs. How many additional Cs do we need to purchase?
فتح الحزمة
افتح القفل للوصول البطاقات البالغ عددها 52 في هذه المجموعة.
فتح الحزمة
k this deck
25
Why is the MRP process referred to as an "explosion"?
فتح الحزمة
افتح القفل للوصول البطاقات البالغ عددها 52 في هذه المجموعة.
فتح الحزمة
k this deck
26
What is the MRP term for the time periods used in planning?
فتح الحزمة
افتح القفل للوصول البطاقات البالغ عددها 52 في هذه المجموعة.
فتح الحزمة
k this deck
27
These are orders that have already been released and are to arrive in the future.
فتح الحزمة
افتح القفل للوصول البطاقات البالغ عددها 52 في هذه المجموعة.
فتح الحزمة
k this deck
28
Many practitioners currently update MRP weekly or biweekly. Would it be more valuable if it were updated daily? Discuss.
فتح الحزمة
افتح القفل للوصول البطاقات البالغ عددها 52 في هذه المجموعة.
فتح الحزمة
k this deck
29
Note: For these problems, to simplify data handling to include the receipt of orders that have actually been placed in previous periods, the following six-level scheme can be used. (A number of different techniques are used in practice, but the important issue is to keep track of what is on hand, what is expected to arrive, what is needed, and what size orders should be placed.) One way to calculate the numbers is as follows:
Semans is a manufacturer that produces bracket assemblies. Demand for bracket assemblies (X) is 130 units. The following is the BOM in indented form:
a. Using Excel, create the MRP using the information provided.
b. What are the net requirements of each item in the MPS?
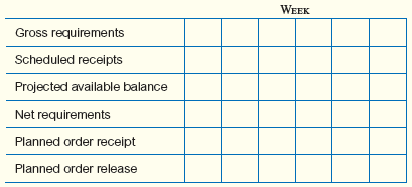
Semans is a manufacturer that produces bracket assemblies. Demand for bracket assemblies (X) is 130 units. The following is the BOM in indented form:
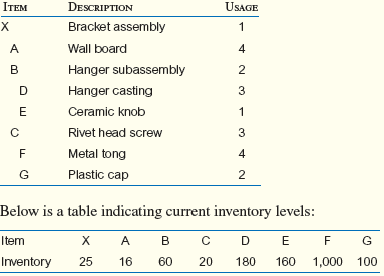
a. Using Excel, create the MRP using the information provided.
b. What are the net requirements of each item in the MPS?
فتح الحزمة
افتح القفل للوصول البطاقات البالغ عددها 52 في هذه المجموعة.
فتح الحزمة
k this deck
30
This is the total amount required for a particular item.
فتح الحزمة
افتح القفل للوصول البطاقات البالغ عددها 52 في هذه المجموعة.
فتح الحزمة
k this deck
31
Should safety stock be necessary in an MRP system with dependent demand? If so, why? If not, why do firms carry it anyway?
فتح الحزمة
افتح القفل للوصول البطاقات البالغ عددها 52 في هذه المجموعة.
فتح الحزمة
k this deck
32
Note: For these problems, to simplify data handling to include the receipt of orders that have actually been placed in previous periods, the following six-level scheme can be used. (A number of different techniques are used in practice, but the important issue is to keep track of what is on hand, what is expected to arrive, what is needed, and what size orders should be placed.) One way to calculate the numbers is as follows:
In the following MRP planning schedule for Item J, indicate the correct net requirements, planned order receipts, and planned order releases to meet the gross requirements. Lead time is one week.
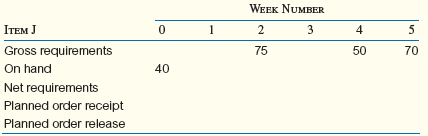
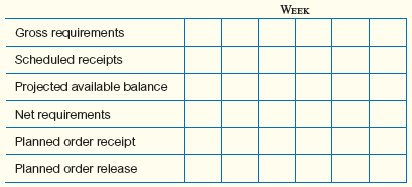
In the following MRP planning schedule for Item J, indicate the correct net requirements, planned order receipts, and planned order releases to meet the gross requirements. Lead time is one week.
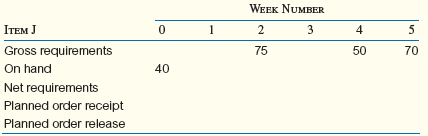
فتح الحزمة
افتح القفل للوصول البطاقات البالغ عددها 52 في هذه المجموعة.
فتح الحزمة
k this deck
33
This is the amount needed after considering what we currently have in inventory and what we expect to arrive in the future.
فتح الحزمة
افتح القفل للوصول البطاقات البالغ عددها 52 في هذه المجموعة.
فتح الحزمة
k this deck
34
Contrast the significance of the term lead time in the traditional EOQ context and in an MRP system.
فتح الحزمة
افتح القفل للوصول البطاقات البالغ عددها 52 في هذه المجموعة.
فتح الحزمة
k this deck
35
Note: For these problems, to simplify data handling to include the receipt of orders that have actually been placed in previous periods, the following six-level scheme can be used. (A number of different techniques are used in practice, but the important issue is to keep track of what is on hand, what is expected to arrive, what is needed, and what size orders should be placed.) One way to calculate the numbers is as follows:
Assume that Product Z is made of two units of A and four units of B. A is made of three units of C and four of D. D is made of two units of E.
Lead times for purchase or fabrication of each unit to final assembly are: Z takes two weeks; A, B, C, and D take one week each; and E takes three weeks.
Fifty units are required in Period 10. (Assume that there is currently no inventory on hand of any of these items.)
a. Show the bill-of-materials (product structure tree).
b. Develop an MRP planning schedule showing gross and net requirements and order release and order receipt dates.
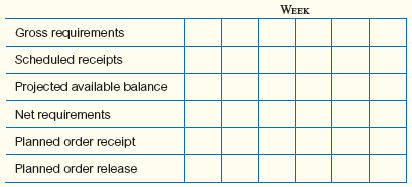
Assume that Product Z is made of two units of A and four units of B. A is made of three units of C and four of D. D is made of two units of E.
Lead times for purchase or fabrication of each unit to final assembly are: Z takes two weeks; A, B, C, and D take one week each; and E takes three weeks.
Fifty units are required in Period 10. (Assume that there is currently no inventory on hand of any of these items.)
a. Show the bill-of-materials (product structure tree).
b. Develop an MRP planning schedule showing gross and net requirements and order release and order receipt dates.
فتح الحزمة
افتح القفل للوصول البطاقات البالغ عددها 52 في هذه المجموعة.
فتح الحزمة
k this deck
36
The planned order receipt and planned order release are offset by this amount of time.
فتح الحزمة
افتح القفل للوصول البطاقات البالغ عددها 52 في هذه المجموعة.
فتح الحزمة
k this deck
37
Planning orders using a lot-for-lot (L4L) technique is commonly done because it is simple and intuitive. It also helps to minimize holding costs as you are only ordering what is needed when it is needed. So far it sounds like a good idea. Are there any disadvantages to this approach?
فتح الحزمة
افتح القفل للوصول البطاقات البالغ عددها 52 في هذه المجموعة.
فتح الحزمة
k this deck
38
Note: For these problems, to simplify data handling to include the receipt of orders that have actually been placed in previous periods, the following six-level scheme can be used. (A number of different techniques are used in practice, but the important issue is to keep track of what is on hand, what is expected to arrive, what is needed, and what size orders should be placed.) One way to calculate the numbers is as follows:
One unit of A is made of three units of B, one unit of C, and two units of D. B is composed of two units of E and one unit of D. C is made of one unit of B and two units of E. E is made of one unit of F.
Items B, C, E, and F have one-week lead times; A and D have lead times of two weeks.
Assume that lot-for-lot (L4L) lot sizing is used for Items A, B, and F; lots of size 50, 50, and 200 are used for Items C, D, and E, respectively. Items C, E, and F have onhand (beginning) inventories of 10, 50, and 150, respectively; all other items have zero beginning inventory. We are scheduled to receive 10 units of A in Week 2, 50 units of E in Week 1, and also 50 units of F in Week 1. There are no other scheduled receipts. If 30 units of A are required in Week 8, use the low-level-coded bill-of-materials to find the necessary planned order releases for all components.
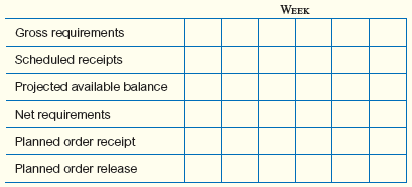
One unit of A is made of three units of B, one unit of C, and two units of D. B is composed of two units of E and one unit of D. C is made of one unit of B and two units of E. E is made of one unit of F.
Items B, C, E, and F have one-week lead times; A and D have lead times of two weeks.
Assume that lot-for-lot (L4L) lot sizing is used for Items A, B, and F; lots of size 50, 50, and 200 are used for Items C, D, and E, respectively. Items C, E, and F have onhand (beginning) inventories of 10, 50, and 150, respectively; all other items have zero beginning inventory. We are scheduled to receive 10 units of A in Week 2, 50 units of E in Week 1, and also 50 units of F in Week 1. There are no other scheduled receipts. If 30 units of A are required in Week 8, use the low-level-coded bill-of-materials to find the necessary planned order releases for all components.
فتح الحزمة
افتح القفل للوصول البطاقات البالغ عددها 52 في هذه المجموعة.
فتح الحزمة
k this deck
39
These are the part quantities issued in the planned order release section of an MRP report.
فتح الحزمة
افتح القفل للوصول البطاقات البالغ عددها 52 في هذه المجموعة.
فتح الحزمة
k this deck
40
What is meant when we say that the least total cost (LTC) and least unit cost (LUC) methods are dynamic lot-sizing techniques?
فتح الحزمة
افتح القفل للوصول البطاقات البالغ عددها 52 في هذه المجموعة.
فتح الحزمة
k this deck
41
Note: For these problems, to simplify data handling to include the receipt of orders that have actually been placed in previous periods, the following six-level scheme can be used. (A number of different techniques are used in practice, but the important issue is to keep track of what is on hand, what is expected to arrive, what is needed, and what size orders should be placed.) One way to calculate the numbers is as follows:
One unit of A is made of two units of B, three units of C, and two units of D. B is composed of one unit of E and two units of F. C is made of two units of F and one unit of D. E is made of two units of D. Items A, C, D, and F have one-week lead times; B and E have lead times of two weeks. Lot-for-lot (L4L) lot sizing is used for Items A, B, C, and D; lots of size 50 and 180 are used for Items E and F, respectively. Item C has an on-hand (beginning) inventory of 15; D has an on-hand inventory of 50; all other items have zero beginning inventories. We are scheduled to receive 20 units of Item E in Week 2; there are no other scheduled receipts.
Construct simple and low-level-coded bill-of-materials (product structure tree) and indented and summarized parts lists.
If 20 units of A are required in Week 8, use the low-level-coded bill-of-materials to find the necessary planned order releases for all components.
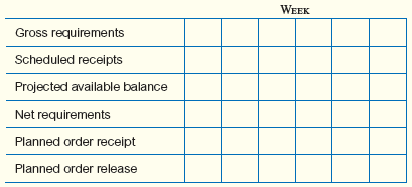
One unit of A is made of two units of B, three units of C, and two units of D. B is composed of one unit of E and two units of F. C is made of two units of F and one unit of D. E is made of two units of D. Items A, C, D, and F have one-week lead times; B and E have lead times of two weeks. Lot-for-lot (L4L) lot sizing is used for Items A, B, C, and D; lots of size 50 and 180 are used for Items E and F, respectively. Item C has an on-hand (beginning) inventory of 15; D has an on-hand inventory of 50; all other items have zero beginning inventories. We are scheduled to receive 20 units of Item E in Week 2; there are no other scheduled receipts.
Construct simple and low-level-coded bill-of-materials (product structure tree) and indented and summarized parts lists.
If 20 units of A are required in Week 8, use the low-level-coded bill-of-materials to find the necessary planned order releases for all components.
فتح الحزمة
افتح القفل للوصول البطاقات البالغ عددها 52 في هذه المجموعة.
فتح الحزمة
k this deck
42
Ordering exactly what is needed each period without regard to economic considerations.
فتح الحزمة
افتح القفل للوصول البطاقات البالغ عددها 52 في هذه المجموعة.
فتح الحزمة
k this deck
43
Note: For these problems, to simplify data handling to include the receipt of orders that have actually been placed in previous periods, the following six-level scheme can be used. (A number of different techniques are used in practice, but the important issue is to keep track of what is on hand, what is expected to arrive, what is needed, and what size orders should be placed.) One way to calculate the numbers is as follows:
One unit of A is made of one unit of B and one unit of C. B is made of four units of C and one unit each of E and F. C is made of two units of D and one unit of E. E is made of three units of F. Item C has a lead time of one week; Items A, B, E, and F have two-week lead times; and Item D has a lead time of three weeks. Lot-for-lot (L4L) lot sizing is used for Items A, D, and E; lots of size 50, 100, and 50 are used for Items B, C, and F, respectively. Items A, C, D, and E have on-hand (beginning) inventories of 20, 50, 100, and 10, respectively; all other items have zero beginning inventory. We are scheduled to receive 10 units of A in Week 1, 100 units of C in Week 1, and 100 units of D in Week 3; there are no other scheduled receipts. If 50 units of A are required in Week 10, use the low-level-coded bill-of-materials (product structure tree) to find the necessary planned order releases for all components.
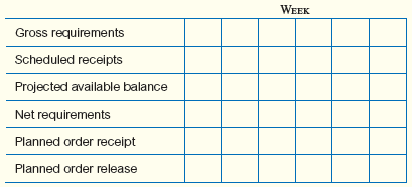
One unit of A is made of one unit of B and one unit of C. B is made of four units of C and one unit each of E and F. C is made of two units of D and one unit of E. E is made of three units of F. Item C has a lead time of one week; Items A, B, E, and F have two-week lead times; and Item D has a lead time of three weeks. Lot-for-lot (L4L) lot sizing is used for Items A, D, and E; lots of size 50, 100, and 50 are used for Items B, C, and F, respectively. Items A, C, D, and E have on-hand (beginning) inventories of 20, 50, 100, and 10, respectively; all other items have zero beginning inventory. We are scheduled to receive 10 units of A in Week 1, 100 units of C in Week 1, and 100 units of D in Week 3; there are no other scheduled receipts. If 50 units of A are required in Week 10, use the low-level-coded bill-of-materials (product structure tree) to find the necessary planned order releases for all components.
فتح الحزمة
افتح القفل للوصول البطاقات البالغ عددها 52 في هذه المجموعة.
فتح الحزمة
k this deck
44
None of the techniques for determining order quantity consider this important noneconomic factor that could make the order quantity infeasible.
فتح الحزمة
افتح القفل للوصول البطاقات البالغ عددها 52 في هذه المجموعة.
فتح الحزمة
k this deck
45
Note: For these problems, to simplify data handling to include the receipt of orders that have actually been placed in previous periods, the following six-level scheme can be used. (A number of different techniques are used in practice, but the important issue is to keep track of what is on hand, what is expected to arrive, what is needed, and what size orders should be placed.) One way to calculate the numbers is as follows:
One unit of A is made of two units of B and one unit of C. B is made of three units of D and one unit of F. C is composed of three units of B, one unit of D, and four units of E. D is made of one unit of E. Item C has a lead time of one week; Items A, B, E, and F have two-week lead times; and Item D has a lead time of three weeks. Lot-for-lot (L4L) lot sizing is used for Items C, E, and F; lots of size 20, 40, and 160 are used for Items A, B, and D, respectively. Items A, B, D, and E have on-hand (beginning) inventories of 5, 10, 100, and 100, respectively; all other items have zero beginning inventories. We are scheduled to receive 10 units of A in Week 3, 20 units of B in Week 7, 40 units of F in Week 5, and 60 units of E in Week 2; there are no other scheduled receipts. If 20 units of A are required in Week 10, use the low-level-coded bill-of-materials (product structure tree) to find the necessary planned order releases for all components.
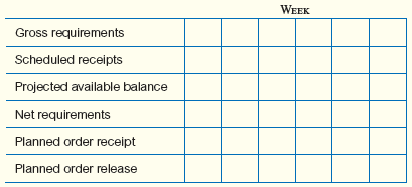
One unit of A is made of two units of B and one unit of C. B is made of three units of D and one unit of F. C is composed of three units of B, one unit of D, and four units of E. D is made of one unit of E. Item C has a lead time of one week; Items A, B, E, and F have two-week lead times; and Item D has a lead time of three weeks. Lot-for-lot (L4L) lot sizing is used for Items C, E, and F; lots of size 20, 40, and 160 are used for Items A, B, and D, respectively. Items A, B, D, and E have on-hand (beginning) inventories of 5, 10, 100, and 100, respectively; all other items have zero beginning inventories. We are scheduled to receive 10 units of A in Week 3, 20 units of B in Week 7, 40 units of F in Week 5, and 60 units of E in Week 2; there are no other scheduled receipts. If 20 units of A are required in Week 10, use the low-level-coded bill-of-materials (product structure tree) to find the necessary planned order releases for all components.
فتح الحزمة
افتح القفل للوصول البطاقات البالغ عددها 52 في هذه المجموعة.
فتح الحزمة
k this deck
46
Note: For these problems, to simplify data handling to include the receipt of orders that have actually been placed in previous periods, the following six-level scheme can be used. (A number of different techniques are used in practice, but the important issue is to keep track of what is on hand, what is expected to arrive, what is needed, and what size orders should be placed.) One way to calculate the numbers is as follows:
One unit of A is composed of two units of B and three units of C. Each B is composed of one unit of F. C is made of one unit of D, one unit of E, and two units of F. Items A, B, C, and D have 20, 50, 60, and 25 units of on-hand inventory, respectively. Items A, B, and C use lot-for-lot (L4L) as their lot-sizing technique, while D, E, and F require multiples of 50, 100, and 100, respectively, to be purchased. B has scheduled receipts of 30 units in Period 1. No other scheduled receipts exist. Lead times are one period for Items A, B, and D, and two periods for Items C, E, and F. Gross requirements for A are 20 units in Period 1, 20 units in Period 2, 60 units in Period 6, and 50 units in Period 8. Find the planned order releases for all items.
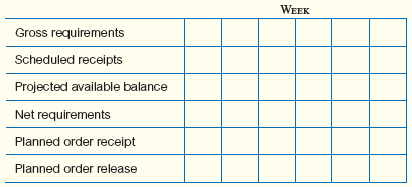
One unit of A is composed of two units of B and three units of C. Each B is composed of one unit of F. C is made of one unit of D, one unit of E, and two units of F. Items A, B, C, and D have 20, 50, 60, and 25 units of on-hand inventory, respectively. Items A, B, and C use lot-for-lot (L4L) as their lot-sizing technique, while D, E, and F require multiples of 50, 100, and 100, respectively, to be purchased. B has scheduled receipts of 30 units in Period 1. No other scheduled receipts exist. Lead times are one period for Items A, B, and D, and two periods for Items C, E, and F. Gross requirements for A are 20 units in Period 1, 20 units in Period 2, 60 units in Period 6, and 50 units in Period 8. Find the planned order releases for all items.
فتح الحزمة
افتح القفل للوصول البطاقات البالغ عددها 52 في هذه المجموعة.
فتح الحزمة
k this deck
47
Note: For these problems, to simplify data handling to include the receipt of orders that have actually been placed in previous periods, the following six-level scheme can be used. (A number of different techniques are used in practice, but the important issue is to keep track of what is on hand, what is expected to arrive, what is needed, and what size orders should be placed.) One way to calculate the numbers is as follows:
Each unit of A is composed of one unit of B, two units of C, and one unit of D. C is composed of two units of D and three units of E. Items A, C, D, and E have on-hand inventories of 20, 10, 20, and 10 units, respectively. Item B has a scheduled receipt of 10 units in Period 1, and C has a scheduled receipt of 50 units in Period 1. Lot-for-lot (L4L) lot sizing is used for Items A and B. Item C requires a minimum lot size of 50 units. D and E are required to be purchased in multiples of 100 and 50, respectively. Lead times are one period for Items A, B, and C, and two periods for Items D and E. The gross requirements for A are 30 in Period 2, 30 in Period 5, and 40 in Period 8. Find the planned order releases for all items.
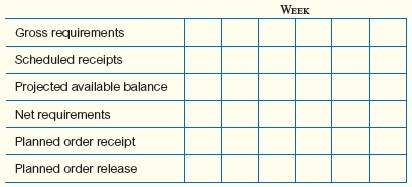
Each unit of A is composed of one unit of B, two units of C, and one unit of D. C is composed of two units of D and three units of E. Items A, C, D, and E have on-hand inventories of 20, 10, 20, and 10 units, respectively. Item B has a scheduled receipt of 10 units in Period 1, and C has a scheduled receipt of 50 units in Period 1. Lot-for-lot (L4L) lot sizing is used for Items A and B. Item C requires a minimum lot size of 50 units. D and E are required to be purchased in multiples of 100 and 50, respectively. Lead times are one period for Items A, B, and C, and two periods for Items D and E. The gross requirements for A are 30 in Period 2, 30 in Period 5, and 40 in Period 8. Find the planned order releases for all items.
فتح الحزمة
افتح القفل للوصول البطاقات البالغ عددها 52 في هذه المجموعة.
فتح الحزمة
k this deck
48
Note: For these problems, to simplify data handling to include the receipt of orders that have actually been placed in previous periods, the following six-level scheme can be used. (A number of different techniques are used in practice, but the important issue is to keep track of what is on hand, what is expected to arrive, what is needed, and what size orders should be placed.) One way to calculate the numbers is as follows:
Product A is an end item and is made from two units of B and four of C. B is made of three units of D and two of E. C is made of two units of F and two of E.
A has a lead time of one week. B, C, and E have lead times of two weeks, and D and F have lead times of three weeks.
a. Show the bill-of-materials (product structure tree).
b. If 100 units of A are required in Week 10, develop the MRP planning schedule, specifying when items are to be ordered and received. There are currently no units of inventory on hand.
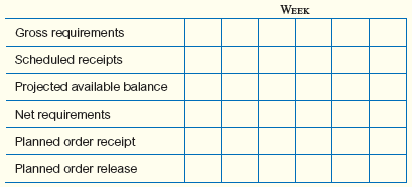
Product A is an end item and is made from two units of B and four of C. B is made of three units of D and two of E. C is made of two units of F and two of E.
A has a lead time of one week. B, C, and E have lead times of two weeks, and D and F have lead times of three weeks.
a. Show the bill-of-materials (product structure tree).
b. If 100 units of A are required in Week 10, develop the MRP planning schedule, specifying when items are to be ordered and received. There are currently no units of inventory on hand.
فتح الحزمة
افتح القفل للوصول البطاقات البالغ عددها 52 في هذه المجموعة.
فتح الحزمة
k this deck
49
Note: For these problems, to simplify data handling to include the receipt of orders that have actually been placed in previous periods, the following six-level scheme can be used. (A number of different techniques are used in practice, but the important issue is to keep track of what is on hand, what is expected to arrive, what is needed, and what size orders should be placed.) One way to calculate the numbers is as follows:
Audio Products, Inc., produces two AM/FM/CD players for cars. The radio/CD units are identical, but the mounting hardware and finish trim differ. The standard model fits intermediate and full-size cars, and the sports model fits small sports cars.
Audio Products handles the production in the following way. The chassis (radio/ CD unit) is assembled in Mexico and has a manufacturing lead time of two weeks. The mounting hardware is purchased from a sheet steel company and has a three-week lead time. The finish trim is purchased as prepackaged units consisting of knobs and various trim pieces from a Taiwan electronics company with offices in Los Angeles. Trim packages have a two-week lead time. Final assembly time may be disregarded because adding the trim package and mounting are performed by the customer.
Audio Products supplies wholesalers and retailers, which place specific orders for both models up to eight weeks in advance. These orders, together with enough additional units to satisfy the small number of individual sales, are summarized in the following demand schedule:
There are currently 50 radio/CD units on hand but no trim packages or mounting hardware.
Prepare a material requirements plan to meet the demand schedule exactly. Specify the gross and net requirements, on-hand amounts, and the planned order release and receipt periods for the radio/CD chassis, the standard trim and sports car model trim, and the standard mounting hardware and the sports car mounting hardware.
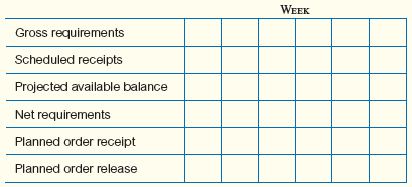
Audio Products, Inc., produces two AM/FM/CD players for cars. The radio/CD units are identical, but the mounting hardware and finish trim differ. The standard model fits intermediate and full-size cars, and the sports model fits small sports cars.
Audio Products handles the production in the following way. The chassis (radio/ CD unit) is assembled in Mexico and has a manufacturing lead time of two weeks. The mounting hardware is purchased from a sheet steel company and has a three-week lead time. The finish trim is purchased as prepackaged units consisting of knobs and various trim pieces from a Taiwan electronics company with offices in Los Angeles. Trim packages have a two-week lead time. Final assembly time may be disregarded because adding the trim package and mounting are performed by the customer.
Audio Products supplies wholesalers and retailers, which place specific orders for both models up to eight weeks in advance. These orders, together with enough additional units to satisfy the small number of individual sales, are summarized in the following demand schedule:

There are currently 50 radio/CD units on hand but no trim packages or mounting hardware.
Prepare a material requirements plan to meet the demand schedule exactly. Specify the gross and net requirements, on-hand amounts, and the planned order release and receipt periods for the radio/CD chassis, the standard trim and sports car model trim, and the standard mounting hardware and the sports car mounting hardware.
فتح الحزمة
افتح القفل للوصول البطاقات البالغ عددها 52 في هذه المجموعة.
فتح الحزمة
k this deck
50
The MRP gross requirements for Item A are shown here for the next 10 weeks. Lead time for A is three weeks and setup cost is $10. There is a carrying cost of $0.01 per unit per week. Beginning inventory is 90 units.
Use the least total cost or the least unit cost lot-sizing method to determine when and for what quantity the first order should be released.
Least Total Cost Method Reference:
Least Unit Cost Method for Reference:
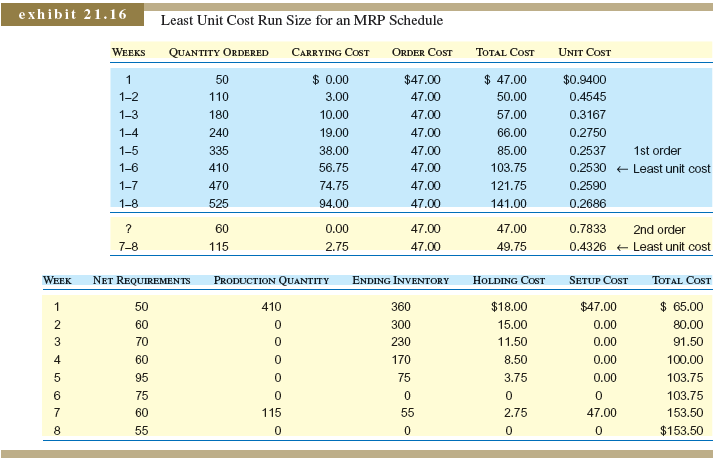

Use the least total cost or the least unit cost lot-sizing method to determine when and for what quantity the first order should be released.
Least Total Cost Method Reference:
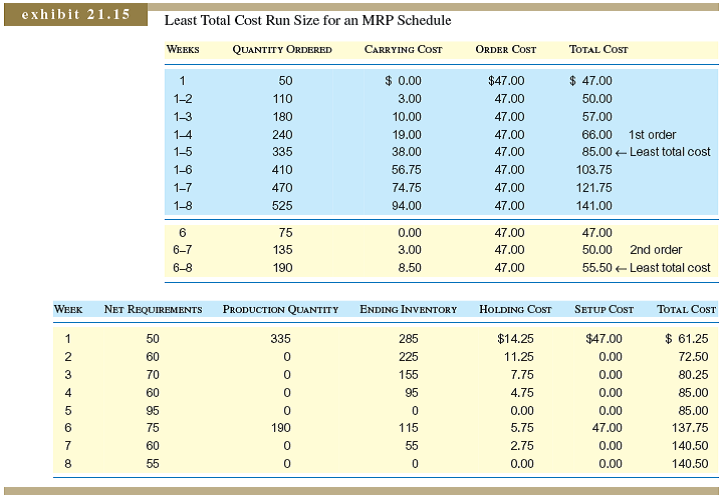
Least Unit Cost Method for Reference:
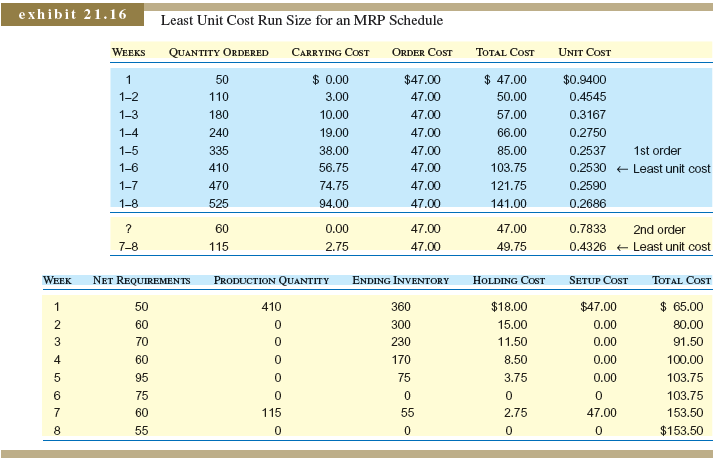
فتح الحزمة
افتح القفل للوصول البطاقات البالغ عددها 52 في هذه المجموعة.
فتح الحزمة
k this deck
51
The MRP gross requirements for Item X are shown here for the next 10 weeks. Lead time for A is two weeks, and setup cost is $9. There is a carrying cost of $0.02 per unit per week. Beginning inventory is 70 units.
Use the least total cost or the least unit cost lot-sizing method to determine when and for what quantity the first order should be released.
Least Total Cost Method Reference:
Least Unit Cost Method for Reference:
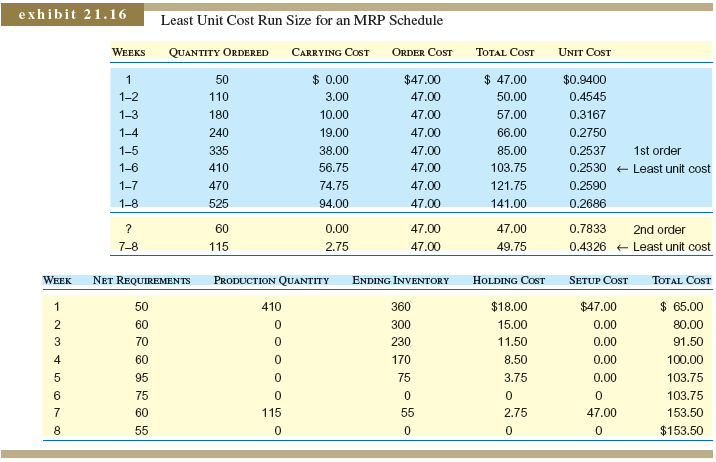

Use the least total cost or the least unit cost lot-sizing method to determine when and for what quantity the first order should be released.
Least Total Cost Method Reference:
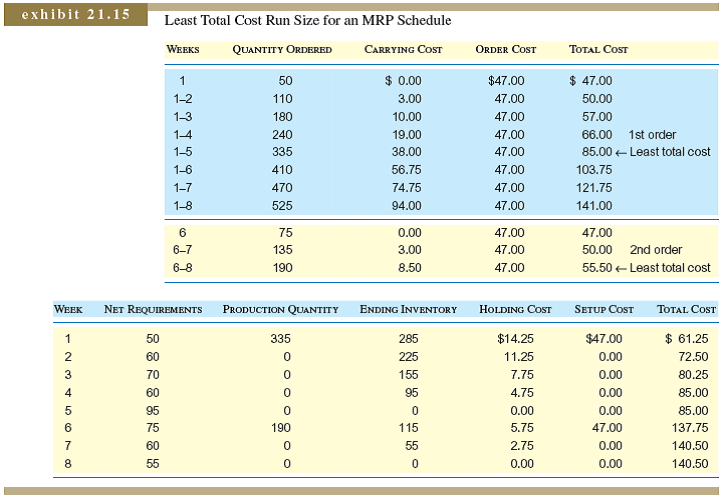
Least Unit Cost Method for Reference:
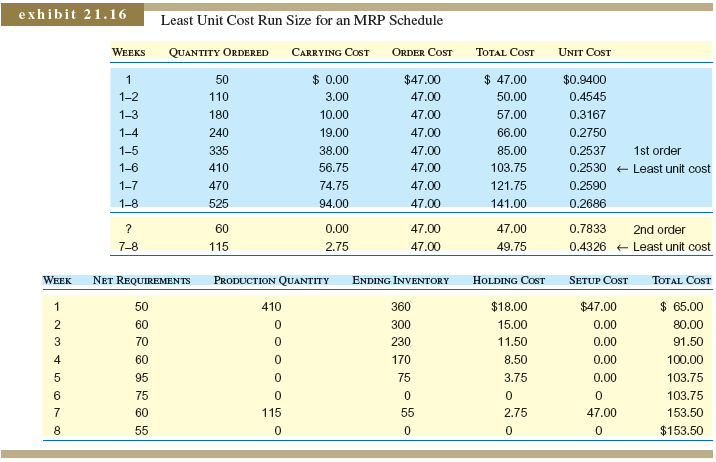
فتح الحزمة
افتح القفل للوصول البطاقات البالغ عددها 52 في هذه المجموعة.
فتح الحزمة
k this deck
52
Product A consists of two units of Subassembly B, three units of C, and one unit of D. B is composed of four units of E and three units of F. C is made of two units of H and three units of D. H is made of five units of E and two units of G.
a. Construct a simple bill-of-materials (product structure tree).
b. Construct a product structure tree using low-level coding.
c. Construct an indented parts list.
d. To produce 100 units of A, determine the number of units of B, C, D, E, F, G, and H required.
a. Construct a simple bill-of-materials (product structure tree).
b. Construct a product structure tree using low-level coding.
c. Construct an indented parts list.
d. To produce 100 units of A, determine the number of units of B, C, D, E, F, G, and H required.
فتح الحزمة
افتح القفل للوصول البطاقات البالغ عددها 52 في هذه المجموعة.
فتح الحزمة
k this deck