Deck 7: Activity-Based Costing and Management
سؤال
سؤال
سؤال
سؤال
سؤال
سؤال
سؤال
سؤال
سؤال
سؤال
سؤال
سؤال
سؤال
سؤال
سؤال
سؤال
سؤال
سؤال
سؤال
سؤال
سؤال
سؤال
سؤال
سؤال
سؤال
سؤال
سؤال
سؤال
سؤال
سؤال
سؤال
سؤال
سؤال
سؤال
سؤال
سؤال
سؤال
سؤال
سؤال
سؤال
سؤال
سؤال
سؤال
سؤال
سؤال
سؤال
سؤال
سؤال
سؤال
سؤال
سؤال
سؤال
سؤال
سؤال
سؤال
سؤال
سؤال
سؤال
سؤال
سؤال
سؤال
سؤال
سؤال
سؤال
سؤال
سؤال
سؤال
سؤال
سؤال
سؤال
سؤال
سؤال
سؤال
سؤال
سؤال
سؤال
سؤال
سؤال
سؤال
سؤال
فتح الحزمة
قم بالتسجيل لفتح البطاقات في هذه المجموعة!
Unlock Deck
Unlock Deck
1/80
العب
ملء الشاشة (f)
Deck 7: Activity-Based Costing and Management
1
Interview questions are asked to determine
A) what activities are being performed.
B) who performs the activities.
C) the relative amount of time spent on each activity by individual workers.
D) possible activity drivers for assigning costs to products.
E) All of these.
A) what activities are being performed.
B) who performs the activities.
C) the relative amount of time spent on each activity by individual workers.
D) possible activity drivers for assigning costs to products.
E) All of these.
Option e is the correct answer.
Interview questions are asked to gather all of the following information:
1. What activities are performed?
2. Who performs the activities
3. The amount of relative amount of time spent on each activity by individual workers
4. Possible activity drivers for assigning costs to products.
Interview questions are asked to gather all of the following information:
1. What activities are performed?
2. Who performs the activities
3. The amount of relative amount of time spent on each activity by individual workers
4. Possible activity drivers for assigning costs to products.
2
Which of the following are nonvalue-added activities?
A) Moving goods
B) Storing goods
C) Inspecting finished goods
D) Reworking a defective product
E) All of these.
A) Moving goods
B) Storing goods
C) Inspecting finished goods
D) Reworking a defective product
E) All of these.
Option e is the correct answer.
All of these are non value added activities:
a. Moving goods
b. Storing goods
c. Inspecting finished goods
d. Reworking a defective product
All of these are non value added activities:
a. Moving goods
b. Storing goods
c. Inspecting finished goods
d. Reworking a defective product
3
Calculating ABC Unit Costs
Perry National Bank has collected the following information for four activities and two types of credit cards:
There are 5,000 holders of Classic cards and 20,000 holders of the Gold cards.
Required:
Calculate the unit cost (rounded to the nearest cent) for Classic and Gold credit cards.
Perry National Bank has collected the following information for four activities and two types of credit cards:

There are 5,000 holders of Classic cards and 20,000 holders of the Gold cards.
Required:
Calculate the unit cost (rounded to the nearest cent) for Classic and Gold credit cards.
Calculation of unit cost for Classic and Gold credit cards:
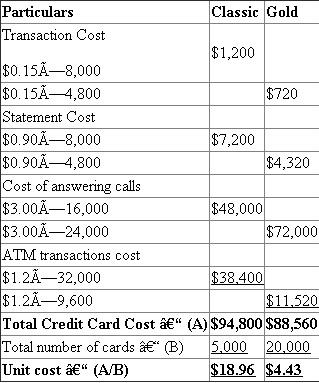
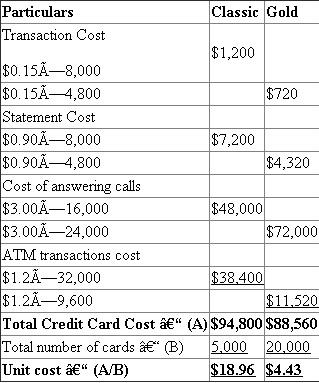
4
Cycle Time and Velocity
In the first quarter of operations, a manufacturing cell produced 80,000 stereo speakers, using 20,000 production hours. In the second quarter, the cycle time was 10 minutes per unit with the same number of production hours as were used in the first quarter.
Required:
1. Compute the velocity (per hour) for the first quarter.
2. Compute the cycle time for the first quarter (minutes per unit produced).
3. How many units were produced in the second quarter?
In the first quarter of operations, a manufacturing cell produced 80,000 stereo speakers, using 20,000 production hours. In the second quarter, the cycle time was 10 minutes per unit with the same number of production hours as were used in the first quarter.
Required:
1. Compute the velocity (per hour) for the first quarter.
2. Compute the cycle time for the first quarter (minutes per unit produced).
3. How many units were produced in the second quarter?
فتح الحزمة
افتح القفل للوصول البطاقات البالغ عددها 80 في هذه المجموعة.
فتح الحزمة
k this deck
5
Classification of Environmental Costs
Consider the following independent environmental activities:
a. A company takes actions to reduce the amount of material in its packages.
b. After its useful life, a soft-drink producer returns the activated carbon used for purifying water for its beverages to the supplier. The supplier reactivates the carbon for a second use in nonfood applications. As a consequence, many tons of material are prevented from entering landfills.
c. An evaporator system is installed to treat wastewater and to collect usable solids for other uses.
d. The inks used to print snack packages (for chips) contain heavy metals.
e. Processes are inspected to ensure compliance with environmental standards.
f. Delivery boxes are used five times and then recycled. This prevents 112 million pounds of cardboard from entering landfills and saves two million trees per year.
g. Scrubber equipment is installed to ensure that air emissions are less than the level permitted by law.
h. Local residents are incurring medical costs from illnesses caused by air pollution from automobile exhaust pollution.
i. As part of implementing an environmental perspective for a balanced performance measurement system, environmental performance measures are developed.
j. Because of liquid and solid residues being discharged into a local lake, it is no longer fit for swimming, fishing, and other recreational activities.
k. To reduce energy consumption, magnetic ballasts are replaced with electronic ballasts, and more efficient light bulbs and lighting sensors are installed. As a result, 2.3 million kilowatthours of electricity are saved per year.
l. Because of a legal settlement, a chemical company must spend $20,000,000 to clean up contaminated soil.
m. A soft-drink company uses the following practice: In all bottling plants, packages damaged during filling are collected and recycled (glass, plastic, and aluminum).
n. Products are inspected to ensure that the gaseous emissions produced during operation follow legal and company guidelines.
o. Costs are incurred to operate pollution-control equipment.
p. An internal audit is conducted to verify that environmental policies are being followed.
Required:
Classify these environmental activities as prevention, detection, internal failure, or external failure costs. For external failure costs, classify the costs as societal or realized. Also, label those activities that are compatible with sustainable development with ''SD.''
Consider the following independent environmental activities:
a. A company takes actions to reduce the amount of material in its packages.
b. After its useful life, a soft-drink producer returns the activated carbon used for purifying water for its beverages to the supplier. The supplier reactivates the carbon for a second use in nonfood applications. As a consequence, many tons of material are prevented from entering landfills.
c. An evaporator system is installed to treat wastewater and to collect usable solids for other uses.
d. The inks used to print snack packages (for chips) contain heavy metals.
e. Processes are inspected to ensure compliance with environmental standards.
f. Delivery boxes are used five times and then recycled. This prevents 112 million pounds of cardboard from entering landfills and saves two million trees per year.
g. Scrubber equipment is installed to ensure that air emissions are less than the level permitted by law.
h. Local residents are incurring medical costs from illnesses caused by air pollution from automobile exhaust pollution.
i. As part of implementing an environmental perspective for a balanced performance measurement system, environmental performance measures are developed.
j. Because of liquid and solid residues being discharged into a local lake, it is no longer fit for swimming, fishing, and other recreational activities.
k. To reduce energy consumption, magnetic ballasts are replaced with electronic ballasts, and more efficient light bulbs and lighting sensors are installed. As a result, 2.3 million kilowatthours of electricity are saved per year.
l. Because of a legal settlement, a chemical company must spend $20,000,000 to clean up contaminated soil.
m. A soft-drink company uses the following practice: In all bottling plants, packages damaged during filling are collected and recycled (glass, plastic, and aluminum).
n. Products are inspected to ensure that the gaseous emissions produced during operation follow legal and company guidelines.
o. Costs are incurred to operate pollution-control equipment.
p. An internal audit is conducted to verify that environmental policies are being followed.
Required:
Classify these environmental activities as prevention, detection, internal failure, or external failure costs. For external failure costs, classify the costs as societal or realized. Also, label those activities that are compatible with sustainable development with ''SD.''
فتح الحزمة
افتح القفل للوصول البطاقات البالغ عددها 80 في هذه المجموعة.
فتح الحزمة
k this deck
6
Explain how costs are assigned to activities.
فتح الحزمة
افتح القفل للوصول البطاقات البالغ عددها 80 في هذه المجموعة.
فتح الحزمة
k this deck
7
Suppose that a company is spending $60,000 per year for inspecting, $30,000 for purchasing, and $40,000 for reworking products. A good estimate of nonvalue-added costs would be
A) $70,000.
B) $130,000.
C) $40,000.
D) $90,000.
E) $100,000.
A) $70,000.
B) $130,000.
C) $40,000.
D) $90,000.
E) $100,000.
فتح الحزمة
افتح القفل للوصول البطاقات البالغ عددها 80 في هذه المجموعة.
فتح الحزمة
k this deck
8
Assigning Costs to Activities
Baker Company produces small engines for lawnmower producers. The accounts payable department at Baker has six clerks who process and pay supplier invoices. The total cost of their salaries is $320,000. The work distribution for the activities that they perform is as follows:
Required:
Assign the cost of labor to each of the three activities in the accounts payable department.
Baker Company produces small engines for lawnmower producers. The accounts payable department at Baker has six clerks who process and pay supplier invoices. The total cost of their salaries is $320,000. The work distribution for the activities that they perform is as follows:
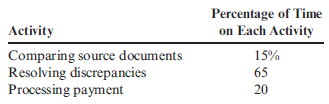
Required:
Assign the cost of labor to each of the three activities in the accounts payable department.
فتح الحزمة
افتح القفل للوصول البطاقات البالغ عددها 80 في هذه المجموعة.
فتح الحزمة
k this deck
9
Product-Costing Accuracy, Consumption Ratios
Plata Company produces two products: a mostly handcrafted soft leather briefcase sold under the label Maletin Elegant and a leather briefcase produced largely through automation and sold under the label Maletin Fina. The two products use two overhead activities, with the following costs:
The controller has collected the expected annual prime costs for each briefcase, the machine hours, the setup hours, and the expected production.
Required:
1. CONCEPTUAL CONNECTION Do you think that the direct labor costs and direct materials costs are accurately traced to each briefcase? Explain.
2. Calculate the consumption ratios for each activity. Round to two decimal places.
3. Calculate the overhead cost per unit for each briefcase by using a plantwide rate based on direct labor costs. Round rates to the nearest cent. Comment on this approach to assigning overhead.
4. CONCEPTUAL CONNECTION Calculate the overhead cost per unit for each briefcase by using overhead rates based on machine hours and setup hours. Explain why these assignments are more accurate than using the direct labor costs.
Plata Company produces two products: a mostly handcrafted soft leather briefcase sold under the label Maletin Elegant and a leather briefcase produced largely through automation and sold under the label Maletin Fina. The two products use two overhead activities, with the following costs:

The controller has collected the expected annual prime costs for each briefcase, the machine hours, the setup hours, and the expected production.
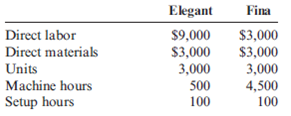
Required:
1. CONCEPTUAL CONNECTION Do you think that the direct labor costs and direct materials costs are accurately traced to each briefcase? Explain.
2. Calculate the consumption ratios for each activity. Round to two decimal places.
3. Calculate the overhead cost per unit for each briefcase by using a plantwide rate based on direct labor costs. Round rates to the nearest cent. Comment on this approach to assigning overhead.
4. CONCEPTUAL CONNECTION Calculate the overhead cost per unit for each briefcase by using overhead rates based on machine hours and setup hours. Explain why these assignments are more accurate than using the direct labor costs.
فتح الحزمة
افتح القفل للوصول البطاقات البالغ عددها 80 في هذه المجموعة.
فتح الحزمة
k this deck
10
Activity-Based Costing, Distorted Product Costs
Sharp Paper Inc. has three paper mills, one of which is located in Memphis, Tennessee. The Memphis mill produces 300 different types of coated and uncoated specialty printing papers. Management was convinced that the value of the large variety of products more than offset the extra costs of the increased complexity.
During 2015, the Memphis mill produced 120,000 tons of coated paper and 80,000 tons of uncoated paper. Of the 200,000 tons produced, 180,000 were sold. Sixty products account for 80% of the tons sold. Thus, 240 products are classified as low-volume products.
Lightweight lime hopsack in cartons (LLHC) is one of the low-volume products. LLHC is produced in rolls, converted into sheets of paper, and then sold in cartons. In 2015 the cost to produce and sell one ton of LLHC was as follows:
Overhead is applied by using a two-stage process. First, overhead is allocated to the paper and finishing machines by using the direct method of allocation with carefully selected cost drivers. Second, the overhead assigned to each machine is divided by the budgeted tons of output. These rates are then multiplied by the number of pounds required to produce one good ton.
In 2015, LLHC sold for $2,400 per ton, making it one of the most profitable products. A similar examination of some of the other low-volume products revealed that they also had very respectable profit margins. Unfortunately, the performance of the high volume products was less impressive, with many showing losses or very low profit margins. This situation led Ryan Chesser to call a meeting with his marketing vice president, Jennifer Woodruff, and his controller, Kaylin Penn.
Ryan: The above-average profitability of our low-volume specialty products and the poor profit performance of our high-volume products make me believe that we should switch our marketing emphasis to the low-volume line. Perhaps we should drop some of our high-volume products, particularly those showing a loss.
Jennifer: I'm not convinced that solution is the right one. I know our high-volume products are of high quality, and I'm convinced that we are as efficient in our production as other firms. I think that somehow our costs are not being assigned correctly. For example, the shipping and warehousing costs are assigned by dividing these costs by the total tons of paper sold. Yet …
Kaylin: Jennifer, I hate to disagree, but the $30-per-ton charge for shipping and warehousing seems reasonable. I know that our method to assign these costs is identical to a number of other paper companies.
Jennifer: Well, that may be true, but do these other companies have the variety of products that we have? Our low-volume products require special handling and processing, but when we assign shipping and warehousing costs, we average these special costs across our entire product line. Every ton produced in our mill passes through our mill shipping department and is either sent directly to the customer or to our distribution center and then eventually to customers. My records indicate quite clearly that virtually all of the high-volume products are sent directly to customers, whereas most of the low-volume products are sent to the distribution center. Now, all of the products passing through the mill shipping department should receive a share of the $2,000,000 annual shipping costs. I'm not convinced, however, that all products should receive a share of the receiving and shipping costs of the distribution center as currently practiced.
Ryan: Kaylin, is this true?Does our systemallocate our shipping and warehousing costs in this way?
Kaylin: Yes, I'm afraid it does. Jennifer may have a point. Perhaps we need to reevaluate our method to assign these costs to the product lines.
Ryan: Jennifer, do you have any suggestions concerning how the shipping and warehousing costs should be assigned?
Jennifer: It seems reasonable to make a distinction between products that spend time in the distribution center and those that do not. We should also distinguish between the receiving and shipping activities at the distribution center. All incoming shipments are packed on pallets and weigh one ton each (there are 14 cartons of paper per pallet). In 2015, the receiving department processed 56,000 tons of paper. Receiving employs 15 people at an annual cost of $600,000. Other receiving costs total about $500,000. I would recommend that these costs be assigned by using tons processed.
Shipping, however, is different. There are two activities associated with shipping: picking the order from inventory and loading the paper. We employ 30 people for picking and 10 for loading, at an annual cost of $1,200,000. Other shipping costs total $1,100,000. Picking and loading are more concerned with the number of shipping items than with tonnage. That is, a shipping item may consist of two or three cartons instead of pallets. Accordingly, the shipping costs of the distribution center should be assigned by using the number of items shipped. In 2015, for example, we handled 190,000 shipping items.
Ryan: These suggestions have merit. Kaylin, I would like to see what effect Jennifer's suggestions have on the per-unit assignment of shipping and warehousing for LLHC. If the effect is significant, then we will expand the analysis to include all products.
Kaylin: I'm willing to compute the effect, but I'd like to suggest one additional feature. Currently, we have a policy to carry about 25 tons of LLHC in inventory. Our current costing system totally ignores the cost of carrying this inventory. Since it costs us $1,665 to produce each ton of this product, we are tying up a lot of money in inventory-money that could be invested in other productive opportunities. In fact, the return lost is about 16% per year. This cost should also be assigned to the units sold.
Ryan: Kaylin, this also sounds good to me. Go ahead and include the carrying cost in your computation.
To help in the analysis, Kaylin gathered the following data for LLHC for 2015:
Required:
1. Identify the flaws associated with the current method of assigning shipping and warehousing costs to Sharp's products.
2. Compute the shipping and warehousing cost per ton of LLHC sold by using the new method suggested by Jennifer and Kaylin. Round rates and the cost per ton to two decimal places.
3. Using the new costs computed in Requirement 2, compute the profit per ton of LLHC. Compare this with the profit per ton computed by using the old method. Do you think that this same effect would be realized for other low-volume products? Explain.
4. Comment on Ryan's proposal to drop some high-volume products and place more emphasis on low-volume products. Discuss the role of the accounting system in supporting this type of decision making.
5. After receiving the analysis of LLHC, Ryan decided to expand the analysis to all products. He also had Kaylin reevaluate the way in which mill overhead was assigned to products. After the restructuring was completed, Ryan took the following actions: (a) the prices of most low-volume products were increased, (b) the prices of several high-volume products were decreased, and (c) some low-volume products were dropped. Explain why his strategy changed so dramatically.
Sharp Paper Inc. has three paper mills, one of which is located in Memphis, Tennessee. The Memphis mill produces 300 different types of coated and uncoated specialty printing papers. Management was convinced that the value of the large variety of products more than offset the extra costs of the increased complexity.
During 2015, the Memphis mill produced 120,000 tons of coated paper and 80,000 tons of uncoated paper. Of the 200,000 tons produced, 180,000 were sold. Sixty products account for 80% of the tons sold. Thus, 240 products are classified as low-volume products.
Lightweight lime hopsack in cartons (LLHC) is one of the low-volume products. LLHC is produced in rolls, converted into sheets of paper, and then sold in cartons. In 2015 the cost to produce and sell one ton of LLHC was as follows:
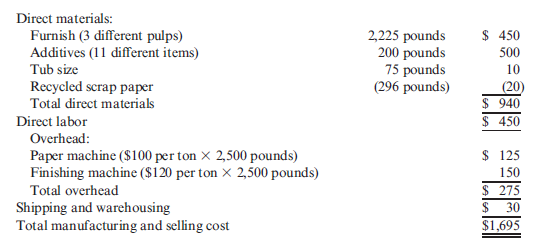
Overhead is applied by using a two-stage process. First, overhead is allocated to the paper and finishing machines by using the direct method of allocation with carefully selected cost drivers. Second, the overhead assigned to each machine is divided by the budgeted tons of output. These rates are then multiplied by the number of pounds required to produce one good ton.
In 2015, LLHC sold for $2,400 per ton, making it one of the most profitable products. A similar examination of some of the other low-volume products revealed that they also had very respectable profit margins. Unfortunately, the performance of the high volume products was less impressive, with many showing losses or very low profit margins. This situation led Ryan Chesser to call a meeting with his marketing vice president, Jennifer Woodruff, and his controller, Kaylin Penn.
Ryan: The above-average profitability of our low-volume specialty products and the poor profit performance of our high-volume products make me believe that we should switch our marketing emphasis to the low-volume line. Perhaps we should drop some of our high-volume products, particularly those showing a loss.
Jennifer: I'm not convinced that solution is the right one. I know our high-volume products are of high quality, and I'm convinced that we are as efficient in our production as other firms. I think that somehow our costs are not being assigned correctly. For example, the shipping and warehousing costs are assigned by dividing these costs by the total tons of paper sold. Yet …
Kaylin: Jennifer, I hate to disagree, but the $30-per-ton charge for shipping and warehousing seems reasonable. I know that our method to assign these costs is identical to a number of other paper companies.
Jennifer: Well, that may be true, but do these other companies have the variety of products that we have? Our low-volume products require special handling and processing, but when we assign shipping and warehousing costs, we average these special costs across our entire product line. Every ton produced in our mill passes through our mill shipping department and is either sent directly to the customer or to our distribution center and then eventually to customers. My records indicate quite clearly that virtually all of the high-volume products are sent directly to customers, whereas most of the low-volume products are sent to the distribution center. Now, all of the products passing through the mill shipping department should receive a share of the $2,000,000 annual shipping costs. I'm not convinced, however, that all products should receive a share of the receiving and shipping costs of the distribution center as currently practiced.
Ryan: Kaylin, is this true?Does our systemallocate our shipping and warehousing costs in this way?
Kaylin: Yes, I'm afraid it does. Jennifer may have a point. Perhaps we need to reevaluate our method to assign these costs to the product lines.
Ryan: Jennifer, do you have any suggestions concerning how the shipping and warehousing costs should be assigned?
Jennifer: It seems reasonable to make a distinction between products that spend time in the distribution center and those that do not. We should also distinguish between the receiving and shipping activities at the distribution center. All incoming shipments are packed on pallets and weigh one ton each (there are 14 cartons of paper per pallet). In 2015, the receiving department processed 56,000 tons of paper. Receiving employs 15 people at an annual cost of $600,000. Other receiving costs total about $500,000. I would recommend that these costs be assigned by using tons processed.
Shipping, however, is different. There are two activities associated with shipping: picking the order from inventory and loading the paper. We employ 30 people for picking and 10 for loading, at an annual cost of $1,200,000. Other shipping costs total $1,100,000. Picking and loading are more concerned with the number of shipping items than with tonnage. That is, a shipping item may consist of two or three cartons instead of pallets. Accordingly, the shipping costs of the distribution center should be assigned by using the number of items shipped. In 2015, for example, we handled 190,000 shipping items.
Ryan: These suggestions have merit. Kaylin, I would like to see what effect Jennifer's suggestions have on the per-unit assignment of shipping and warehousing for LLHC. If the effect is significant, then we will expand the analysis to include all products.
Kaylin: I'm willing to compute the effect, but I'd like to suggest one additional feature. Currently, we have a policy to carry about 25 tons of LLHC in inventory. Our current costing system totally ignores the cost of carrying this inventory. Since it costs us $1,665 to produce each ton of this product, we are tying up a lot of money in inventory-money that could be invested in other productive opportunities. In fact, the return lost is about 16% per year. This cost should also be assigned to the units sold.
Ryan: Kaylin, this also sounds good to me. Go ahead and include the carrying cost in your computation.
To help in the analysis, Kaylin gathered the following data for LLHC for 2015:
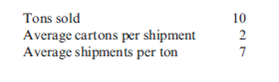
Required:
1. Identify the flaws associated with the current method of assigning shipping and warehousing costs to Sharp's products.
2. Compute the shipping and warehousing cost per ton of LLHC sold by using the new method suggested by Jennifer and Kaylin. Round rates and the cost per ton to two decimal places.
3. Using the new costs computed in Requirement 2, compute the profit per ton of LLHC. Compare this with the profit per ton computed by using the old method. Do you think that this same effect would be realized for other low-volume products? Explain.
4. Comment on Ryan's proposal to drop some high-volume products and place more emphasis on low-volume products. Discuss the role of the accounting system in supporting this type of decision making.
5. After receiving the analysis of LLHC, Ryan decided to expand the analysis to all products. He also had Kaylin reevaluate the way in which mill overhead was assigned to products. After the restructuring was completed, Ryan took the following actions: (a) the prices of most low-volume products were increased, (b) the prices of several high-volume products were decreased, and (c) some low-volume products were dropped. Explain why his strategy changed so dramatically.
فتح الحزمة
افتح القفل للوصول البطاقات البالغ عددها 80 في هذه المجموعة.
فتح الحزمة
k this deck
11
The receiving department employs one worker, who spends 25% of his time on the receiving activity and 75% of his time on inspecting products. His salary is $40,000. The amount of cost assigned to the receiving activity is
A) $34,000.
B) $40,000.
C) $10,000.
D) $30,000.
E) None of these.
A) $34,000.
B) $40,000.
C) $10,000.
D) $30,000.
E) None of these.
فتح الحزمة
افتح القفل للوصول البطاقات البالغ عددها 80 في هذه المجموعة.
فتح الحزمة
k this deck
12
The cost of inspecting incoming parts is most likely to be reduced by
A) activity sharing.
B) activity elimination.
C) activity reduction.
D) activity selection.
E) None of these.
A) activity sharing.
B) activity elimination.
C) activity reduction.
D) activity selection.
E) None of these.
فتح الحزمة
افتح القفل للوصول البطاقات البالغ عددها 80 في هذه المجموعة.
فتح الحزمة
k this deck
13
Activity-Based Customer Costing
Dormirbien Company produces mattresses for 20 retail outlets. Of the 20 retail outlets, 19 are small, separately owned furniture stores and one is a retail chain. The retail chain buys 60% of the mattresses produced. The 19 smaller customers purchase mattresses in approximately equal quantities, where the orders are about the same size. Data concerning Dormirbien's customer activity are as follows:
Currently, customer-driven costs are assigned to customers based on units sold, a unit-level driver.
Required:
Assign costs to customers by using an ABC approach. Round activity rates and activity costs to the nearest dollar.
Dormirbien Company produces mattresses for 20 retail outlets. Of the 20 retail outlets, 19 are small, separately owned furniture stores and one is a retail chain. The retail chain buys 60% of the mattresses produced. The 19 smaller customers purchase mattresses in approximately equal quantities, where the orders are about the same size. Data concerning Dormirbien's customer activity are as follows:
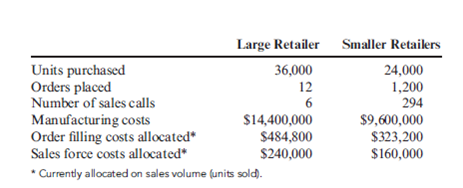
Currently, customer-driven costs are assigned to customers based on units sold, a unit-level driver.
Required:
Assign costs to customers by using an ABC approach. Round activity rates and activity costs to the nearest dollar.
فتح الحزمة
افتح القفل للوصول البطاقات البالغ عددها 80 في هذه المجموعة.
فتح الحزمة
k this deck
14
Product-Costing Accuracy, Consumption Ratios, Activity Rates, Activity Costing
Tristar Manufacturing produces two types of battery-operated toy soldiers: infantry and special forces. The soldiers are produced by using one continuous process. Four activities have been identified: machining, setups, receiving, and packing. Resource drivers have been used to assign costs to each activity. The overhead activities, their costs, and the other related data are as follows:
Required:
1. Calculate the total overhead assigned to each product by using only machine hours to calculate a plantwide rate.
2. Calculate consumption ratios for each activity. (Round to two decimal places.)
3. Calculate a rate for each activity by using the associated driver. (Round to two decimal places.)
4. Assign the overhead costs to each product by using the activity rates computed in Requirement 3.
5. CONCEPTUAL CONNECTION Comment on the difference between the assignment in Requirement 1 and the activity-based assignment.
Tristar Manufacturing produces two types of battery-operated toy soldiers: infantry and special forces. The soldiers are produced by using one continuous process. Four activities have been identified: machining, setups, receiving, and packing. Resource drivers have been used to assign costs to each activity. The overhead activities, their costs, and the other related data are as follows:

Required:
1. Calculate the total overhead assigned to each product by using only machine hours to calculate a plantwide rate.
2. Calculate consumption ratios for each activity. (Round to two decimal places.)
3. Calculate a rate for each activity by using the associated driver. (Round to two decimal places.)
4. Assign the overhead costs to each product by using the activity rates computed in Requirement 3.
5. CONCEPTUAL CONNECTION Comment on the difference between the assignment in Requirement 1 and the activity-based assignment.
فتح الحزمة
افتح القفل للوصول البطاقات البالغ عددها 80 في هذه المجموعة.
فتح الحزمة
k this deck
15
Activity-Based Product Costing and Ethical Behavior
Consider the following conversation between Leonard Bryner, president and manager of a firm engaged in job manufacturing, and Chuck Davis, certified management accountant, the firm's controller.
Leonard: Chuck, as you know, our firm has been losing market share over the past 3 years. We have been losing more and more bids, and I don't understand why. At first, I thought that other firms were undercutting simply to gain business, but after examining some of the public financial reports, I believe that they are making a reasonable rate of return. I am beginning to believe that our costs and costing methods are at fault.
Chuck: I can't agree with that. We have good control over our costs. Like most firms in our industry, we use a normal job-costing system. I really don't see any significant waste in the plant.
Leonard: After talking with some other managers at a recent industrial convention, I'm not so sure that waste by itself is the issue. They talked about activity-based management, activitybased costing, and continuous improvement. They mentioned the use of something called ''activity drivers'' to assign overhead. They claimed that these new procedures can help to produce more efficiency in manufacturing, better control of overhead, and more accurate product costing. A big deal was made of eliminating activities that added no value. Maybe our bids are too high because these other firms have found ways to decrease their overhead costs and to increase the accuracy of their product costing.
Chuck: I doubt it. For one thing, I don't see how we can increase product costing accuracy. So many of our costs are indirect costs. Furthermore, everyone uses some measure of production activity to assign overhead costs. I imagine that what they are calling ''activity drivers'' is just some new buzzword for measures of production volume. Fads in costing come and go. I wouldn't worry about it. I'll bet that our problems with decreasing sales are temporary. You might recall that we experienced a similar problem about 12 years ago-it was 2 years before it straightened out.
Required:
1. Do you agree or disagree with Chuck Davis and the advice that he gave Leonard Bryner? Explain.
2. Was there anything wrong or unethical in the behavior that Chuck Davis displayed? Explain your reasoning.
3. Do you think that Chuck was well informed-that he was aware of the accounting implications of ABC and that he knew what was meant by cost drivers? Should he have been well informed? Review (in Chapter 1) the first category of the Statement of Ethical Professional Practice for management accountants. Do any of these standards apply in Chuck's case?
Consider the following conversation between Leonard Bryner, president and manager of a firm engaged in job manufacturing, and Chuck Davis, certified management accountant, the firm's controller.
Leonard: Chuck, as you know, our firm has been losing market share over the past 3 years. We have been losing more and more bids, and I don't understand why. At first, I thought that other firms were undercutting simply to gain business, but after examining some of the public financial reports, I believe that they are making a reasonable rate of return. I am beginning to believe that our costs and costing methods are at fault.
Chuck: I can't agree with that. We have good control over our costs. Like most firms in our industry, we use a normal job-costing system. I really don't see any significant waste in the plant.
Leonard: After talking with some other managers at a recent industrial convention, I'm not so sure that waste by itself is the issue. They talked about activity-based management, activitybased costing, and continuous improvement. They mentioned the use of something called ''activity drivers'' to assign overhead. They claimed that these new procedures can help to produce more efficiency in manufacturing, better control of overhead, and more accurate product costing. A big deal was made of eliminating activities that added no value. Maybe our bids are too high because these other firms have found ways to decrease their overhead costs and to increase the accuracy of their product costing.
Chuck: I doubt it. For one thing, I don't see how we can increase product costing accuracy. So many of our costs are indirect costs. Furthermore, everyone uses some measure of production activity to assign overhead costs. I imagine that what they are calling ''activity drivers'' is just some new buzzword for measures of production volume. Fads in costing come and go. I wouldn't worry about it. I'll bet that our problems with decreasing sales are temporary. You might recall that we experienced a similar problem about 12 years ago-it was 2 years before it straightened out.
Required:
1. Do you agree or disagree with Chuck Davis and the advice that he gave Leonard Bryner? Explain.
2. Was there anything wrong or unethical in the behavior that Chuck Davis displayed? Explain your reasoning.
3. Do you think that Chuck was well informed-that he was aware of the accounting implications of ABC and that he knew what was meant by cost drivers? Should he have been well informed? Review (in Chapter 1) the first category of the Statement of Ethical Professional Practice for management accountants. Do any of these standards apply in Chuck's case?
فتح الحزمة
افتح القفل للوصول البطاقات البالغ عددها 80 في هذه المجموعة.
فتح الحزمة
k this deck
16
Describe the two-stage process associated with plantwide overhead rates.
فتح الحزمة
افتح القفل للوصول البطاقات البالغ عددها 80 في هذه المجموعة.
فتح الحزمة
k this deck
17
Describe the value of activity-based customer costing.
فتح الحزمة
افتح القفل للوصول البطاقات البالغ عددها 80 في هذه المجموعة.
فتح الحزمة
k this deck
18
Thom Company produces 60 units in 10 hours. The cycle time for Thom
a. is 6 units per hour.
b. is 10 hours per unit.
c. is 10 minutes per unit.
d. is 6 minutes per unit.
e. cannot be calculated.
a. is 6 units per hour.
b. is 10 hours per unit.
c. is 10 minutes per unit.
d. is 6 minutes per unit.
e. cannot be calculated.
فتح الحزمة
افتح القفل للوصول البطاقات البالغ عددها 80 في هذه المجموعة.
فتح الحزمة
k this deck
19
Activity-Based Supplier Costing
LissenPhones uses Alpha Electronics and La Paz Company to buy two electronic components used in the manufacture of its cell phones: Component 125X and Component 30Y. Consider two activities: testing and reordering components. After the two components are inserted, testing is done to ensure that the two components in the phones are working properly. Reordering occurs because one or both of the components have failed the test and it is necessary to replenish component inventories. Activity cost information and other data needed for supplier costing are as follows:
I. Activity Costs Caused by Suppliers (testing failures and reordering as a result)
II. Supplier Data
Required:
Determine the cost of each supplier by using ABC. Round unit costs to two decimal places.
LissenPhones uses Alpha Electronics and La Paz Company to buy two electronic components used in the manufacture of its cell phones: Component 125X and Component 30Y. Consider two activities: testing and reordering components. After the two components are inserted, testing is done to ensure that the two components in the phones are working properly. Reordering occurs because one or both of the components have failed the test and it is necessary to replenish component inventories. Activity cost information and other data needed for supplier costing are as follows:
I. Activity Costs Caused by Suppliers (testing failures and reordering as a result)
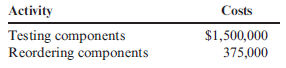
II. Supplier Data
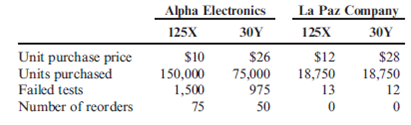
Required:
Determine the cost of each supplier by using ABC. Round unit costs to two decimal places.
فتح الحزمة
افتح القفل للوصول البطاقات البالغ عددها 80 في هذه المجموعة.
فتح الحزمة
k this deck
20
Formation of an Activity Dictionary
A hospital is in the process of implementing an ABC system. A pilot study is being done to assess the effects of the costing changes on specific products. Of particular interest is the cost of caring for patients who receive in-patient recovery treatment for illness, surgery (noncardiac), and injury. These patients are housed on the third and fourth floors of the hospital (the floors are dedicated to patient care and have only nursing stations and patient rooms). A partial transcript of an interview with the hospital's nursing supervisor is as follows:
1. How many nurses are in the hospital?
2. Of these 100 nurses, how many are assigned to the third and fourth floors?
3. What do these nurses do (please describe)?
4. And what do you do?
5. What other lodging and care activities are done for the third and fourth floors by persons other than the nurses?
6. Do patients use any equipment?
7. Who or what uses the activity output?
Required:
Prepare an activity dictionary with three categories: activity name, activity description, and activity driver.
A hospital is in the process of implementing an ABC system. A pilot study is being done to assess the effects of the costing changes on specific products. Of particular interest is the cost of caring for patients who receive in-patient recovery treatment for illness, surgery (noncardiac), and injury. These patients are housed on the third and fourth floors of the hospital (the floors are dedicated to patient care and have only nursing stations and patient rooms). A partial transcript of an interview with the hospital's nursing supervisor is as follows:
1. How many nurses are in the hospital?
2. Of these 100 nurses, how many are assigned to the third and fourth floors?
3. What do these nurses do (please describe)?
4. And what do you do?
5. What other lodging and care activities are done for the third and fourth floors by persons other than the nurses?
6. Do patients use any equipment?
7. Who or what uses the activity output?
Required:
Prepare an activity dictionary with three categories: activity name, activity description, and activity driver.
فتح الحزمة
افتح القفل للوصول البطاقات البالغ عددها 80 في هذه المجموعة.
فتح الحزمة
k this deck
21
A batch-level driver is consumed by a product each and every time that
A) a batch of products is produced.
B) a unit is produced.
C) a purchase order is issued.
D) a customer complains.
E) None of these.
A) a batch of products is produced.
B) a unit is produced.
C) a purchase order is issued.
D) a customer complains.
E) None of these.
فتح الحزمة
افتح القفل للوصول البطاقات البالغ عددها 80 في هذه المجموعة.
فتح الحزمة
k this deck
22
Assume that the moving activity has an expected cost of $80,000. Expected direct labor hours are 20,000, and expected number of moves is 40,000. The best activity rate for moving is
a. $4 per move.
b. $1.33 per hour-move.
c. $4 per hour.
d. $2 per move.
e. None of these.
a. $4 per move.
b. $1.33 per hour-move.
c. $4 per hour.
d. $2 per move.
e. None of these.
فتح الحزمة
افتح القفل للوصول البطاقات البالغ عددها 80 في هذه المجموعة.
فتح الحزمة
k this deck
23
Thom Company produces 60 units in 10 hours. The velocity for Thom
a. is 6 units per hour.
b. is 10 hours per unit.
c. is 10 minutes per unit.
d. 6 minutes per unit.
e. cannot be calculated.
a. is 6 units per hour.
b. is 10 hours per unit.
c. is 10 minutes per unit.
d. 6 minutes per unit.
e. cannot be calculated.
فتح الحزمة
افتح القفل للوصول البطاقات البالغ عددها 80 في هذه المجموعة.
فتح الحزمة
k this deck
24
Nonvalue-Added Costs
Boothe Inc. has the following two activities: (1) Retesting reworked products, cost: $480,000. The retesting cost of the most efficient competitor is $150,000. (2) Welding subassemblies, cost: $900,000 (45,000 welding hours). A benchmarking study reveals that the most efficient level for Boothe would use 36,000 welding hours and entail a cost of $720,000.
Required:
Determine the nonvalue-added cost of each activity.
Boothe Inc. has the following two activities: (1) Retesting reworked products, cost: $480,000. The retesting cost of the most efficient competitor is $150,000. (2) Welding subassemblies, cost: $900,000 (45,000 welding hours). A benchmarking study reveals that the most efficient level for Boothe would use 36,000 welding hours and entail a cost of $720,000.
Required:
Determine the nonvalue-added cost of each activity.
فتح الحزمة
افتح القفل للوصول البطاقات البالغ عددها 80 في هذه المجموعة.
فتح الحزمة
k this deck
25
Activity Rates and Activity-Based Product Costing
Hammer Company produces a variety of electronic equipment. One of its plants produces two laser printers: the deluxe and the regular. At the beginning of the year, the following data were prepared for this plant:
In addition, the following information was provided so that overhead costs could be assigned to each product:
Required:
1. Calculate the overhead rates for each activity. (Round to two decimal places.)
2. Calculate the per-unit product cost for each product. (Round to the nearest dollar.)
Hammer Company produces a variety of electronic equipment. One of its plants produces two laser printers: the deluxe and the regular. At the beginning of the year, the following data were prepared for this plant:
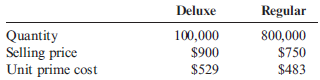
In addition, the following information was provided so that overhead costs could be assigned to each product:

Required:
1. Calculate the overhead rates for each activity. (Round to two decimal places.)
2. Calculate the per-unit product cost for each product. (Round to the nearest dollar.)
فتح الحزمة
افتح القفل للوصول البطاقات البالغ عددها 80 في هذه المجموعة.
فتح الحزمة
k this deck
26
Describe the two-stage process for departmental overhead rates.
فتح الحزمة
افتح القفل للوصول البطاقات البالغ عددها 80 في هذه المجموعة.
فتح الحزمة
k this deck
27
Explain how ABC can help a firm identify its true low-cost suppliers.
فتح الحزمة
افتح القفل للوصول البطاقات البالغ عددها 80 في هذه المجموعة.
فتح الحزمة
k this deck
28
Striving to produce the same activity output with lower costs for the input used is concerned with which of the following dimensions of activity performance?
A) Quality
B) Time
C) Activity sharing
D) Effectiveness
E) Efficiency
A) Quality
B) Time
C) Activity sharing
D) Effectiveness
E) Efficiency
فتح الحزمة
افتح القفل للوصول البطاقات البالغ عددها 80 في هذه المجموعة.
فتح الحزمة
k this deck
29
Velocity and Cycle Time
Karsen Company takes 7,200 hours to produce 28,800 units of a product.
Required:
What is the velocity? Cycle time?
Karsen Company takes 7,200 hours to produce 28,800 units of a product.
Required:
What is the velocity? Cycle time?
فتح الحزمة
افتح القفل للوصول البطاقات البالغ عددها 80 في هذه المجموعة.
فتح الحزمة
k this deck
30
Value- and Nonvalue-Added Costs
Waterfun Technology produces engines for recreational boats. Because of competitive pressures, the company was making an effort to reduce costs. As part of this effort, management implemented an activity-based management system and began focusing its attention on processes and activities. Receiving was among the processes (activities) that were carefully studied. The study revealed that the number of receiving orders was a good driver for receiving costs. During the last year, the company incurred fixed receiving costs of $630,000 (salaries of 10 employees). These fixed costs provide a capacity of processing 72,000 receiving orders (7,200 per employee at practical capacity). Management decided that the efficient level for receiving should use 36,000 receiving orders.
Required:
1. CONCEPTUAL CONNECTION Explain why receiving would be viewed as a value-added activity. List all possible reasons. Also, list some possible reasons that explain why the demand for receiving is more than the efficient level of 36,000 orders.
2. Break the cost of receiving into its value-added and nonvalue-added components.
Waterfun Technology produces engines for recreational boats. Because of competitive pressures, the company was making an effort to reduce costs. As part of this effort, management implemented an activity-based management system and began focusing its attention on processes and activities. Receiving was among the processes (activities) that were carefully studied. The study revealed that the number of receiving orders was a good driver for receiving costs. During the last year, the company incurred fixed receiving costs of $630,000 (salaries of 10 employees). These fixed costs provide a capacity of processing 72,000 receiving orders (7,200 per employee at practical capacity). Management decided that the efficient level for receiving should use 36,000 receiving orders.
Required:
1. CONCEPTUAL CONNECTION Explain why receiving would be viewed as a value-added activity. List all possible reasons. Also, list some possible reasons that explain why the demand for receiving is more than the efficient level of 36,000 orders.
2. Break the cost of receiving into its value-added and nonvalue-added components.
فتح الحزمة
افتح القفل للوصول البطاقات البالغ عددها 80 في هذه المجموعة.
فتح الحزمة
k this deck
31
Which of the following is a nonunit-level driver?
A) Direct labor hours
B) Machine hours
C) Direct materials
D) Setup hours
E) Assembly hours
A) Direct labor hours
B) Machine hours
C) Direct materials
D) Setup hours
E) Assembly hours
فتح الحزمة
افتح القفل للوصول البطاقات البالغ عددها 80 في هذه المجموعة.
فتح الحزمة
k this deck
32
Which of the following is a true statement about activity-based customer costing?
A) Customer diversity requires multiple drivers to trace costs accurately to customers.
B) Customers consume customer-driven activities in the same proportions.
C) It seldom produces changes in the company's customer mix.
D) It never improves profitability.
E) None of the above are true.
A) Customer diversity requires multiple drivers to trace costs accurately to customers.
B) Customers consume customer-driven activities in the same proportions.
C) It seldom produces changes in the company's customer mix.
D) It never improves profitability.
E) None of the above are true.
فتح الحزمة
افتح القفل للوصول البطاقات البالغ عددها 80 في هذه المجموعة.
فتح الحزمة
k this deck
33
Which of the following is a quality prevention cost?
A) Quality planning
B) Supplier evaluation and selection
C) Quality audits
D) Field trials
E) All of these.
A) Quality planning
B) Supplier evaluation and selection
C) Quality audits
D) Field trials
E) All of these.
فتح الحزمة
افتح القفل للوصول البطاقات البالغ عددها 80 في هذه المجموعة.
فتح الحزمة
k this deck
34
Consumption Ratios; Activity Rates
Bienestar Company produces two types of get-well cards: scented and regular. Drivers for the four activities are as follows:
The following activity data have been collected:
Required:
1. Calculate the consumption ratios for the four drivers (round to two decimal places).
2. CONCEPTUAL CONNECTION Is there evidence of product diversity? Explain the significance of product diversity for decision making if the company chooses to use machine hours to assign all overhead.
3. Calculate the activity rates that would be used to assign costs to each product (round to two decimal places).
4. Suppose that the activity rate for inspecting products is $20 per inspection hour. How many hours of inspection are expected for the coming year?
Bienestar Company produces two types of get-well cards: scented and regular. Drivers for the four activities are as follows:
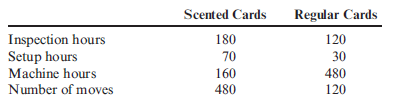
The following activity data have been collected:
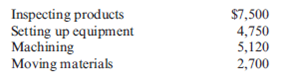
Required:
1. Calculate the consumption ratios for the four drivers (round to two decimal places).
2. CONCEPTUAL CONNECTION Is there evidence of product diversity? Explain the significance of product diversity for decision making if the company chooses to use machine hours to assign all overhead.
3. Calculate the activity rates that would be used to assign costs to each product (round to two decimal places).
4. Suppose that the activity rate for inspecting products is $20 per inspection hour. How many hours of inspection are expected for the coming year?
فتح الحزمة
افتح القفل للوصول البطاقات البالغ عددها 80 في هذه المجموعة.
فتح الحزمة
k this deck
35
Functional-Based versus Activity-Based Costing
For years, Tamarindo Company produced only one product: backpacks. Recently, Tamarindo added a line of duffel bags. With this addition, the company began assigning overhead costs by using departmental rates. (Prior to this, the company used a predetermined plantwide rate based on units produced.) Surprisingly, after the addition of the duffel-bag line and the switch to departmental rates, the costs to produce the backpacks increased, and their profitability dropped.
Josie, the marketing manager, and Steve, the production manager, both complained about the increase in the production cost of backpacks. Josie was concerned because the increase in unit costs led to pressure to increase the unit price of backpacks. She was resisting this pressure because she was certain that the increase would harm the company's market share. Steve was receiving pressure to cut costs also, yet he was convinced that nothing different was being done in the way the backpacks were produced. After some discussion, the two managers decided that the problem had to be connected to the addition of the duffel-bag line.
Upon investigation, they were informed that the only real change in product costing procedures was in the way overhead costs are assigned. A two-stage procedure was now in use. First, overhead costs are assigned to the two producing departments, Patterns and Finishing. Second, the costs accumulated in the producing departments are assigned to the two products by using direct labor hours as a driver (the rate in each department is based on direct labor hours). The managers were assured that great care was taken to associate overhead costs with individual products. So that they could construct their own example of overhead cost assignment, the controller provided them with the information necessary to show how accounting costs are assigned to products:
The controller remarked that the cost of operating the accounting department had doubled with the addition of the new product line. The increase came because of the need to process additional transactions, which had also doubled in number.
During the first year of producing duffel bags, the company produced and sold 100,000 backpacks and 25,000 duffel bags. The 100,000 backpacks matched the prior year's output for that product.
Required:
( Note: Round rates and unit cost to the nearest cent.)
1. CONCEPTUAL CONNECTION Compute the amount of accounting cost assigned to a backpack before the duffel-bag line was added by using a plantwide rate approach based on units produced. Is this assignment accurate? Explain.
2. Suppose that the company decided to assign the accounting costs directly to the product lines by using the number of transactions as the activity driver. What is the accounting cost per unit of backpacks? Per unit of duffel bags?
3. Compute the amount of accounting cost assigned to each backpack and duffel bag by using departmental rates based on direct labor hours.
4. CONCEPTUAL CONNECTION Which way of assigning overhead does the best job-the functional-based approach by using departmental rates or the activity-based approach by using transactions processed for each product? Explain. Discuss the value of ABC before the duffel-bag line was added.
For years, Tamarindo Company produced only one product: backpacks. Recently, Tamarindo added a line of duffel bags. With this addition, the company began assigning overhead costs by using departmental rates. (Prior to this, the company used a predetermined plantwide rate based on units produced.) Surprisingly, after the addition of the duffel-bag line and the switch to departmental rates, the costs to produce the backpacks increased, and their profitability dropped.
Josie, the marketing manager, and Steve, the production manager, both complained about the increase in the production cost of backpacks. Josie was concerned because the increase in unit costs led to pressure to increase the unit price of backpacks. She was resisting this pressure because she was certain that the increase would harm the company's market share. Steve was receiving pressure to cut costs also, yet he was convinced that nothing different was being done in the way the backpacks were produced. After some discussion, the two managers decided that the problem had to be connected to the addition of the duffel-bag line.
Upon investigation, they were informed that the only real change in product costing procedures was in the way overhead costs are assigned. A two-stage procedure was now in use. First, overhead costs are assigned to the two producing departments, Patterns and Finishing. Second, the costs accumulated in the producing departments are assigned to the two products by using direct labor hours as a driver (the rate in each department is based on direct labor hours). The managers were assured that great care was taken to associate overhead costs with individual products. So that they could construct their own example of overhead cost assignment, the controller provided them with the information necessary to show how accounting costs are assigned to products:
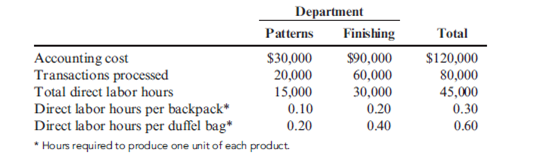
The controller remarked that the cost of operating the accounting department had doubled with the addition of the new product line. The increase came because of the need to process additional transactions, which had also doubled in number.
During the first year of producing duffel bags, the company produced and sold 100,000 backpacks and 25,000 duffel bags. The 100,000 backpacks matched the prior year's output for that product.
Required:
( Note: Round rates and unit cost to the nearest cent.)
1. CONCEPTUAL CONNECTION Compute the amount of accounting cost assigned to a backpack before the duffel-bag line was added by using a plantwide rate approach based on units produced. Is this assignment accurate? Explain.
2. Suppose that the company decided to assign the accounting costs directly to the product lines by using the number of transactions as the activity driver. What is the accounting cost per unit of backpacks? Per unit of duffel bags?
3. Compute the amount of accounting cost assigned to each backpack and duffel bag by using departmental rates based on direct labor hours.
4. CONCEPTUAL CONNECTION Which way of assigning overhead does the best job-the functional-based approach by using departmental rates or the activity-based approach by using transactions processed for each product? Explain. Discuss the value of ABC before the duffel-bag line was added.
فتح الحزمة
افتح القفل للوصول البطاقات البالغ عددها 80 في هذه المجموعة.
فتح الحزمة
k this deck
36
What are nonunit-level overhead activities? Nonunit-based cost drivers? Give some examples.
فتح الحزمة
افتح القفل للوصول البطاقات البالغ عددها 80 في هذه المجموعة.
فتح الحزمة
k this deck
37
What is driver analysis? What role does it play in process-value analysis?
فتح الحزمة
افتح القفل للوصول البطاقات البالغ عددها 80 في هذه المجموعة.
فتح الحزمة
k this deck
38
Which of the following is an appraisal cost (quality)?
a. Manager of an inspection team
b. Quality reporting
c. Design reviews
d. Warranties
e. Retesting
a. Manager of an inspection team
b. Quality reporting
c. Design reviews
d. Warranties
e. Retesting
فتح الحزمة
افتح القفل للوصول البطاقات البالغ عددها 80 في هذه المجموعة.
فتح الحزمة
k this deck
39
Activity Rates
Patten Company uses activity-based costing (ABC). Patten manufactures toy cars using two activities: plastic injection molding and decal application. Patten's 2015 total budgeted overhead costs for these two activities are $675,000 (80% for injection molding and 20% for decal application). Molding overhead costs are driven by the number of pounds of plastic that are molded together. Decal application overhead costs are driven by the number of decals applied to toys. The budgeted activity data for 2015 are as follows:
Required:
1. Calculate the activity rate for the plastic injection molding activity (round to two decimal places).
2. Calculate the activity rate for the decal application activity (round to two decimal places).
Patten Company uses activity-based costing (ABC). Patten manufactures toy cars using two activities: plastic injection molding and decal application. Patten's 2015 total budgeted overhead costs for these two activities are $675,000 (80% for injection molding and 20% for decal application). Molding overhead costs are driven by the number of pounds of plastic that are molded together. Decal application overhead costs are driven by the number of decals applied to toys. The budgeted activity data for 2015 are as follows:

Required:
1. Calculate the activity rate for the plastic injection molding activity (round to two decimal places).
2. Calculate the activity rate for the decal application activity (round to two decimal places).
فتح الحزمة
افتح القفل للوصول البطاقات البالغ عددها 80 في هذه المجموعة.
فتح الحزمة
k this deck
40
Plantwide versus Departmental Rates, Product-Costing Accuracy: Activity-Based Costing
Ramsey Company produces speakers (Model A and Model B). Both products pass through two producing departments. Model A's production is much more labor-intensive than that of Model B. Model B is also the more popular of the two speakers. The following data have been gathered for the two products:
Required:
1. Compute the overhead cost per unit for each product by using a plantwide rate based on direct labor hours. ( Note : Round to two decimal places.)
2. Compute the overhead cost per unit for each product by using ABC. ( Note: Round rates and unit overhead cost to two decimal places.)
3. Suppose that Ramsey decides to use departmental overhead rates. There are two departments: Department 1 (machine intensive) with a rate of $3.50 per machine hour and Department 2 (labor intensive) with a rate of $0.90 per direct labor hour. The consumption of these two drivers is as follows:
Compute the overhead cost per unit for each product by using departmental rates. ( Note: Round to two decimal places.)
4. CONCEPTUAL CONNECTION Using the activity-based product costs as the standard, comment on the ability of departmental rates to improve the accuracy of product costing. Did the departmental rates do better than the plantwide rate?
Ramsey Company produces speakers (Model A and Model B). Both products pass through two producing departments. Model A's production is much more labor-intensive than that of Model B. Model B is also the more popular of the two speakers. The following data have been gathered for the two products:
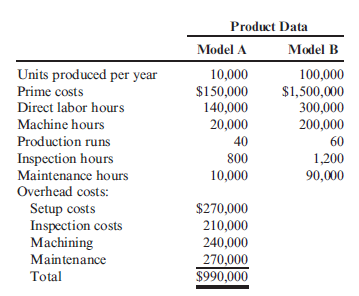
Required:
1. Compute the overhead cost per unit for each product by using a plantwide rate based on direct labor hours. ( Note : Round to two decimal places.)
2. Compute the overhead cost per unit for each product by using ABC. ( Note: Round rates and unit overhead cost to two decimal places.)
3. Suppose that Ramsey decides to use departmental overhead rates. There are two departments: Department 1 (machine intensive) with a rate of $3.50 per machine hour and Department 2 (labor intensive) with a rate of $0.90 per direct labor hour. The consumption of these two drivers is as follows:
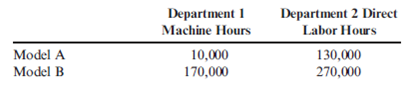
Compute the overhead cost per unit for each product by using departmental rates. ( Note: Round to two decimal places.)
4. CONCEPTUAL CONNECTION Using the activity-based product costs as the standard, comment on the ability of departmental rates to improve the accuracy of product costing. Did the departmental rates do better than the plantwide rate?
فتح الحزمة
افتح القفل للوصول البطاقات البالغ عددها 80 في هذه المجموعة.
فتح الحزمة
k this deck
41
Consider the information given on two products and their activity usage:
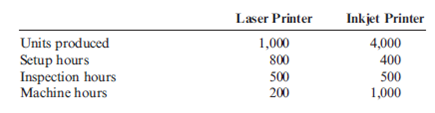
Refer to the information above. The consumption ratios for the inspection activity for each product are
A) 0.167; 0.833.
B) 0.333; 0.667.
C) 0.500; 0.500.
D) 0.667; 0.333.
E) None of these.
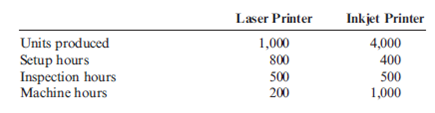
Refer to the information above. The consumption ratios for the inspection activity for each product are
A) 0.167; 0.833.
B) 0.333; 0.667.
C) 0.500; 0.500.
D) 0.667; 0.333.
E) None of these.
فتح الحزمة
افتح القفل للوصول البطاقات البالغ عددها 80 في هذه المجموعة.
فتح الحزمة
k this deck
42
Which of the following is a true statement about activity-based supplier costing?
a. The cost of a supplier is the purchase price of the components or materials acquired.
b. It encourages managers to increase the number of suppliers.
c. It encourages managers to evaluate suppliers based on purchase cost.
d. Suppliers can affect many internal activities of a firm and significantly increase the cost of purchasing.
e. All of the above are true.
a. The cost of a supplier is the purchase price of the components or materials acquired.
b. It encourages managers to increase the number of suppliers.
c. It encourages managers to evaluate suppliers based on purchase cost.
d. Suppliers can affect many internal activities of a firm and significantly increase the cost of purchasing.
e. All of the above are true.
فتح الحزمة
افتح القفل للوصول البطاقات البالغ عددها 80 في هذه المجموعة.
فتح الحزمة
k this deck
43
Which of the following is an internal failure cost (quality)?
a. Supplier evaluation and selection
b. Packaging inspection
c. Retesting
d. Product liability
e. Complaint adjustment
a. Supplier evaluation and selection
b. Packaging inspection
c. Retesting
d. Product liability
e. Complaint adjustment
فتح الحزمة
افتح القفل للوصول البطاقات البالغ عددها 80 في هذه المجموعة.
فتح الحزمة
k this deck
44
Comparing ABC and Plantwide Overhead Cost Assignments
The Sabroso Chocolate Company uses activity-based costing (ABC). The controller identified two activities and their budgeted costs:
Setting up equipment is based on setup hours, and other overhead is based on oven hours.
Oscuro produces two products, Fudge and Cookies. Information on each product is as follows:
Required:
( Note: Round answers to two decimal places.)
1. Calculate the activity rate for (a) setting up equipment and (b) other overhead.
2. How much total overhead is assigned to Fudge using ABC?
3. What is the unit overhead assigned to Fudge using ABC?
4. Now, ignoring the ABC results, calculate the plantwide overhead rate, based on oven hours.
5. How much total overhead is assigned to Fudge using the plantwide overhead rate?
6. CONCEPTUAL CONNECTION Explain why the total overhead assigned to Fudge is different under the ABC system (i.e., using the activity rates) than under the nonABC system (i.e., using the plantwide rate).
The Sabroso Chocolate Company uses activity-based costing (ABC). The controller identified two activities and their budgeted costs:

Setting up equipment is based on setup hours, and other overhead is based on oven hours.
Oscuro produces two products, Fudge and Cookies. Information on each product is as follows:

Required:
( Note: Round answers to two decimal places.)
1. Calculate the activity rate for (a) setting up equipment and (b) other overhead.
2. How much total overhead is assigned to Fudge using ABC?
3. What is the unit overhead assigned to Fudge using ABC?
4. Now, ignoring the ABC results, calculate the plantwide overhead rate, based on oven hours.
5. How much total overhead is assigned to Fudge using the plantwide overhead rate?
6. CONCEPTUAL CONNECTION Explain why the total overhead assigned to Fudge is different under the ABC system (i.e., using the activity rates) than under the nonABC system (i.e., using the plantwide rate).
فتح الحزمة
افتح القفل للوصول البطاقات البالغ عددها 80 في هذه المجموعة.
فتح الحزمة
k this deck
45
Production-Based Costing versus Activity-Based Costing, Assigning Costs to Activities, Resource Drivers
Willow Company produces lawn mowers. One of its plants produces two versions of mowers: a basic model and a deluxe model. The deluxe model has a sturdier frame, a higher horsepower engine, a wider blade, and mulching capability. At the beginning of the year, the following data were prepared for this plant:
Additionally, the following overhead activity costs are reported:
Facility-level costs are allocated in proportion to machine hours (provides a measure of time the facility is used by each product). Receiving and materials handling use three inputs: two forklifts, gasoline to operate the forklift, and three operators. The three operators are paid a salary of $40,000 each. The operators spend 25% of their time on the receiving activity and 75% on moving goods (materials handling). Gasoline costs $3 per move. Depreciation amounts to $8,000 per forklift per year.
Required:
( Note: Round answers to two decimal places.)
1. Calculate the cost of the materials handling activity. Label the cost assignments as driver tracing or direct tracing. Identify the resource drivers.
2. Calculate the cost per unit for each product by using direct labor hours to assign all overhead costs.
3. Calculate activity rates, and assign costs to each product. Calculate a unit cost for each product, and compare these costs with those calculated in Requirement 2.
4. Calculate consumption ratios for each activity.
5. CONCEPTUAL CONNECTION Explain how the consumption ratios calculated in Requirement 4 can be used to reduce the number of rates. Calculate the rates that would apply under this approach.
Willow Company produces lawn mowers. One of its plants produces two versions of mowers: a basic model and a deluxe model. The deluxe model has a sturdier frame, a higher horsepower engine, a wider blade, and mulching capability. At the beginning of the year, the following data were prepared for this plant:
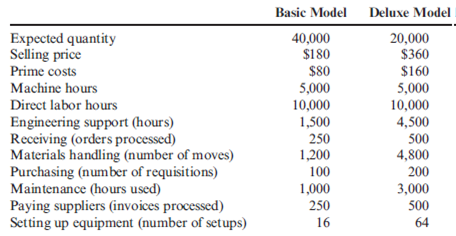
Additionally, the following overhead activity costs are reported:
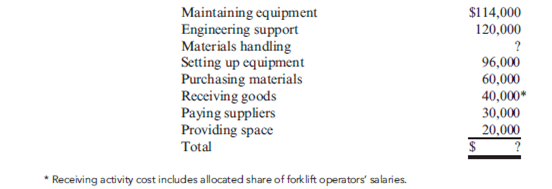
Facility-level costs are allocated in proportion to machine hours (provides a measure of time the facility is used by each product). Receiving and materials handling use three inputs: two forklifts, gasoline to operate the forklift, and three operators. The three operators are paid a salary of $40,000 each. The operators spend 25% of their time on the receiving activity and 75% on moving goods (materials handling). Gasoline costs $3 per move. Depreciation amounts to $8,000 per forklift per year.
Required:
( Note: Round answers to two decimal places.)
1. Calculate the cost of the materials handling activity. Label the cost assignments as driver tracing or direct tracing. Identify the resource drivers.
2. Calculate the cost per unit for each product by using direct labor hours to assign all overhead costs.
3. Calculate activity rates, and assign costs to each product. Calculate a unit cost for each product, and compare these costs with those calculated in Requirement 2.
4. Calculate consumption ratios for each activity.
5. CONCEPTUAL CONNECTION Explain how the consumption ratios calculated in Requirement 4 can be used to reduce the number of rates. Calculate the rates that would apply under this approach.
فتح الحزمة
افتح القفل للوصول البطاقات البالغ عددها 80 في هذه المجموعة.
فتح الحزمة
k this deck
46
What is meant by ''product diversity''?
فتح الحزمة
افتح القفل للوصول البطاقات البالغ عددها 80 في هذه المجموعة.
فتح الحزمة
k this deck
47
What are value-added activities? Value-added costs?
فتح الحزمة
افتح القفل للوصول البطاقات البالغ عددها 80 في هذه المجموعة.
فتح الحزمة
k this deck
48
Which of the following is an external failure cost (quality)?
a. Design reviews
b. Retesting
c. Rework
d. Lost sales
e. All of these.
a. Design reviews
b. Retesting
c. Rework
d. Lost sales
e. All of these.
فتح الحزمة
افتح القفل للوصول البطاقات البالغ عددها 80 في هذه المجموعة.
فتح الحزمة
k this deck
49
Activity-Based Product Costing
Suppose that a surgical ward has gathered the following information for four nursing activities and two types of patients:
Required:
1. Determine the total nursing costs assigned to each patient category.
2. Output is measured in patient days. Assuming that the normal patient category uses 8,000 patient days and the intensive patient category uses 6,400 patient days, calculate the nursing cost per patient day for each type of patient. (Round to two decimal places.)
3. CONCEPTUAL CONNECTION The supervisor of the surgical ward has suggested that patient days is the only driver needed to assign nursing costs to each type of patient. Calculate the charge per patient day (rounded to the nearest cent) using this approach and then explain to the supervisor why this would be a bad decision.
Suppose that a surgical ward has gathered the following information for four nursing activities and two types of patients:
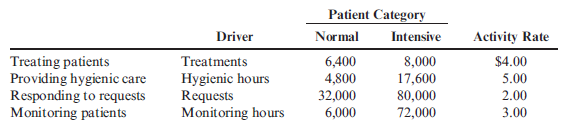
Required:
1. Determine the total nursing costs assigned to each patient category.
2. Output is measured in patient days. Assuming that the normal patient category uses 8,000 patient days and the intensive patient category uses 6,400 patient days, calculate the nursing cost per patient day for each type of patient. (Round to two decimal places.)
3. CONCEPTUAL CONNECTION The supervisor of the surgical ward has suggested that patient days is the only driver needed to assign nursing costs to each type of patient. Calculate the charge per patient day (rounded to the nearest cent) using this approach and then explain to the supervisor why this would be a bad decision.
فتح الحزمة
افتح القفل للوصول البطاقات البالغ عددها 80 في هذه المجموعة.
فتح الحزمة
k this deck
50
Activity Costing, Assigning Resource Costs, Primary and Secondary Activities
Elmo Clinic has identified three activities for daily maternity care: occupancy and feeding, nursing, and nursing supervision. The nursing supervisor oversees 150 nurses, 25 of whom are maternity nurses (the other nurses are located in other care areas such as the emergency room and intensive care). The nursing supervisor has three assistants, a secretary, several offices, computers, phones, and furniture. The three assistants spend 75% of their time on the supervising activity and 25% of their time as surgical nurses. They each receive a salary of $60,000. The nursing supervisor has a salary of $80,000. She spends 100% of her time supervising. The secretary receives a salary of $35,000 per year. Other costs directly traceable to the supervisory activity (depreciation, utilities, phone, etc.) average $170,000 per year.
Daily care output is measured as ''patient days.'' The clinic has traditionally assigned the cost of daily care by using a daily rate (a rate per patient day). Daily rates can differ between units, but within units the daily rates are the same for all patients. Under the traditional approach, the daily rate is computed by dividing the annual costs of occupancy and feeding, nursing, and a share of supervision by the unit's capacity expressed in patient days. The cost of supervision is assigned to each care area based on the number of nurses. A single driver (patient days) is used to assign the costs of daily care to each patient.
A pilot study has revealed that the demands for nursing care vary within the maternity unit, depending on the severity of a patient's case. Assume that the maternity unit has three levels of increasing severity: normal patients, cesarean patients, and patients with complications. The pilot study provided the following activity and cost information:
The pilot study also revealed the following information concerning the three types of patients and their annual demands:
Required:
1. Calculate the cost per patient day by using a functional-based approach.
2. Calculate the cost per patient day by using an activity-based approach. (Round rates and unit cost to two decimal places.)
3. CONCEPTUAL CONNECTION The hospital processes 1,250,000 pounds of laundry per year. The cost for the laundering activity is $600,000 per year. In a functional-based cost system, the cost of the laundry department is assigned to each user department in proportion to the pounds of laundry produced. Typically, maternity produces 240,000 pounds per year. How much would this change the cost per patient day calculated in Requirement 1? Now, describe what information you would need to modify the calculation made in Requirement 2. Under what conditions would this activity calculation provide a more accurate cost assignment?
Elmo Clinic has identified three activities for daily maternity care: occupancy and feeding, nursing, and nursing supervision. The nursing supervisor oversees 150 nurses, 25 of whom are maternity nurses (the other nurses are located in other care areas such as the emergency room and intensive care). The nursing supervisor has three assistants, a secretary, several offices, computers, phones, and furniture. The three assistants spend 75% of their time on the supervising activity and 25% of their time as surgical nurses. They each receive a salary of $60,000. The nursing supervisor has a salary of $80,000. She spends 100% of her time supervising. The secretary receives a salary of $35,000 per year. Other costs directly traceable to the supervisory activity (depreciation, utilities, phone, etc.) average $170,000 per year.
Daily care output is measured as ''patient days.'' The clinic has traditionally assigned the cost of daily care by using a daily rate (a rate per patient day). Daily rates can differ between units, but within units the daily rates are the same for all patients. Under the traditional approach, the daily rate is computed by dividing the annual costs of occupancy and feeding, nursing, and a share of supervision by the unit's capacity expressed in patient days. The cost of supervision is assigned to each care area based on the number of nurses. A single driver (patient days) is used to assign the costs of daily care to each patient.
A pilot study has revealed that the demands for nursing care vary within the maternity unit, depending on the severity of a patient's case. Assume that the maternity unit has three levels of increasing severity: normal patients, cesarean patients, and patients with complications. The pilot study provided the following activity and cost information:

The pilot study also revealed the following information concerning the three types of patients and their annual demands:
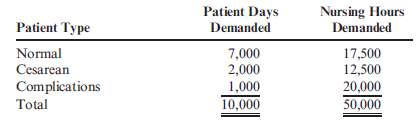
Required:
1. Calculate the cost per patient day by using a functional-based approach.
2. Calculate the cost per patient day by using an activity-based approach. (Round rates and unit cost to two decimal places.)
3. CONCEPTUAL CONNECTION The hospital processes 1,250,000 pounds of laundry per year. The cost for the laundering activity is $600,000 per year. In a functional-based cost system, the cost of the laundry department is assigned to each user department in proportion to the pounds of laundry produced. Typically, maternity produces 240,000 pounds per year. How much would this change the cost per patient day calculated in Requirement 1? Now, describe what information you would need to modify the calculation made in Requirement 2. Under what conditions would this activity calculation provide a more accurate cost assignment?
فتح الحزمة
افتح القفل للوصول البطاقات البالغ عددها 80 في هذه المجموعة.
فتح الحزمة
k this deck
51
Consider the information given on two products and their activity usage:
Refer to the information above. Suppose that machine hours are used to assign all overhead costs to the two products. Select the best answer from the following:
a. Laser printers are overcosted, and inkjet printers are undercosted.
b. Laser printers and inkjet printers are accurately costed.
c. Laser printers are undercosted, and inkjet printers are overcosted.
d. Using inspection hours to assign overhead costs is the most accurate approach.
e. None of the above.
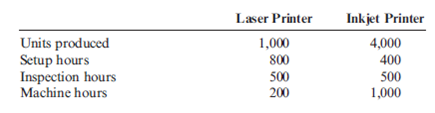
Refer to the information above. Suppose that machine hours are used to assign all overhead costs to the two products. Select the best answer from the following:
a. Laser printers are overcosted, and inkjet printers are undercosted.
b. Laser printers and inkjet printers are accurately costed.
c. Laser printers are undercosted, and inkjet printers are overcosted.
d. Using inspection hours to assign overhead costs is the most accurate approach.
e. None of the above.
فتح الحزمة
افتح القفل للوصول البطاقات البالغ عددها 80 في هذه المجموعة.
فتح الحزمة
k this deck
52
This year, Lambert Company will ship 1,500,000 pounds of goods to customers at a cost of $1,200,000. If a customer orders 10,000 pounds and produces $200,000 of revenue (total revenue is $20 million), the amount of shipping cost assigned to the customer by using ABC would be
a. unable to be determined.
b. $8,000 ($0.80 per pound shipped).
c. $24,000 (2% of the shipping cost).
d. $12,000 (1% of the shipping cost).
e. None of these.
a. unable to be determined.
b. $8,000 ($0.80 per pound shipped).
c. $24,000 (2% of the shipping cost).
d. $12,000 (1% of the shipping cost).
e. None of these.
فتح الحزمة
افتح القفل للوصول البطاقات البالغ عددها 80 في هذه المجموعة.
فتح الحزمة
k this deck
53
Which of the following represents environmental detection costs?
a. Depreciation on scrubbers
b. Recycling products
c. Disposing of toxic materials
d. Carrying out contamination tests
e. None of these.
a. Depreciation on scrubbers
b. Recycling products
c. Disposing of toxic materials
d. Carrying out contamination tests
e. None of these.
فتح الحزمة
افتح القفل للوصول البطاقات البالغ عددها 80 في هذه المجموعة.
فتح الحزمة
k this deck
54
Assigning Costs to Activities, Resource Drivers
The Receiving Department has three activities: unloading, counting goods, and inspecting. Unloading uses a forklift that is leased for $15,000 per year. The forklift is used only for unloading. The fuel for the forklift is $3,600 per year. Other operating costs (maintenance) for the forklift total $1,500 per year. Inspection uses some special testing equipment that has a depreciation of $1,200 per year and an operating cost of $750. Receiving has three employees who have an average salary of $50,000 per year. The work distribution matrix for the receiving personnel is as follows:
No other resources are used for these activities.
Required:
1. Calculate the cost of each activity.
2. CONCEPTUAL CONNECTION Explain the two methods used to assign costs to activities.
The Receiving Department has three activities: unloading, counting goods, and inspecting. Unloading uses a forklift that is leased for $15,000 per year. The forklift is used only for unloading. The fuel for the forklift is $3,600 per year. Other operating costs (maintenance) for the forklift total $1,500 per year. Inspection uses some special testing equipment that has a depreciation of $1,200 per year and an operating cost of $750. Receiving has three employees who have an average salary of $50,000 per year. The work distribution matrix for the receiving personnel is as follows:
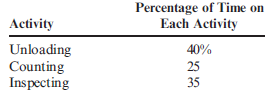
No other resources are used for these activities.
Required:
1. Calculate the cost of each activity.
2. CONCEPTUAL CONNECTION Explain the two methods used to assign costs to activities.
فتح الحزمة
افتح القفل للوصول البطاقات البالغ عددها 80 في هذه المجموعة.
فتح الحزمة
k this deck
55
Customers as a Cost Object
Morrisom National Bank has requested an analysis of checking account profitability by customer type. Customers are categorized according to the size of their account: low balances, medium balances, and high balances. The activities associated with the three different customer categories and their associated annual costs are as follows:
Additional data concerning the usage of the activities by the various customers are also provided:
Required:
( Note: Round answers to two decimal places.)
1. Calculate a cost per account per year by dividing the total cost of processing and maintaining checking accounts by the total number of accounts. What is the average fee per month that the bank should charge to cover the costs incurred because of checking accounts?
2. Calculate a cost per account by customer category by using activity rates.
3. Currently, the bank offers free checking to all of its customers. The interest revenues average $90 per account; however, the interest revenues earned per account by category are $80, $100, and $165 for the low-, medium-, and high-balance accounts, respectively. Calculate the average profit per account (average revenue minus average cost from Requirement 1). Then calculate the profit per account by using the revenue per customer type and the unit cost per customer type calculated in Requirement 2.
4. CONCEPTUAL CONNECTION After the analysis in Requirement 3, a vice president recommended eliminating the free checking feature for low-balance customers. The bank president expressed reluctance to do so, arguing that the low-balance customers more than made up for the loss through cross-sales. He presented a survey that showed that 50% of the customers would switch banks if a checking fee were imposed. Explain how you could verify the president's argument by using ABC.
Morrisom National Bank has requested an analysis of checking account profitability by customer type. Customers are categorized according to the size of their account: low balances, medium balances, and high balances. The activities associated with the three different customer categories and their associated annual costs are as follows:
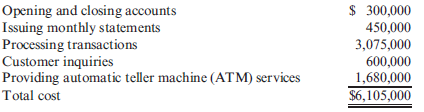
Additional data concerning the usage of the activities by the various customers are also provided:
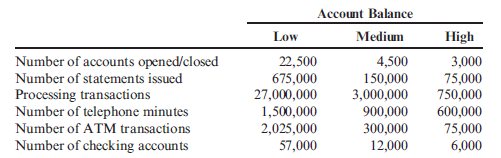
Required:
( Note: Round answers to two decimal places.)
1. Calculate a cost per account per year by dividing the total cost of processing and maintaining checking accounts by the total number of accounts. What is the average fee per month that the bank should charge to cover the costs incurred because of checking accounts?
2. Calculate a cost per account by customer category by using activity rates.
3. Currently, the bank offers free checking to all of its customers. The interest revenues average $90 per account; however, the interest revenues earned per account by category are $80, $100, and $165 for the low-, medium-, and high-balance accounts, respectively. Calculate the average profit per account (average revenue minus average cost from Requirement 1). Then calculate the profit per account by using the revenue per customer type and the unit cost per customer type calculated in Requirement 2.
4. CONCEPTUAL CONNECTION After the analysis in Requirement 3, a vice president recommended eliminating the free checking feature for low-balance customers. The bank president expressed reluctance to do so, arguing that the low-balance customers more than made up for the loss through cross-sales. He presented a survey that showed that 50% of the customers would switch banks if a checking fee were imposed. Explain how you could verify the president's argument by using ABC.
فتح الحزمة
افتح القفل للوصول البطاقات البالغ عددها 80 في هذه المجموعة.
فتح الحزمة
k this deck
56
What is an overhead consumption ratio?
فتح الحزمة
افتح القفل للوصول البطاقات البالغ عددها 80 في هذه المجموعة.
فتح الحزمة
k this deck
57
What are nonvalue-added activities? Nonvalue-added costs? Give an example of each.
فتح الحزمة
افتح القفل للوصول البطاقات البالغ عددها 80 في هذه المجموعة.
فتح الحزمة
k this deck
58
An example of an environmental internal failure cost is
a. cleaning up oil spills.
b. damaging ecosystems from solid waste disposal.
c. cost of operating scrubbers.
d. measuring levels of contamination.
e. None of these.
a. cleaning up oil spills.
b. damaging ecosystems from solid waste disposal.
c. cost of operating scrubbers.
d. measuring levels of contamination.
e. None of these.
فتح الحزمة
افتح القفل للوصول البطاقات البالغ عددها 80 في هذه المجموعة.
فتح الحزمة
k this deck
59
Activity-Based Customer-Driven Costs
Suppose that Stillwater Designs has two classes of distributors: JIT distributors and nonJIT distributors. The JIT distributor places small, frequent orders, and the nonJIT distributor tends to place larger, less frequent orders. Both types of distributors are buying the same product. Stillwater Designs provides the following information about customer-related activities and costs for the most recent quarter:
Required:
1. Calculate the total revenues per distributor category, and assign the customer costs to each distributor type by using revenues as the allocation base. Selling price for one unit is $150.
2. CONCEPTUAL CONNECTION Calculate the customer cost per distributor type using activity- based cost assignments. Discuss the merits of offering the nonJIT distributors a $2 price decrease (assume that they are agitating for a price concession).
3. CONCEPTUAL CONNECTION Assume that the JIT distributors are simply imposing the frequent orders on Stillwater Designs. No formal discussion has taken place between JIT customers and Stillwater Designs regarding the supply of goods on a JIT basis. The sales pattern has evolved over time. As an independent consultant, what would you suggest to Stillwater Designs' management?
Suppose that Stillwater Designs has two classes of distributors: JIT distributors and nonJIT distributors. The JIT distributor places small, frequent orders, and the nonJIT distributor tends to place larger, less frequent orders. Both types of distributors are buying the same product. Stillwater Designs provides the following information about customer-related activities and costs for the most recent quarter:
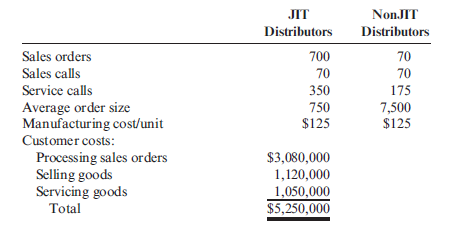
Required:
1. Calculate the total revenues per distributor category, and assign the customer costs to each distributor type by using revenues as the allocation base. Selling price for one unit is $150.
2. CONCEPTUAL CONNECTION Calculate the customer cost per distributor type using activity- based cost assignments. Discuss the merits of offering the nonJIT distributors a $2 price decrease (assume that they are agitating for a price concession).
3. CONCEPTUAL CONNECTION Assume that the JIT distributors are simply imposing the frequent orders on Stillwater Designs. No formal discussion has taken place between JIT customers and Stillwater Designs regarding the supply of goods on a JIT basis. The sales pattern has evolved over time. As an independent consultant, what would you suggest to Stillwater Designs' management?
فتح الحزمة
افتح القفل للوصول البطاقات البالغ عددها 80 في هذه المجموعة.
فتح الحزمة
k this deck
60
Activity-Based Costing and Customer-Driven Costs
Grundvig Manufacturing produces several types of bolts used in aircrafts. The bolts are produced in batches and grouped into three product families. Because the product families are used in different kinds of aircraft, customers also can be grouped into three categories, corresponding to the product family that they purchase. The number of units sold to each customer class is the same. The selling prices for the three product families range from $0.50 to $0.80 per unit. Historically, the costs of order entry, processing, and handling were expensed and not traced to individual customer groups. These costs are not trivial and totaled $9,000,000 for the most recent year. Recently, the company started emphasizing a cost reduction strategy with an emphasis on creating a competitive advantage.
Upon investigation, management discovered that order-filling costs were driven by the number of customer orders processed with the following cost behavior:
Step-fixed cost component: $50,000 per step (2,000 orders define a step)*
Variable cost component: $20 per order
* Grundvig currently has sufficient steps to process 200,000 orders.
The expected customer orders for the year total 200,000. The expected usage of the orderfilling activity and the average size of an order by customer category follow:
As a result of cost behavior analysis, the marketing manager recommended the imposition of a charge per customer order. The charge was implemented by adding the cost per order to the price of each order (computed by using the projected ordering costs and expected orders). This ordering cost was then reduced as the size of the order increased and was eliminated as the order size reached 2,000 units. Within a short period of communicating this new price information to customers, the average order size for all three product families increased to 2,000 units.
Required:
1. CONCEPTUAL CONNECTION Grundvig traditionally has expensed order-filling costs. What is the most likely reason for this practice?
2. Calculate the cost per order for each customer category. ( Note: Round to two decimal places.)
3. CONCEPTUAL CONNECTION Calculate the reduction in order-filling costs produced by the change in pricing strategy (assume that resource spending is reduced as much as possible and that the total units sold remain unchanged). Explain how exploiting customer activity information produced this cost reduction. Would any other internal activities benefit from this pricing strategy?
Grundvig Manufacturing produces several types of bolts used in aircrafts. The bolts are produced in batches and grouped into three product families. Because the product families are used in different kinds of aircraft, customers also can be grouped into three categories, corresponding to the product family that they purchase. The number of units sold to each customer class is the same. The selling prices for the three product families range from $0.50 to $0.80 per unit. Historically, the costs of order entry, processing, and handling were expensed and not traced to individual customer groups. These costs are not trivial and totaled $9,000,000 for the most recent year. Recently, the company started emphasizing a cost reduction strategy with an emphasis on creating a competitive advantage.
Upon investigation, management discovered that order-filling costs were driven by the number of customer orders processed with the following cost behavior:
Step-fixed cost component: $50,000 per step (2,000 orders define a step)*
Variable cost component: $20 per order
* Grundvig currently has sufficient steps to process 200,000 orders.
The expected customer orders for the year total 200,000. The expected usage of the orderfilling activity and the average size of an order by customer category follow:

As a result of cost behavior analysis, the marketing manager recommended the imposition of a charge per customer order. The charge was implemented by adding the cost per order to the price of each order (computed by using the projected ordering costs and expected orders). This ordering cost was then reduced as the size of the order increased and was eliminated as the order size reached 2,000 units. Within a short period of communicating this new price information to customers, the average order size for all three product families increased to 2,000 units.
Required:
1. CONCEPTUAL CONNECTION Grundvig traditionally has expensed order-filling costs. What is the most likely reason for this practice?
2. Calculate the cost per order for each customer category. ( Note: Round to two decimal places.)
3. CONCEPTUAL CONNECTION Calculate the reduction in order-filling costs produced by the change in pricing strategy (assume that resource spending is reduced as much as possible and that the total units sold remain unchanged). Explain how exploiting customer activity information produced this cost reduction. Would any other internal activities benefit from this pricing strategy?
فتح الحزمة
افتح القفل للوصول البطاقات البالغ عددها 80 في هذه المجموعة.
فتح الحزمة
k this deck
61
The first stage of ABC entails the assignment of
A) resource costs to departments.
B) activity costs to products or customers.
C) resource costs to a plantwide pool.
D) resource costs to distribution channels.
E) resource costs to individual activities.
A) resource costs to departments.
B) activity costs to products or customers.
C) resource costs to a plantwide pool.
D) resource costs to distribution channels.
E) resource costs to individual activities.
فتح الحزمة
افتح القفل للوصول البطاقات البالغ عددها 80 في هذه المجموعة.
فتح الحزمة
k this deck
62
Lambert Company has two suppliers: Deming and Leming. The cost of warranty work due to defective components is $2,000,000. The total units repaired under warranty average 100,000, of which 90,000 have components from Deming and 10,000 have components from Leming. Select the items below that represent true statements.
a. Components purchased from Leming cost $200,000 more than their purchase price.
b. Components purchased from Deming cost $1,800,000 more than their purchase price.
c. Components from Leming appear to be of higher quality.
d. All of the above are true.
e. None of the above is true.
a. Components purchased from Leming cost $200,000 more than their purchase price.
b. Components purchased from Deming cost $1,800,000 more than their purchase price.
c. Components from Leming appear to be of higher quality.
d. All of the above are true.
e. None of the above is true.
فتح الحزمة
افتح القفل للوصول البطاقات البالغ عددها 80 في هذه المجموعة.
فتح الحزمة
k this deck
63
An example of a societal cost is
a. medical care due to polluted air.
b. recycling scrap.
c. disposing of toxic materials.
d. maintaining pollution equipment.
e. All of these.
a. medical care due to polluted air.
b. recycling scrap.
c. disposing of toxic materials.
d. maintaining pollution equipment.
e. All of these.
فتح الحزمة
افتح القفل للوصول البطاقات البالغ عددها 80 في هذه المجموعة.
فتح الحزمة
k this deck
64
Activity-Based Supplier Costing
Bowman Company manufactures cooling systems. Bowman produces all the parts necessary for its product except for one electronic component, which is purchased from two local suppliers: Manzer Inc. and Buckner Company. Both suppliers are reliable and seldom deliver late; however, Manzer sells the component for $89 per unit, while Buckner sells the same component for $86. Bowman purchases 80% of its components from Buckner because of its lower price. The total annual demand is 4,000,000 components.
To help assess the cost effect of the two components, the following data were collected for supplier-related activities and suppliers:
I. Activity Data
II. Supplier Data
Required:
1. Calculate the cost per component for each supplier, taking into consideration the costs of the supplier-related activities and using the current prices and sales volume. ( Note : Round the unit cost to two decimal places.)
2. Suppose that Bowman loses $4,000,000 in sales per year because it develops a poor reputation due to defective units attributable to failed components. Using warranty hours, assign the cost of lost sales to each supplier. By how much would this change the cost of each supplier's component? (Round to two decimal places.)
3. CONCEPTUAL CONNECTION Based on the analysis in Requirements 1 and 2, discuss the importance of activity-based supplier costing for internal decision making.
Bowman Company manufactures cooling systems. Bowman produces all the parts necessary for its product except for one electronic component, which is purchased from two local suppliers: Manzer Inc. and Buckner Company. Both suppliers are reliable and seldom deliver late; however, Manzer sells the component for $89 per unit, while Buckner sells the same component for $86. Bowman purchases 80% of its components from Buckner because of its lower price. The total annual demand is 4,000,000 components.
To help assess the cost effect of the two components, the following data were collected for supplier-related activities and suppliers:
I. Activity Data

II. Supplier Data
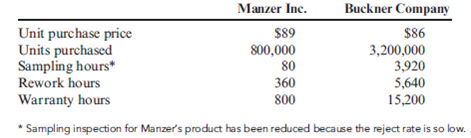
Required:
1. Calculate the cost per component for each supplier, taking into consideration the costs of the supplier-related activities and using the current prices and sales volume. ( Note : Round the unit cost to two decimal places.)
2. Suppose that Bowman loses $4,000,000 in sales per year because it develops a poor reputation due to defective units attributable to failed components. Using warranty hours, assign the cost of lost sales to each supplier. By how much would this change the cost of each supplier's component? (Round to two decimal places.)
3. CONCEPTUAL CONNECTION Based on the analysis in Requirements 1 and 2, discuss the importance of activity-based supplier costing for internal decision making.
فتح الحزمة
افتح القفل للوصول البطاقات البالغ عددها 80 في هذه المجموعة.
فتح الحزمة
k this deck
65
Activity-Based Supplier Costing
Levy Inc. manufactures tractors for agricultural usage. Levy purchases the engines needed for its tractors from two sources: Johnson Engines and Watson Company. The Johnson engine has a price of $1,000. The Watson engine is $900 per unit. Levy produces and sells 22,000 tractors. Of the 22,000 engines needed for the tractors, 4,000 are purchased from Johnson Engines, and 18,000 are purchased from Watson Company. The production manager, Jamie Murray, prefers the Johnson engine. However, Jan Booth, purchasing manager, maintains that the price difference is too great to buy more than the 4,000 units currently purchased. Booth also wants to maintain a significant connection with the Johnson source just in case the less expensive source cannot supply the needed quantities. Jamie, however, is convinced that the quality of the Johnson engine is worth the price difference.
Frank Wallace, the controller, has decided to use activity costing to resolve the issue. The following activity cost and supplier data have been collected:
Required:
1. CONCEPTUAL CONNECTION Calculate the activity-based supplier cost per engine (acquisition cost plus supplier-related activity costs). (Round to the nearest cent.) Which of the two suppliers is the low-cost supplier? Explain why this is a better measure of engine cost than the usual purchase costs assigned to the engines.
2. CONCEPTUAL CONNECTION Consider the supplier cost information obtained in Requirement 1. Suppose further that Johnson can only supply a total of 20,000 units. What actions would you advise Levy to undertake with its suppliers?
Levy Inc. manufactures tractors for agricultural usage. Levy purchases the engines needed for its tractors from two sources: Johnson Engines and Watson Company. The Johnson engine has a price of $1,000. The Watson engine is $900 per unit. Levy produces and sells 22,000 tractors. Of the 22,000 engines needed for the tractors, 4,000 are purchased from Johnson Engines, and 18,000 are purchased from Watson Company. The production manager, Jamie Murray, prefers the Johnson engine. However, Jan Booth, purchasing manager, maintains that the price difference is too great to buy more than the 4,000 units currently purchased. Booth also wants to maintain a significant connection with the Johnson source just in case the less expensive source cannot supply the needed quantities. Jamie, however, is convinced that the quality of the Johnson engine is worth the price difference.
Frank Wallace, the controller, has decided to use activity costing to resolve the issue. The following activity cost and supplier data have been collected:
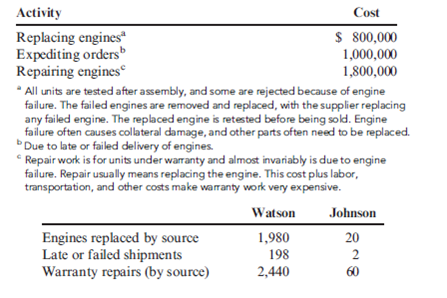
Required:
1. CONCEPTUAL CONNECTION Calculate the activity-based supplier cost per engine (acquisition cost plus supplier-related activity costs). (Round to the nearest cent.) Which of the two suppliers is the low-cost supplier? Explain why this is a better measure of engine cost than the usual purchase costs assigned to the engines.
2. CONCEPTUAL CONNECTION Consider the supplier cost information obtained in Requirement 1. Suppose further that Johnson can only supply a total of 20,000 units. What actions would you advise Levy to undertake with its suppliers?
فتح الحزمة
افتح القفل للوصول البطاقات البالغ عددها 80 في هذه المجموعة.
فتح الحزمة
k this deck
66
What is activity-based product costing?
فتح الحزمة
افتح القفل للوصول البطاقات البالغ عددها 80 في هذه المجموعة.
فتح الحزمة
k this deck
67
Identify and define four different ways to manage activities so that costs can be reduced.
فتح الحزمة
افتح القفل للوصول البطاقات البالغ عددها 80 في هذه المجموعة.
فتح الحزمة
k this deck
68
An example of an environmental prevention cost is
a. restoring land to its natural state.
b. auditing environmental activities.
c. licensing facilities for producing contaminants.
d. developing environmental management systems.
e. treating toxic materials.
a. restoring land to its natural state.
b. auditing environmental activities.
c. licensing facilities for producing contaminants.
d. developing environmental management systems.
e. treating toxic materials.
فتح الحزمة
افتح القفل للوصول البطاقات البالغ عددها 80 في هذه المجموعة.
فتح الحزمة
k this deck
69
Nonvalue-Added Costs
The following six situations at Diviney Manufacturing Inc. are independent.
a. A manual insertion process takes 30 minutes and 8 pounds of material to produce a product. Automating the insertion process requires 15 minutes of machine time and 7.5 pounds of material. The cost per labor hour is $12, the cost per machine hour is $8, and the cost per pound of materials is $10.
b. With its original design, a gear requires 8 hours of setup time. By redesigning the gear so that the number of different grooves needed is reduced by 50% the setup time is reduced by 75%. The cost per setup hour is $50.
c. A product currently requires 6 moves. By redesigning the manufacturing layout, the number of moves can be reduced from 6 to 0. The cost per move is $20.
d. Inspection time for a plant is 16,000 hours per year. The cost of inspection consists of salaries of 8 inspectors, totaling $320,000. Inspection also uses supplies costing $5 per inspection hour. The company eliminated most defective components by eliminating low-quality suppliers. The number of production errors was reduced dramatically by installing a system of statistical process control. Further quality improvements were realized by redesigning the products, making them easier to manufacture. The net effect was to achieve a close to zero-defect state and eliminate the need for any inspection activity.
e. Each unit of a product requires 6 components. The average number of components is 6.5 due to component failure, requiring rework and extra components. Developing relations with the right suppliers and increasing the quality of the purchased component can reduce the average number of components to 6 components per unit. The cost per component is $500.
f. A plant produces 100 different electronic products. Each product requires an average of 8 components that are purchased externally. The components are different for each part. By redesigning the products, it is possible to produce the 100 products so that they all have 4 components in common. This will reduce the demand for purchasing, receiving, and paying bills. Estimated savings from the reduced demand are $900,000 per year.
Refer to the information for Diviney Manufacturing above.
Required:
Estimate the nonvalue-added cost for each situation.
The following six situations at Diviney Manufacturing Inc. are independent.
a. A manual insertion process takes 30 minutes and 8 pounds of material to produce a product. Automating the insertion process requires 15 minutes of machine time and 7.5 pounds of material. The cost per labor hour is $12, the cost per machine hour is $8, and the cost per pound of materials is $10.
b. With its original design, a gear requires 8 hours of setup time. By redesigning the gear so that the number of different grooves needed is reduced by 50% the setup time is reduced by 75%. The cost per setup hour is $50.
c. A product currently requires 6 moves. By redesigning the manufacturing layout, the number of moves can be reduced from 6 to 0. The cost per move is $20.
d. Inspection time for a plant is 16,000 hours per year. The cost of inspection consists of salaries of 8 inspectors, totaling $320,000. Inspection also uses supplies costing $5 per inspection hour. The company eliminated most defective components by eliminating low-quality suppliers. The number of production errors was reduced dramatically by installing a system of statistical process control. Further quality improvements were realized by redesigning the products, making them easier to manufacture. The net effect was to achieve a close to zero-defect state and eliminate the need for any inspection activity.
e. Each unit of a product requires 6 components. The average number of components is 6.5 due to component failure, requiring rework and extra components. Developing relations with the right suppliers and increasing the quality of the purchased component can reduce the average number of components to 6 components per unit. The cost per component is $500.
f. A plant produces 100 different electronic products. Each product requires an average of 8 components that are purchased externally. The components are different for each part. By redesigning the products, it is possible to produce the 100 products so that they all have 4 components in common. This will reduce the demand for purchasing, receiving, and paying bills. Estimated savings from the reduced demand are $900,000 per year.
Refer to the information for Diviney Manufacturing above.
Required:
Estimate the nonvalue-added cost for each situation.
فتح الحزمة
افتح القفل للوصول البطاقات البالغ عددها 80 في هذه المجموعة.
فتح الحزمة
k this deck
70
Activity-Based Management, Nonvalue-Added Costs
Danna Martin, president of Mays Electronics, was concerned about the end-of-the year marketing report that she had just received. According to Larry Savage, marketing manager, a price decrease for the coming year was again needed to maintain the company's annual sales volume of integrated circuit boards (CBs). This would make a bad situation worse. The current selling price of $18 per unit was producing a $2-per-unit profit-half the customary $4-per-unit profit. Foreign competitors kept reducing their prices. To match the latest reduction would reduce the price from $18 to $14. This would put the price below the cost to produce and sell it. How could these firms sell for such a low price? Determined to find out if there were problems with the company's operations, Danna decided to hire a consultant to evaluate the way in which the CBs were produced and sold. After two weeks, the consultant had identified the following activities and costs:
The consultant indicated that some preliminary activity analysis shows that per-unit costs can be reduced by at least $7. Since the marketing manager had indicated that the market share (sales volume) for the boards could be increased by 50% if the price could be reduced to $12, Danna became quite excited.
Required:
1. CONCEPTUAL CONNECTION What is activity-based management? What phases of activity analysis did the consultant provide? What else remains to be done?
2. CONCEPTUAL CONNECTION Identify as many nonvalue-added costs as possible. Compute the cost savings per unit that would be realized if these costs were eliminated. Was the consultant correct in the preliminary cost reduction assessment? Discuss actions that the company can take to reduce or eliminate the nonvalue-added activities.
3. Compute the unit cost required to maintain current market share, while earning a profit of $4 per unit. Now compute the unit cost required to expand sales by 50%, assuming a per unit profit of $4. How much cost reduction would be required to achieve each unit cost?
4. Assume that further activity analysis revealed the following: switching to automated insertion would save $60,000 of engineering support and $90,000 of direct labor. Now, what is the total potential cost reduction per unit available from activity analysis? With these additional reductions, can Mays achieve the unit cost to maintain current sales? To increase it by 50%? What form of activity analysis is this: reduction, sharing, elimination, or selection?
5. CONCEPTUAL CONNECTION Calculate income based on current sales, prices, and costs. Then calculate the income by using a $14 price and a $12 price, assuming that the maximum cost reduction possible is achieved (including Requirement 4's reduction). What price should be selected?
Danna Martin, president of Mays Electronics, was concerned about the end-of-the year marketing report that she had just received. According to Larry Savage, marketing manager, a price decrease for the coming year was again needed to maintain the company's annual sales volume of integrated circuit boards (CBs). This would make a bad situation worse. The current selling price of $18 per unit was producing a $2-per-unit profit-half the customary $4-per-unit profit. Foreign competitors kept reducing their prices. To match the latest reduction would reduce the price from $18 to $14. This would put the price below the cost to produce and sell it. How could these firms sell for such a low price? Determined to find out if there were problems with the company's operations, Danna decided to hire a consultant to evaluate the way in which the CBs were produced and sold. After two weeks, the consultant had identified the following activities and costs:
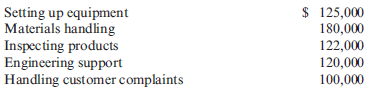
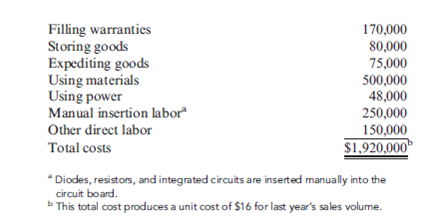
The consultant indicated that some preliminary activity analysis shows that per-unit costs can be reduced by at least $7. Since the marketing manager had indicated that the market share (sales volume) for the boards could be increased by 50% if the price could be reduced to $12, Danna became quite excited.
Required:
1. CONCEPTUAL CONNECTION What is activity-based management? What phases of activity analysis did the consultant provide? What else remains to be done?
2. CONCEPTUAL CONNECTION Identify as many nonvalue-added costs as possible. Compute the cost savings per unit that would be realized if these costs were eliminated. Was the consultant correct in the preliminary cost reduction assessment? Discuss actions that the company can take to reduce or eliminate the nonvalue-added activities.
3. Compute the unit cost required to maintain current market share, while earning a profit of $4 per unit. Now compute the unit cost required to expand sales by 50%, assuming a per unit profit of $4. How much cost reduction would be required to achieve each unit cost?
4. Assume that further activity analysis revealed the following: switching to automated insertion would save $60,000 of engineering support and $90,000 of direct labor. Now, what is the total potential cost reduction per unit available from activity analysis? With these additional reductions, can Mays achieve the unit cost to maintain current sales? To increase it by 50%? What form of activity analysis is this: reduction, sharing, elimination, or selection?
5. CONCEPTUAL CONNECTION Calculate income based on current sales, prices, and costs. Then calculate the income by using a $14 price and a $12 price, assuming that the maximum cost reduction possible is achieved (including Requirement 4's reduction). What price should be selected?
فتح الحزمة
افتح القفل للوصول البطاقات البالغ عددها 80 في هذه المجموعة.
فتح الحزمة
k this deck
71
The second stage of ABC entails the assignment of
A) activity costs to products or customers.
B) resource costs to departments.
C) resource costs to a plantwide pool.
D) resource costs to individual activities.
E) resource costs to distribution channels.
A) activity costs to products or customers.
B) resource costs to departments.
C) resource costs to a plantwide pool.
D) resource costs to individual activities.
E) resource costs to distribution channels.
فتح الحزمة
افتح القفل للوصول البطاقات البالغ عددها 80 في هذه المجموعة.
فتح الحزمة
k this deck
72
A forklift and its driver used for moving materials are examples of
a. activity inputs.
b. activity output measures.
c. resource drivers.
d. activity outputs.
e. root causes.
a. activity inputs.
b. activity output measures.
c. resource drivers.
d. activity outputs.
e. root causes.
فتح الحزمة
افتح القفل للوصول البطاقات البالغ عددها 80 في هذه المجموعة.
فتح الحزمة
k this deck
73
Consumption Ratios
Botas Company produces two types of boots: vaquero and vaquera. There are four activities associated with the two products. Drivers for the four activities are as follows:
Refer to the information for Botas Company on the previous page.
Required:
1. Calculate the consumption ratios for the four drivers.
2. Is there evidence of product diversity? Explain.
Botas Company produces two types of boots: vaquero and vaquera. There are four activities associated with the two products. Drivers for the four activities are as follows:
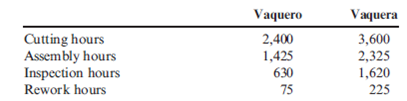
Refer to the information for Botas Company on the previous page.
Required:
1. Calculate the consumption ratios for the four drivers.
2. Is there evidence of product diversity? Explain.
فتح الحزمة
افتح القفل للوصول البطاقات البالغ عددها 80 في هذه المجموعة.
فتح الحزمة
k this deck
74
Driver Analysis
The following six situations at Diviney Manufacturing Inc. are independent.
a. A manual insertion process takes 30 minutes and 8 pounds of material to produce a product. Automating the insertion process requires 15 minutes of machine time and 7.5 pounds of material. The cost per labor hour is $12, the cost per machine hour is $8, and the cost per pound of materials is $10.
b. With its original design, a gear requires 8 hours of setup time. By redesigning the gear so that the number of different grooves needed is reduced by 50% the setup time is reduced by 75%. The cost per setup hour is $50.
c. A product currently requires 6 moves. By redesigning the manufacturing layout, the number of moves can be reduced from 6 to 0. The cost per move is $20.
d. Inspection time for a plant is 16,000 hours per year. The cost of inspection consists of salaries of 8 inspectors, totaling $320,000. Inspection also uses supplies costing $5 per inspection hour. The company eliminated most defective components by eliminating low-quality suppliers. The number of production errors was reduced dramatically by installing a system of statistical process control. Further quality improvements were realized by redesigning the products, making them easier to manufacture. The net effect was to achieve a close to zero-defect state and eliminate the need for any inspection activity.
e. Each unit of a product requires 6 components. The average number of components is 6.5 due to component failure, requiring rework and extra components. Developing relations with the right suppliers and increasing the quality of the purchased component can reduce the average number of components to 6 components per unit. The cost per component is $500.
f. A plant produces 100 different electronic products. Each product requires an average of 8 components that are purchased externally. The components are different for each part. By redesigning the products, it is possible to produce the 100 products so that they all have 4 components in common. This will reduce the demand for purchasing, receiving, and paying bills. Estimated savings from the reduced demand are $900,000 per year.
Refer to the information for Diviney Manufacturing above.
Required:
CONCEPTUAL CONNECTION For each situation, identify the possible root cause(s) of the activity cost (such as plant layout, process design, and product design).
The following six situations at Diviney Manufacturing Inc. are independent.
a. A manual insertion process takes 30 minutes and 8 pounds of material to produce a product. Automating the insertion process requires 15 minutes of machine time and 7.5 pounds of material. The cost per labor hour is $12, the cost per machine hour is $8, and the cost per pound of materials is $10.
b. With its original design, a gear requires 8 hours of setup time. By redesigning the gear so that the number of different grooves needed is reduced by 50% the setup time is reduced by 75%. The cost per setup hour is $50.
c. A product currently requires 6 moves. By redesigning the manufacturing layout, the number of moves can be reduced from 6 to 0. The cost per move is $20.
d. Inspection time for a plant is 16,000 hours per year. The cost of inspection consists of salaries of 8 inspectors, totaling $320,000. Inspection also uses supplies costing $5 per inspection hour. The company eliminated most defective components by eliminating low-quality suppliers. The number of production errors was reduced dramatically by installing a system of statistical process control. Further quality improvements were realized by redesigning the products, making them easier to manufacture. The net effect was to achieve a close to zero-defect state and eliminate the need for any inspection activity.
e. Each unit of a product requires 6 components. The average number of components is 6.5 due to component failure, requiring rework and extra components. Developing relations with the right suppliers and increasing the quality of the purchased component can reduce the average number of components to 6 components per unit. The cost per component is $500.
f. A plant produces 100 different electronic products. Each product requires an average of 8 components that are purchased externally. The components are different for each part. By redesigning the products, it is possible to produce the 100 products so that they all have 4 components in common. This will reduce the demand for purchasing, receiving, and paying bills. Estimated savings from the reduced demand are $900,000 per year.
Refer to the information for Diviney Manufacturing above.
Required:
CONCEPTUAL CONNECTION For each situation, identify the possible root cause(s) of the activity cost (such as plant layout, process design, and product design).
فتح الحزمة
افتح القفل للوصول البطاقات البالغ عددها 80 في هذه المجموعة.
فتح الحزمة
k this deck
75
Nonvalue-Added Costs, Activity Costs, Activity Cost Reduction
John Thomas, vice president of Mallett Company (a producer of a variety of plastic products), has been supervising the implementation of an ABC management system. John wants to improve process efficiency by improving the activities that define the processes. To illustrate the potential of the new system to the president, John has decided to focus on two processes: production and customer service.
Within each process, one activity will be selected for improvement: materials usage for production and sustaining engineering for customer service (sustaining engineers are responsible for redesigning products based on customer needs and feedback). Value-added standards are identified for each activity. For materials usage, the value-added standard calls for six pounds per unit of output (the products differ in shape and function, but their weight is uniform). The valueadded standard is based on the elimination of all waste due to defective molds. The standard price of materials is $5 per pound. For sustaining engineering, the standard is 58% of current practical activity capacity. This standard is based on the fact that about 42% of the complaints have to do with design features that could have been avoided or anticipated by the company.
Current practical capacity (at the end of 2015) is defined by the following requirements: 6,000 engineering hours for each product group that has been on the market or in development for 5 years or less and 2,400 hours per product group of more than 5 years. Four product groups have less than 5 years' experience, and 10 product groups have more. Each of the 24 engineers is paid a salary of $60,000. Each engineer can provide 2,000 hours of service per year. No other significant costs are incurred for the engineering activity.
Actual materials usage for 2015 was 25% above the level called for by the value-added standard; engineering usage was 46,000 hours. A total of 80,000 units of output were produced. John and the operational managers have selected some improvement measures that promise to reduce nonvalue-added activity usage by 40% in 2016. Selected actual results achieved for 2016 are as follows:
The actual prices paid for materials and engineering hours are identical to the standard or budgeted prices.
Required:
1. For 2015, calculate the nonvalue-added usage and costs for materials usage and sustaining engineering.
2. CONCEPTUAL CONNECTION Using the budgeted improvements, calculate the expected activity usage levels for 2016. Now, compute the 2016 usage variances (the difference between the expected and actual values), expressed in both physical and financial measures, for materials and engineering. Comment on the company's ability to achieve its targeted reductions. In particular, discuss what measures the company must take to capture any realized reductions in resource usage.
John Thomas, vice president of Mallett Company (a producer of a variety of plastic products), has been supervising the implementation of an ABC management system. John wants to improve process efficiency by improving the activities that define the processes. To illustrate the potential of the new system to the president, John has decided to focus on two processes: production and customer service.
Within each process, one activity will be selected for improvement: materials usage for production and sustaining engineering for customer service (sustaining engineers are responsible for redesigning products based on customer needs and feedback). Value-added standards are identified for each activity. For materials usage, the value-added standard calls for six pounds per unit of output (the products differ in shape and function, but their weight is uniform). The valueadded standard is based on the elimination of all waste due to defective molds. The standard price of materials is $5 per pound. For sustaining engineering, the standard is 58% of current practical activity capacity. This standard is based on the fact that about 42% of the complaints have to do with design features that could have been avoided or anticipated by the company.
Current practical capacity (at the end of 2015) is defined by the following requirements: 6,000 engineering hours for each product group that has been on the market or in development for 5 years or less and 2,400 hours per product group of more than 5 years. Four product groups have less than 5 years' experience, and 10 product groups have more. Each of the 24 engineers is paid a salary of $60,000. Each engineer can provide 2,000 hours of service per year. No other significant costs are incurred for the engineering activity.
Actual materials usage for 2015 was 25% above the level called for by the value-added standard; engineering usage was 46,000 hours. A total of 80,000 units of output were produced. John and the operational managers have selected some improvement measures that promise to reduce nonvalue-added activity usage by 40% in 2016. Selected actual results achieved for 2016 are as follows:

The actual prices paid for materials and engineering hours are identical to the standard or budgeted prices.
Required:
1. For 2015, calculate the nonvalue-added usage and costs for materials usage and sustaining engineering.
2. CONCEPTUAL CONNECTION Using the budgeted improvements, calculate the expected activity usage levels for 2016. Now, compute the 2016 usage variances (the difference between the expected and actual values), expressed in both physical and financial measures, for materials and engineering. Comment on the company's ability to achieve its targeted reductions. In particular, discuss what measures the company must take to capture any realized reductions in resource usage.
فتح الحزمة
افتح القفل للوصول البطاقات البالغ عددها 80 في هذه المجموعة.
فتح الحزمة
k this deck
76
What is an activity dictionary?
فتح الحزمة
افتح القفل للوصول البطاقات البالغ عددها 80 في هذه المجموعة.
فتح الحزمة
k this deck
77
What is cycle time? Velocity?
فتح الحزمة
افتح القفل للوصول البطاقات البالغ عددها 80 في هذه المجموعة.
فتح الحزمة
k this deck
78
Activity Rates
Botas Company produces two types of boots: vaquero and vaquera. There are four activities associated with the two products. Drivers for the four activities are as follows:
Refer to the information for Botas Company on the previous page. The following activity data have been collected:
Required:
Calculate the activity rates that would be used to assign costs to each product.
Botas Company produces two types of boots: vaquero and vaquera. There are four activities associated with the two products. Drivers for the four activities are as follows:
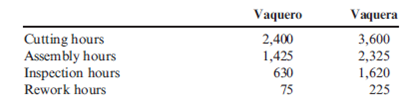
Refer to the information for Botas Company on the previous page. The following activity data have been collected:
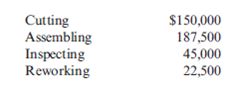
Required:
Calculate the activity rates that would be used to assign costs to each product.
فتح الحزمة
افتح القفل للوصول البطاقات البالغ عددها 80 في هذه المجموعة.
فتح الحزمة
k this deck
79
Type of Activity Management
The following six situations at Diviney Manufacturing Inc. are independent.
a. A manual insertion process takes 30 minutes and 8 pounds of material to produce a product. Automating the insertion process requires 15 minutes of machine time and 7.5 pounds of material. The cost per labor hour is $12, the cost per machine hour is $8, and the cost per pound of materials is $10.
b. With its original design, a gear requires 8 hours of setup time. By redesigning the gear so that the number of different grooves needed is reduced by 50% the setup time is reduced by 75%. The cost per setup hour is $50.
c. A product currently requires 6 moves. By redesigning the manufacturing layout, the number of moves can be reduced from 6 to 0. The cost per move is $20.
d. Inspection time for a plant is 16,000 hours per year. The cost of inspection consists of salaries of 8 inspectors, totaling $320,000. Inspection also uses supplies costing $5 per inspection hour. The company eliminated most defective components by eliminating low-quality suppliers. The number of production errors was reduced dramatically by installing a system of statistical process control. Further quality improvements were realized by redesigning the products, making them easier to manufacture. The net effect was to achieve a close to zero-defect state and eliminate the need for any inspection activity.
e. Each unit of a product requires 6 components. The average number of components is 6.5 due to component failure, requiring rework and extra components. Developing relations with the right suppliers and increasing the quality of the purchased component can reduce the average number of components to 6 components per unit. The cost per component is $500.
f. A plant produces 100 different electronic products. Each product requires an average of 8 components that are purchased externally. The components are different for each part. By redesigning the products, it is possible to produce the 100 products so that they all have 4 components in common. This will reduce the demand for purchasing, receiving, and paying bills. Estimated savings from the reduced demand are $900,000 per year.
Refer to the information for Diviney Manufacturing on the previous page.
Required:
For each situation, identify the cost reduction measure: activity elimination, activity reduction, activity sharing, or activity selection.
The following six situations at Diviney Manufacturing Inc. are independent.
a. A manual insertion process takes 30 minutes and 8 pounds of material to produce a product. Automating the insertion process requires 15 minutes of machine time and 7.5 pounds of material. The cost per labor hour is $12, the cost per machine hour is $8, and the cost per pound of materials is $10.
b. With its original design, a gear requires 8 hours of setup time. By redesigning the gear so that the number of different grooves needed is reduced by 50% the setup time is reduced by 75%. The cost per setup hour is $50.
c. A product currently requires 6 moves. By redesigning the manufacturing layout, the number of moves can be reduced from 6 to 0. The cost per move is $20.
d. Inspection time for a plant is 16,000 hours per year. The cost of inspection consists of salaries of 8 inspectors, totaling $320,000. Inspection also uses supplies costing $5 per inspection hour. The company eliminated most defective components by eliminating low-quality suppliers. The number of production errors was reduced dramatically by installing a system of statistical process control. Further quality improvements were realized by redesigning the products, making them easier to manufacture. The net effect was to achieve a close to zero-defect state and eliminate the need for any inspection activity.
e. Each unit of a product requires 6 components. The average number of components is 6.5 due to component failure, requiring rework and extra components. Developing relations with the right suppliers and increasing the quality of the purchased component can reduce the average number of components to 6 components per unit. The cost per component is $500.
f. A plant produces 100 different electronic products. Each product requires an average of 8 components that are purchased externally. The components are different for each part. By redesigning the products, it is possible to produce the 100 products so that they all have 4 components in common. This will reduce the demand for purchasing, receiving, and paying bills. Estimated savings from the reduced demand are $900,000 per year.
Refer to the information for Diviney Manufacturing on the previous page.
Required:
For each situation, identify the cost reduction measure: activity elimination, activity reduction, activity sharing, or activity selection.
فتح الحزمة
افتح القفل للوصول البطاقات البالغ عددها 80 في هذه المجموعة.
فتح الحزمة
k this deck
80
Cycle Time, Velocity, Product Costing
Goldman Company has a JIT system in place. Each manufacturing cell is dedicated to the production of a single product or major subassembly. One cell, dedicated to the production of telescopes, has four operations: machining, finishing, assembly, and qualifying (testing).
For the coming year, the telescope cell has the following budgeted costs and cell time (both at theoretical capacity):
During the year, the following actual results were obtained:
Required:
( Note: Round answers to two decimal places.)
1. Compute the velocity (number of telescopes per hour) that the cell can theoretically achieve. Now, compute the theoretical cycle time (number of hours or minutes per telescope) that it takes to produce one telescope.
2. Compute the actual velocity and the actual cycle time.
3. CONCEPTUAL CONNECTION Compute the budgeted conversion costs per minute. Using this rate, compute the conversion costs per telescope if theoretical output is achieved. Using this measure, compute the conversion costs per telescope for actual output. Does this product costing approach provide an incentive for the cell manager to reduce cycle time? Explain.
Goldman Company has a JIT system in place. Each manufacturing cell is dedicated to the production of a single product or major subassembly. One cell, dedicated to the production of telescopes, has four operations: machining, finishing, assembly, and qualifying (testing).
For the coming year, the telescope cell has the following budgeted costs and cell time (both at theoretical capacity):

During the year, the following actual results were obtained:


( Note: Round answers to two decimal places.)
1. Compute the velocity (number of telescopes per hour) that the cell can theoretically achieve. Now, compute the theoretical cycle time (number of hours or minutes per telescope) that it takes to produce one telescope.
2. Compute the actual velocity and the actual cycle time.
3. CONCEPTUAL CONNECTION Compute the budgeted conversion costs per minute. Using this rate, compute the conversion costs per telescope if theoretical output is achieved. Using this measure, compute the conversion costs per telescope for actual output. Does this product costing approach provide an incentive for the cell manager to reduce cycle time? Explain.
فتح الحزمة
افتح القفل للوصول البطاقات البالغ عددها 80 في هذه المجموعة.
فتح الحزمة
k this deck