Deck 14: Operational Performance Measurement: Sales, Direct-Cost Variances, and the Role of Nonfinancial Performance Measures
سؤال
سؤال
سؤال
سؤال
سؤال
سؤال
سؤال
سؤال
سؤال
سؤال
سؤال
سؤال
سؤال
سؤال
سؤال
سؤال
سؤال
سؤال
سؤال
سؤال
سؤال
سؤال
سؤال
سؤال
سؤال
سؤال
سؤال
سؤال
سؤال
سؤال
سؤال
سؤال
سؤال
سؤال
سؤال
سؤال
سؤال
سؤال
سؤال
سؤال
سؤال
سؤال
سؤال
سؤال
سؤال
سؤال
سؤال
سؤال
سؤال
سؤال
سؤال
سؤال
سؤال
سؤال
فتح الحزمة
قم بالتسجيل لفتح البطاقات في هذه المجموعة!
Unlock Deck
Unlock Deck
1/54
العب
ملء الشاشة (f)
Deck 14: Operational Performance Measurement: Sales, Direct-Cost Variances, and the Role of Nonfinancial Performance Measures
1
Explain how standard costs and flexible budgets can be used for short-term profit analysis, that is, for financial control purposes.
Direct cost Sales variance Control Systems
Sales variance is the breakdown of sales volume and which includes components like manufacturing cost (which is a direct cost), labour cost, material costs. Certain procedures are set in place, which help the organisation to control performance, which will include components from planning to evaluation. Similarly, operational financial controls are also applied for cost control in their respective areas.
Discussion and analysis:
Construction of operating earnings for a period, planned amount or established targets and flexible budgets, standard costs are used. The difference between operating earning specified in firm's static budget and actual earning for that period can be determined using standard costs. Sales volume, sales mix, selling prices, variable costs per unit and total fixed costs are the five factors that combines to determines operating income and the five factors attributable portion makes total operating income variance.
Sales variance is the breakdown of sales volume and which includes components like manufacturing cost (which is a direct cost), labour cost, material costs. Certain procedures are set in place, which help the organisation to control performance, which will include components from planning to evaluation. Similarly, operational financial controls are also applied for cost control in their respective areas.
Discussion and analysis:
Construction of operating earnings for a period, planned amount or established targets and flexible budgets, standard costs are used. The difference between operating earning specified in firm's static budget and actual earning for that period can be determined using standard costs. Sales volume, sales mix, selling prices, variable costs per unit and total fixed costs are the five factors that combines to determines operating income and the five factors attributable portion makes total operating income variance.
2
Refer to Exhibit 14.8 and the accompanying discussion in the text. Demonstrate that the materials usage variance for PVC during October 2016 was $2,400F.
EXHIBIT 14.8 A Detailed Comparison of Actual Variable Costs and Flexible-Budget Variable Costs: Product XV-1 (October 2016 )
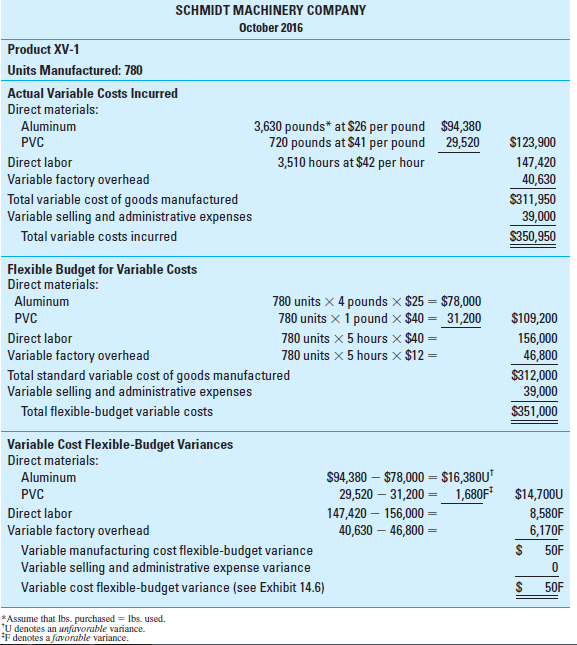
EXHIBIT 14.8 A Detailed Comparison of Actual Variable Costs and Flexible-Budget Variable Costs: Product XV-1 (October 2016 )
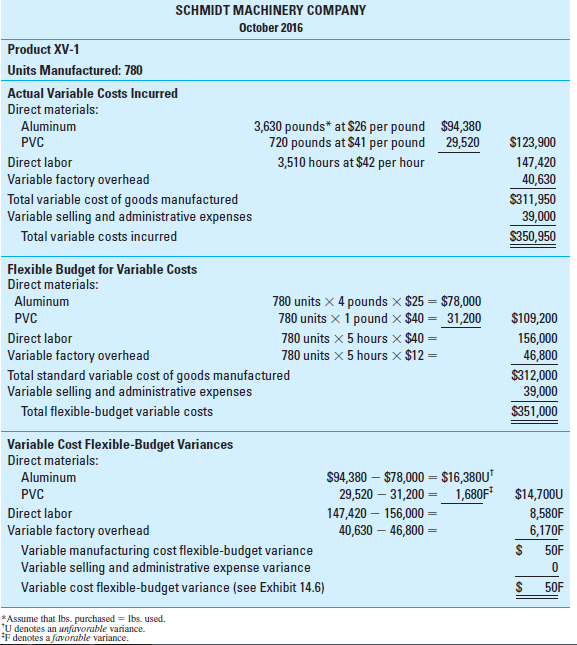
Analysis of variances can be defined as the comparison between the actual data and the budgeted data. In other words it can be said that the variances are derived from the difference between the actual and standard data. The budgets are made by management usually based on the actual data of the past year. The variance analysis helps the management to identify the cost and revenue center performance.
In the present case, we calculate material usage variance for PVC during October 2016. Material usage variance is the difference between the standard quantity specified for actual production and the actual quantity used at standard purchase price. In other words,
A variance can be favorable (F) or unfavorable (U). A variance is considered favorable if it improves net income and unfavorable if it decreases income. Therefore, when actual revenues exceed budgeted amounts, the resulting variance is favorable. When actual revenues fall short of budgeted amounts, the variance is unfavorable. In present case, actual operating income is higher than that of budgeted. Hence, the variance is favorable (F ).
To conclude it can be said that the material usage variance is $ 2,400 (F).
In the present case, we calculate material usage variance for PVC during October 2016. Material usage variance is the difference between the standard quantity specified for actual production and the actual quantity used at standard purchase price. In other words,

To conclude it can be said that the material usage variance is $ 2,400 (F).
3
Standard Costs and Ethics Ohio Apple Orchards (OAO), Inc., produces an organic, super-premium apple juice that it markets to specialty food outlets. OAO purchases its apples from a select group of farmers located in the Midwest. Recently, a graduate of the local university, Susanna Wu, joined the staff of OAO. Among Susanna's first responsibilities was the charge to develop and implement a standard costing system for OAO, this in response to competition arising from new and aggressive entrants to the organic foods market. Susanna discussed her task with the controller of the company, Mary Whitman, who indicated that unrefined apple juice would cost $1.50 per liter, the price she intended to pay her college pal, Bill O'Neal, who had since graduation been operating his own apple orchard at a loss. Because of favorable weather conditions during the most recent growing season, the price for comparable apple juice in the region dropped to $1.10 per liter. Mary felt that the $1.50 price, if maintained throughout the current year, would be sufficient to make Bill's operation profitable-at last.
Required Is Mary's behavior regarding the cost information she provided to Susanna ethical Support your answer by reference to the Institute of Management Accountant's Statement of Ethical Professional Practice (www.imanet.org).
(CMA Adapted)
Required Is Mary's behavior regarding the cost information she provided to Susanna ethical Support your answer by reference to the Institute of Management Accountant's Statement of Ethical Professional Practice (www.imanet.org).
(CMA Adapted)
Standard Cost System and Direct Cost Variance:
A standard cost system is a tool for arranging financial plans, overseeing and controlling expenses, and assessing cost the board execution. A standard costing framework includes assessing the necessary expenses of a creation cycle.
Direct Cost Variance (DCV), is the distinction between the standard expense for real creation and the real expense underway. There are two sorts of work differences. Work Rate Variance is the distinction between the standard expense and the genuine cost paid for the real number of hours.
Discussion and analysis:
As regulator of the organization, behaviour of Mary isn't moral. Under the Credibility standard, Mary has a commitment to impart data reasonably and unbiasedly. Further, under the Credibility standard she has an obligation to plan total and clear reports and suggestions. That is, she should unveil the price data since this data could sensibly be relied upon to impact the owner's decision-making.
By purposefully distorting the obtaining cost of squeezed apple, Mary wants to help her friend's business, but to the expense of her manager, OAO, Inc. Under the Integrity standard, Mary should dodge this irreconcilable situation (individual faithfulness versus dependability to the organization for which she works) by: (a) not being the individual who sets the standard expense for the squeezed apple, and (b) not limiting wellspring of flexibly (e.g., by commanding that squeezed apple must be bought from her companion's business).
A standard cost system is a tool for arranging financial plans, overseeing and controlling expenses, and assessing cost the board execution. A standard costing framework includes assessing the necessary expenses of a creation cycle.
Direct Cost Variance (DCV), is the distinction between the standard expense for real creation and the real expense underway. There are two sorts of work differences. Work Rate Variance is the distinction between the standard expense and the genuine cost paid for the real number of hours.
Discussion and analysis:
As regulator of the organization, behaviour of Mary isn't moral. Under the Credibility standard, Mary has a commitment to impart data reasonably and unbiasedly. Further, under the Credibility standard she has an obligation to plan total and clear reports and suggestions. That is, she should unveil the price data since this data could sensibly be relied upon to impact the owner's decision-making.
By purposefully distorting the obtaining cost of squeezed apple, Mary wants to help her friend's business, but to the expense of her manager, OAO, Inc. Under the Integrity standard, Mary should dodge this irreconcilable situation (individual faithfulness versus dependability to the organization for which she works) by: (a) not being the individual who sets the standard expense for the squeezed apple, and (b) not limiting wellspring of flexibly (e.g., by commanding that squeezed apple must be bought from her companion's business).
4
Standard Costing; Variance Analysis; Strategic Considerations In a Wall Street Journal article, the author notes that various retailers in the United States (e.g., Meijer, Inc., Gap, Inc., Office Depot, Inc., and Toys "R" Us, Inc.) are turning to consulting firms, such as Accenture, to develop engineered labor standards for cashiers and other retail workers. Monitoring labor-hour consumption (i.e., labor efficiency) under such standards involves timing from the first scan of an item in a customer's purchase to the production of a sales receipt for the customer. A commentator for Meijer, Inc., states that the system now in use has enabled the company to more efficiently staff stores while concomitantly increasing customer-service ratings. A representative from another client of Accenture states that the new system allows the retailer to determine how many workers to schedule at a given time, resulting in a labor-cost reduction of approximately 8%. Engineered standards were developed many years ago in a manufacturing environment, at places such as Westinghouse, by time-and-motion study experts. Unlike factory workers, however, most retail clerks deal directly with customers. This raises interesting questions as to whether and how the use of such monitoring (i.e., control) systems affects customer relations, including customer satisfaction. Uncertainties associated with nonstandard transactions or events are also thought to have negative motivational effects on employees whose performance is assessed using such engineered standards. ( Source: Vanessa O'Connell, "Stores Count Seconds to Cut Labor Costs," The Wall Street Journal, November 13, 2008, pp. A1, A15. For additional information regarding "workforce-management systems," go to the website of Accenture, Ltd. (www.accenture.com/home.asp) and search under "Operations Workforce Optimization.")
Required
1. The article refers to the terms engineered labor standards and time-and-motion studies. Define each of these two terms.
2. Define the terms labor rate variance and labor efficiency variance. Which of these two variances is the basis for monitoring a cashier's performance, as described in the above-referenced article
3. What cashier activities might invalidate cashier time measures What recommendation(s) do you have for addressing this problem
4. As described in the chapter, any control/monitoring system is likely to have behavioral consequences. In the present context, what employee morale and customer-service problems might arise from using engineered standards for evaluating employees' time in completing tasks What steps do you think a retailer, such as those described in the article, can take to monitor this situation
5. How can information about cashier time-management be used strategically by a retailer For example, how can such information be used to lower labor costs for retail stores For which types of firms would such detailed information likely be of greater value
Required
1. The article refers to the terms engineered labor standards and time-and-motion studies. Define each of these two terms.
2. Define the terms labor rate variance and labor efficiency variance. Which of these two variances is the basis for monitoring a cashier's performance, as described in the above-referenced article
3. What cashier activities might invalidate cashier time measures What recommendation(s) do you have for addressing this problem
4. As described in the chapter, any control/monitoring system is likely to have behavioral consequences. In the present context, what employee morale and customer-service problems might arise from using engineered standards for evaluating employees' time in completing tasks What steps do you think a retailer, such as those described in the article, can take to monitor this situation
5. How can information about cashier time-management be used strategically by a retailer For example, how can such information be used to lower labor costs for retail stores For which types of firms would such detailed information likely be of greater value
فتح الحزمة
افتح القفل للوصول البطاقات البالغ عددها 54 في هذه المجموعة.
فتح الحزمة
k this deck
5
Explain what is meant by the term "management by exception." What is the relationship between the process of standard cost variance analysis and management by exception
فتح الحزمة
افتح القفل للوصول البطاقات البالغ عددها 54 في هذه المجموعة.
فتح الحزمة
k this deck
6
Refer to Exhibit 14.8 and the accompanying discussion in the text. Demonstrate that the purchase-price variance for PVC during October 2016 was $720U.
EXHIBIT 14.8 A Detailed Comparison of Actual Variable Costs and Flexible-Budget Variable Costs: Product XV-1 (October 2016 )
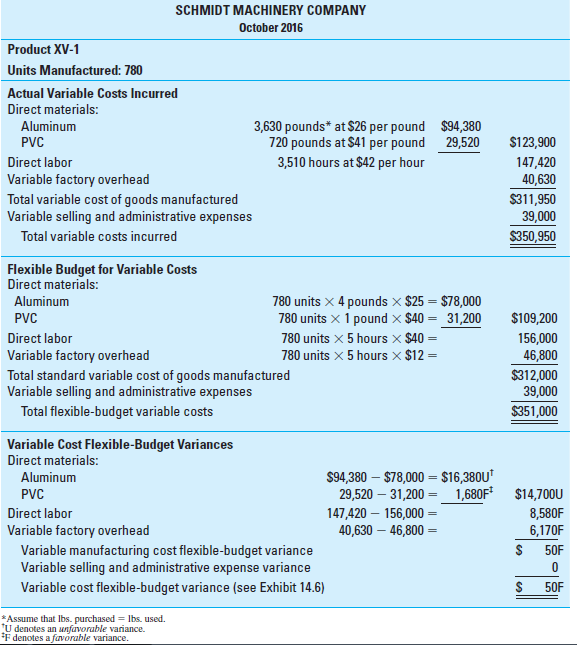
EXHIBIT 14.8 A Detailed Comparison of Actual Variable Costs and Flexible-Budget Variable Costs: Product XV-1 (October 2016 )
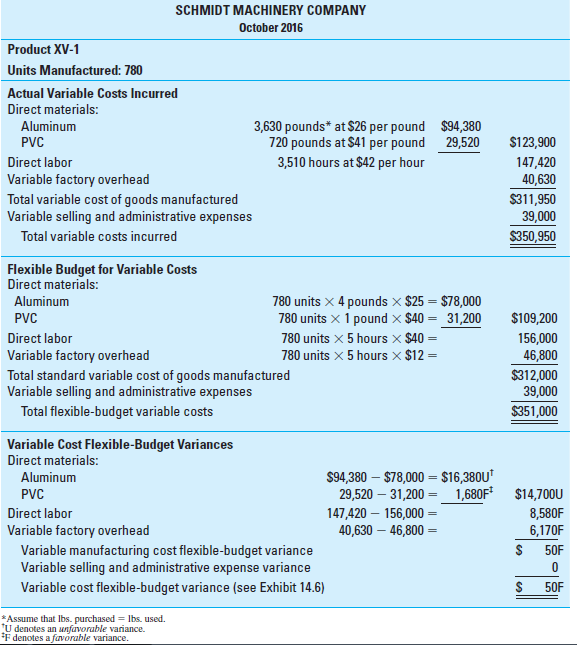
فتح الحزمة
افتح القفل للوصول البطاقات البالغ عددها 54 في هذه المجموعة.
فتح الحزمة
k this deck
7
Financial vs. Operational Control; Behavioral Considerations in the Standard-Setting Process You have been assigned to a strategic leadership committee that has been charged by the CEO with developing and implementing a comprehensive management accounting and control system. At the first planning session that you attended, the subject of financial control systems arose, but there was some uncertainty regarding the nature of such systems and some of the behavioral considerations that might have to be made in the design process. You have been asked by the chair of the committee to prepare a short written document that could be used as the basis of discussion at the next meeting. Specifically, you have been asked to: define and distinguish between operational control and financial control and how such systems relate to an organization's management accounting and control system; explain the theory behind the use of flexible budgets, standard costs, and variance analysis as elements of a financial control system; and provide input regarding how standards/budgets for performance evaluation should be set (i.e., whether authoritative standards, participative standards, or a consultative approach should be used in the standard-setting process). Compose your response as requested.
فتح الحزمة
افتح القفل للوصول البطاقات البالغ عددها 54 في هذه المجموعة.
فتح الحزمة
k this deck
8
Master Budgets; Flexible Budgets; Profit-Variance Analysis As part of its comprehensive planning and control system, Mopar Company uses a master budget and subsequent variance analysis. You are given the following information that pertains to the company's only product, XL-10, for the month of December.
Required
1. Using text Exhibit 14.4 as a guide, complete the missing parts of the following profit report for December.
2. Based on your completed profit report, determine the dollar amount and label (F or U) each of the following variances for December:
a. Total master (static) budget variance.
b. Total flexible-budget variance.
c. Sales volume variance, in terms of operating income.
d. Sales volume variance, in terms of contribution margin.
e. Selling price variance.
3. Explain what is meant by the labels "favorable" and "unfavorable" in terms of a profit-variance report of the type you just prepared for the Mopar Company.
4. What information is contained in the total flexible-budget variance for the period Include in your answer a short discussion of the component variances that can be calculated to explain the causes of the total flexible-budget variance.
5. Some individuals have recently criticized the use of standard costs and flexible budgets to perform the kinds of variance analyses covered in this chapter. Provide an overview of the arguments for and against the use of standard costs and flexible budgets for operational control purposes.
Exhibit 14.4 Breakdown of Total Operating Income Variance
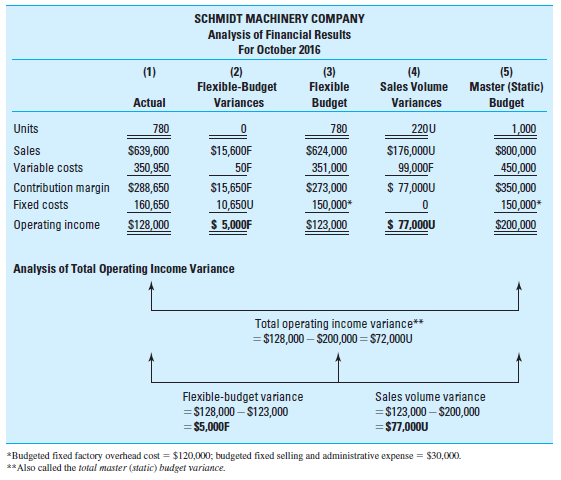
Required
1. Using text Exhibit 14.4 as a guide, complete the missing parts of the following profit report for December.
2. Based on your completed profit report, determine the dollar amount and label (F or U) each of the following variances for December:
a. Total master (static) budget variance.
b. Total flexible-budget variance.
c. Sales volume variance, in terms of operating income.
d. Sales volume variance, in terms of contribution margin.
e. Selling price variance.
3. Explain what is meant by the labels "favorable" and "unfavorable" in terms of a profit-variance report of the type you just prepared for the Mopar Company.
4. What information is contained in the total flexible-budget variance for the period Include in your answer a short discussion of the component variances that can be calculated to explain the causes of the total flexible-budget variance.
5. Some individuals have recently criticized the use of standard costs and flexible budgets to perform the kinds of variance analyses covered in this chapter. Provide an overview of the arguments for and against the use of standard costs and flexible budgets for operational control purposes.
Exhibit 14.4 Breakdown of Total Operating Income Variance
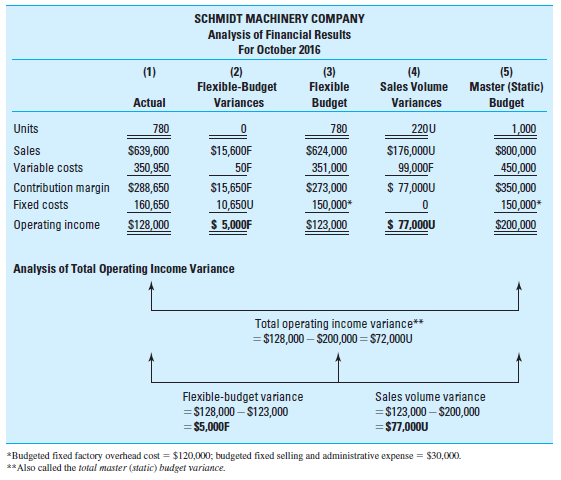
فتح الحزمة
افتح القفل للوصول البطاقات البالغ عددها 54 في هذه المجموعة.
فتح الحزمة
k this deck
9
Should the performance of a division be deemed less than satisfactory if all of its variances are "unfavorable" Explain.
فتح الحزمة
افتح القفل للوصول البطاقات البالغ عددها 54 في هذه المجموعة.
فتح الحزمة
k this deck
10
Refer to Exhibit 14.8 and the accompanying discussion in the text. Demonstrate that the flexible-budget variance for PVC during October 2016 was $1,680F.
Exhibit 14.8 A Detailed Comparison of Actual Variable Costs and Flexible-Budget Variable Costs: Product XV-1 (October 2016 )
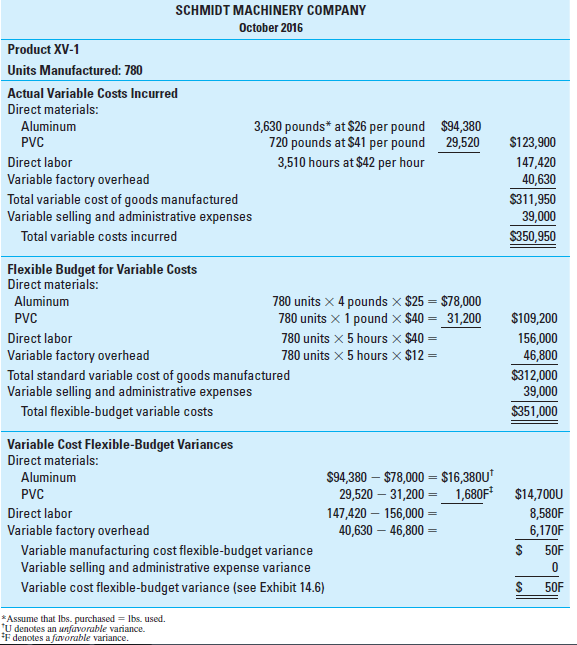
Exhibit 14.8 A Detailed Comparison of Actual Variable Costs and Flexible-Budget Variable Costs: Product XV-1 (October 2016 )
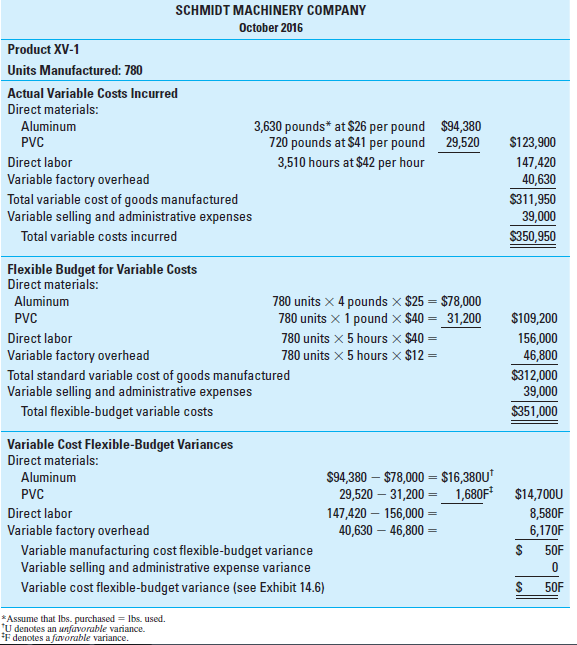
فتح الحزمة
افتح القفل للوصول البطاقات البالغ عددها 54 في هذه المجموعة.
فتح الحزمة
k this deck
11
Journal Entries Use the data in Exhibit 14.5. On October 7, Schmidt Machinery Company purchased 720 pounds of PVC at $41 per pound. On October 9, Schmidt's production department used 720 pounds of PVC for the 780 units of XV-1 it manufactured.
Required Make the necessary journal entries to record the purchase and usage of PVC during October.
EXHIBIT 14.5 Standard Cost Sheet, Product XV-1
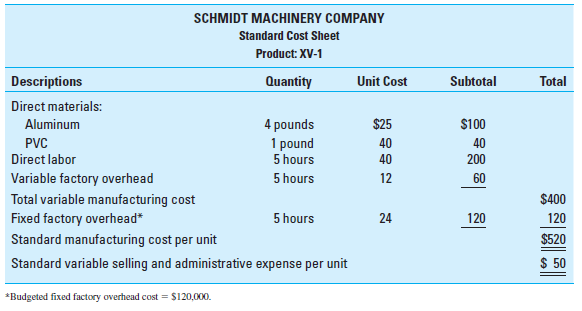
Required Make the necessary journal entries to record the purchase and usage of PVC during October.
EXHIBIT 14.5 Standard Cost Sheet, Product XV-1
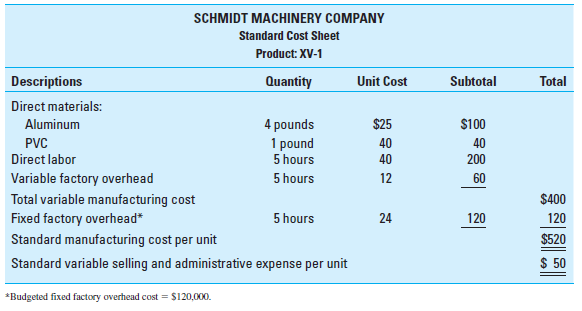
فتح الحزمة
افتح القفل للوصول البطاقات البالغ عددها 54 في هذه المجموعة.
فتح الحزمة
k this deck
12
Production Planning and Control Strategy This is a story about manufacturing performance at one plant of a large company. It begins with Kristen Reynolds, a relatively new plant manager, coming to visit Bryan Simpkins, the plant's head of manufacturing. Kristen and Bryan work for ITR Incorporated, a manufacturer of lighting fixtures with plants located in six countries and worldwide sales. The plant that Kristen and Bryan manage is located in Canada near Hamilton, Ontario. It is the one plant in ITR's system that focuses on custom orders that require special materials, setup, and assembly. The other five plants supply ITR's high-volume, standardized products. Because of changes in the residential and commercial construction industries, the demand for custom orders at the Ontario plant has been increasing steadily. Unfortunately, the plant has not been filling these orders as quickly as Kristen would like. Many solid customers are waiting days or weeks longer for their orders than they did a year ago; moreover, some ITR salespeople have begun to be evasive when customers ask how soon their orders can be filled. Kristen does not know how this is affecting sales or customer goodwill.
Bryan and Kristen first visit an operation where a skilled worker is operating a machine that molds a metal frame on which multiple light fixtures will later be installed. They watch as the worker (his name badge says Ed) completes the last of a batch of 15 frames. Kristen asks how long this batch took him, and he says 82 minutes. "I know this exactly because I have productivity standards to meet, and I must record my time on all jobs. My standard is 6 minutes per item, so I beat my goal." Ed then examines each frame and finds that one has a bad twist and must be rejected; this takes about 10 minutes. He then pushes a button near the machine that calls another worker to remove the defective frame. Meanwhile, Ed loads the 14 good ones on a cart and moves them to the next manufacturing station. Bryan and Kristen note that many frames are already waiting at the next station.
The worker who was called to remove the defective frame tags it, writes up the potential cause(s) for the defect, and then moves the frame to the area of the plant designated for scrap and rework. Kristen and Bryan look at the defect report and note that it indicates two possibilities, which will be studied further by another worker assigned to the scrap and rework area. The two possibilities are poor-quality materials, as determined by apparent weaknesses in portions of the framing material, and poor work quality (Ed could have damaged the frame accidentally by banging it against one of the roof support beams located next to his work area). Kristen and Bryan note that Ed's workstation area is indeed pretty cramped.
They move to another workstation, which has no operator. By asking a worker at the adjacent station, they determine that the station is down because the machine needs repair. "Joe usually works that station, but he is helping out in the shipping department until his machine is repaired."
They move to another workstation that looks very busy. An order marked "urgent" is waiting at this station, while Dan, the operator, quickly finishes another order. Bryan asks Dan why he has not started the urgent order, and Dan explains that he cannot afford to stop the machine and set it up for another order. This would cost him some time that would lower his productivity on the current job. Dan explains that it is important that he get the items done in the current order quickly, within a standard level of productivity, or production supervisors will be coming to call. Dan says he sees the urgent sign and is working quickly to get to it. He says he might even delay lunch to start it.
To investigate some of the things they observed, Kristen and Bryan next visit the purchasing department. Here they find that the frame material Ed used was purchased from a relatively new vendor at an unbelievably low price. The purchasing department manager approved the purchase because other purchases in the month had gone over budget and this was a way to help meet the budget. The budget is a predetermined amount that the purchasing department is expected to spend each month. Plant policy requires an investigation of any large variances from the budget.
Next, Kristen and Bryan inquire about Joe's machine. A check at the job scheduler's desk shows that the workstation had been in use constantly for the last few weeks. Joe said that he noticed a funny noise but had not reported it because he had some jobs to finish and his productivity was measured by how quickly he finished them. His time between jobs is not measured, but doing jobs quickly is important. Bryan asks the job scheduler why Ed's work area is so crowded since there appears to be plenty of room elsewhere in the plant. The job scheduler says that he is not sure, but that it probably has to do with the fact that each production department is charged a certain amount of plant overhead based on the amount of square feet of space that department occupies. Thus, the department manager for whom Ed works is likely to have reduced the space as much as possible to reduce these overhead charges.
As the story ends, Bryan and Kristen are looking for an answer to how urgent orders are scheduled and moved through the plant.
Required Consider the manufacturing processes observed in ITR's Ontario plant. What recommendations do you think Bryan and Kristen should make

Bryan and Kristen first visit an operation where a skilled worker is operating a machine that molds a metal frame on which multiple light fixtures will later be installed. They watch as the worker (his name badge says Ed) completes the last of a batch of 15 frames. Kristen asks how long this batch took him, and he says 82 minutes. "I know this exactly because I have productivity standards to meet, and I must record my time on all jobs. My standard is 6 minutes per item, so I beat my goal." Ed then examines each frame and finds that one has a bad twist and must be rejected; this takes about 10 minutes. He then pushes a button near the machine that calls another worker to remove the defective frame. Meanwhile, Ed loads the 14 good ones on a cart and moves them to the next manufacturing station. Bryan and Kristen note that many frames are already waiting at the next station.
The worker who was called to remove the defective frame tags it, writes up the potential cause(s) for the defect, and then moves the frame to the area of the plant designated for scrap and rework. Kristen and Bryan look at the defect report and note that it indicates two possibilities, which will be studied further by another worker assigned to the scrap and rework area. The two possibilities are poor-quality materials, as determined by apparent weaknesses in portions of the framing material, and poor work quality (Ed could have damaged the frame accidentally by banging it against one of the roof support beams located next to his work area). Kristen and Bryan note that Ed's workstation area is indeed pretty cramped.
They move to another workstation, which has no operator. By asking a worker at the adjacent station, they determine that the station is down because the machine needs repair. "Joe usually works that station, but he is helping out in the shipping department until his machine is repaired."
They move to another workstation that looks very busy. An order marked "urgent" is waiting at this station, while Dan, the operator, quickly finishes another order. Bryan asks Dan why he has not started the urgent order, and Dan explains that he cannot afford to stop the machine and set it up for another order. This would cost him some time that would lower his productivity on the current job. Dan explains that it is important that he get the items done in the current order quickly, within a standard level of productivity, or production supervisors will be coming to call. Dan says he sees the urgent sign and is working quickly to get to it. He says he might even delay lunch to start it.
To investigate some of the things they observed, Kristen and Bryan next visit the purchasing department. Here they find that the frame material Ed used was purchased from a relatively new vendor at an unbelievably low price. The purchasing department manager approved the purchase because other purchases in the month had gone over budget and this was a way to help meet the budget. The budget is a predetermined amount that the purchasing department is expected to spend each month. Plant policy requires an investigation of any large variances from the budget.
Next, Kristen and Bryan inquire about Joe's machine. A check at the job scheduler's desk shows that the workstation had been in use constantly for the last few weeks. Joe said that he noticed a funny noise but had not reported it because he had some jobs to finish and his productivity was measured by how quickly he finished them. His time between jobs is not measured, but doing jobs quickly is important. Bryan asks the job scheduler why Ed's work area is so crowded since there appears to be plenty of room elsewhere in the plant. The job scheduler says that he is not sure, but that it probably has to do with the fact that each production department is charged a certain amount of plant overhead based on the amount of square feet of space that department occupies. Thus, the department manager for whom Ed works is likely to have reduced the space as much as possible to reduce these overhead charges.
As the story ends, Bryan and Kristen are looking for an answer to how urgent orders are scheduled and moved through the plant.
Required Consider the manufacturing processes observed in ITR's Ontario plant. What recommendations do you think Bryan and Kristen should make
فتح الحزمة
افتح القفل للوصول البطاقات البالغ عددها 54 في هذه المجموعة.
فتح الحزمة
k this deck
13
Explain the possible causes for direct materials price and direct materials usage variances. Who in the organization normally has influence over or responsibility for each of these variances
فتح الحزمة
افتح القفل للوصول البطاقات البالغ عددها 54 في هذه المجموعة.
فتح الحزمة
k this deck
14
Mom's Apple Pie Company uses a standard cost system. The standard direct labor time for each pie is 10 minutes. During the most recent month, the company produced and sold 6,000 pies. The standard direct labor rate is $8 per hour; the actual labor rate per hour for the month was $8.40. The company used a total of 980 labor hours. What was the direct labor efficiency (usage) variance for the month (Show calculations.)
فتح الحزمة
افتح القفل للوصول البطاقات البالغ عددها 54 في هذه المجموعة.
فتح الحزمة
k this deck
15
Journal Entries in a Standard Cost System Boron Chemical Company produces a synthetic resin that is used in the automotive industry. The company uses a standard cost system. For each gallon of output, the following direct manufacturing costs are anticipated:
During December of the current year, Boron produced a total of 2,500 gallons of output and incurred the following direct manufacturing costs:
Boron records price variances for materials at the time of purchase.
Required Prepare journal entries for the following events and transactions:
1. Purchase, on credit, of direct materials.
2. Direct materials issued to production.
3. Direct labor cost of units completed this period.
4. Direct manufacturing cost (direct labor plus direct materials) of units completed and transferred to Finished Goods Inventory.
5. Sale, for $150 per gallon, of 2,000 gallons of output. ( Hint: You will need two journal entries here.)

During December of the current year, Boron produced a total of 2,500 gallons of output and incurred the following direct manufacturing costs:

Boron records price variances for materials at the time of purchase.
Required Prepare journal entries for the following events and transactions:
1. Purchase, on credit, of direct materials.
2. Direct materials issued to production.
3. Direct labor cost of units completed this period.
4. Direct manufacturing cost (direct labor plus direct materials) of units completed and transferred to Finished Goods Inventory.
5. Sale, for $150 per gallon, of 2,000 gallons of output. ( Hint: You will need two journal entries here.)
فتح الحزمة
افتح القفل للوصول البطاقات البالغ عددها 54 في هذه المجموعة.
فتح الحزمة
k this deck
16
Research Assignment: Service-Based Innovation; Strategy Obtain from your library (or course pack, as appropriate) a copy of the following article: L. McCreary, "Kaiser Permanente's Innovation on the Front Lines," Harvard Business Review, September 2010, pp. 92-97. One usually thinks of "innovation" in terms of new technologies or new products. This article focuses on a different type of innovation: service-based innovation. In a larger sense, it deals with the issue of improving health care delivery.
Required After reading the above-referenced article, answer the following questions:
1. In general, how does this article relate to the material covered in Chapter 14
2. Describe the Innovation Consultancy and its role in the larger organization, Kaiser Permanente (KP).
3. Provide a brief description of the "human-centered design" methodology employed by the Innovation Consultancy arm of KP.
4. Discuss four concrete examples of improvements in health care delivery (innovations in service-based practice) resulting from the method described in requirement 3 above.
Required After reading the above-referenced article, answer the following questions:
1. In general, how does this article relate to the material covered in Chapter 14
2. Describe the Innovation Consultancy and its role in the larger organization, Kaiser Permanente (KP).
3. Provide a brief description of the "human-centered design" methodology employed by the Innovation Consultancy arm of KP.
4. Discuss four concrete examples of improvements in health care delivery (innovations in service-based practice) resulting from the method described in requirement 3 above.
فتح الحزمة
افتح القفل للوصول البطاقات البالغ عددها 54 في هذه المجموعة.
فتح الحزمة
k this deck
17
Explain some of the possible causes of direct labor rate (price) and direct labor efficiency (quantity) variances. Who normally has responsibility for or influence over each of these variances
فتح الحزمة
افتح القفل للوصول البطاقات البالغ عددها 54 في هذه المجموعة.
فتح الحزمة
k this deck
18
Refer to the data in Brief Exercise 14-21. What was the direct labor rate (price) variance for the month (Show calculations.)
فتح الحزمة
افتح القفل للوصول البطاقات البالغ عددها 54 في هذه المجموعة.
فتح الحزمة
k this deck
19
Direct Materials Variances-Journal Entries Steinberg Company had the following direct materials costs for the manufacturing of product T in March:
Required
1. What was Steinberg's direct materials purchase-price variance and its direct materials usage variance for March (Show calculations.)
2. Prepare the appropriate journal entries for March.
Required

1. What was Steinberg's direct materials purchase-price variance and its direct materials usage variance for March (Show calculations.)
2. Prepare the appropriate journal entries for March.
فتح الحزمة
افتح القفل للوصول البطاقات البالغ عددها 54 في هذه المجموعة.
فتح الحزمة
k this deck
20
Research Assignment: Supply-Chain Management; Strategy Obtain from your library (or course pack, as appropriate) a copy of the following article: S. New, "The Transparent Supply Chain," Harvard Business Review, October 2010, pp. 76-82.
Required After reading the above-referenced article, answer the following questions:
1. In general, how does this article relate to the material covered in Chapter 14
2. What is meant by the term "provenance," as used in this article According to the article, what is motivating the need for businesses to provide greater transparency of their supply chains
3. Provide several examples of leading-edge technology that can be used by businesses to provide consumers and other stakeholders information regarding a product's provenance.
Required After reading the above-referenced article, answer the following questions:
1. In general, how does this article relate to the material covered in Chapter 14
2. What is meant by the term "provenance," as used in this article According to the article, what is motivating the need for businesses to provide greater transparency of their supply chains
3. Provide several examples of leading-edge technology that can be used by businesses to provide consumers and other stakeholders information regarding a product's provenance.
فتح الحزمة
افتح القفل للوصول البطاقات البالغ عددها 54 في هذه المجموعة.
فتح الحزمة
k this deck
21
Will overtime premiums affect direct labor variances If so, which ones
فتح الحزمة
افتح القفل للوصول البطاقات البالغ عددها 54 في هذه المجموعة.
فتح الحزمة
k this deck
22
Flexible Budgets and Operating-Income Variance Analysis; Spreadsheet Application The following information is available for Brownstone Products Company for the month of July:
Required
1. Set up a spreadsheet to compute the July sales volume variance and the flexible-budget variance for the month in terms of both contribution margin and operating income.
2. Discuss implications of these variances on strategic cost management for Brownstone.
3. Configure your spreadsheet so that it will allow the firm to prepare pro forma budgets for activities within its relevant range of operations. Use your spreadsheet to prepare a flexible budget for each of the following two output levels:
a. 3,750 units.
b. 4,150 units.
(CMA Adapted)
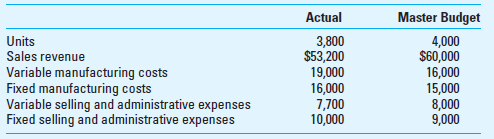
Required
1. Set up a spreadsheet to compute the July sales volume variance and the flexible-budget variance for the month in terms of both contribution margin and operating income.
2. Discuss implications of these variances on strategic cost management for Brownstone.
3. Configure your spreadsheet so that it will allow the firm to prepare pro forma budgets for activities within its relevant range of operations. Use your spreadsheet to prepare a flexible budget for each of the following two output levels:
a. 3,750 units.
b. 4,150 units.
(CMA Adapted)
فتح الحزمة
افتح القفل للوصول البطاقات البالغ عددها 54 في هذه المجموعة.
فتح الحزمة
k this deck
23
Financial vs. Nonfinancial Performance Indicators for Operational Control As indicated in the text, both financial and nonfinancial performance indicators play important roles in an organization's overall operational control system. Explain, concisely, the relative advantage of each type of performance indicator. That is, what role would each type of performance indicator play in helping to ensure that operations are in control ( Hint: Think about this issue both from the standpoint of managers and from the standpoint of operating personnel.)
فتح الحزمة
افتح القفل للوصول البطاقات البالغ عددها 54 في هذه المجموعة.
فتح الحزمة
k this deck
24
Which of the following should a firm use as the standard in assessing production efficiencies: standards based on ideal performance, standards based on attainable performance, or standards based on the average of recent historical performance Explain.
فتح الحزمة
افتح القفل للوصول البطاقات البالغ عددها 54 في هذه المجموعة.
فتح الحزمة
k this deck
25
Master (Static) Budget Variance and Components As the new accountant for Cohen Co., you have been asked to provide a succinct analysis of financial performance for the year just ended. You obtain the following information that pertains to the company's sole product:
Required
1. What was the actual operating income for the period Show calculations.
2. What was the company's master budget operating income for the period Show calculations.
3. What was the total master (static) budget variance, in terms of operating income, for the period Is this variance favorable (F) or unfavorable (U) Why
4. From the information given earlier, are you able to decompose the total master (static) budget variance into a total flexible-budget variance and a sales volume variance Why or why not
5. Define the meaning of the total flexible-budget variance and the sales volume variance.

Required
1. What was the actual operating income for the period Show calculations.
2. What was the company's master budget operating income for the period Show calculations.
3. What was the total master (static) budget variance, in terms of operating income, for the period Is this variance favorable (F) or unfavorable (U) Why
4. From the information given earlier, are you able to decompose the total master (static) budget variance into a total flexible-budget variance and a sales volume variance Why or why not
5. Define the meaning of the total flexible-budget variance and the sales volume variance.
فتح الحزمة
افتح القفل للوصول البطاقات البالغ عددها 54 في هذه المجموعة.
فتح الحزمة
k this deck
26
Behavioral and Strategic Considerations Chen, Inc., produces a line of soy-based products, including a premium soy milk that comes in different flavors. This company, founded by Alan Chen, has been doing business in the United States for the past 15 years. In the face of competition associated with recent entrants into this line of business, the controller of the company, Rosita Chang, implemented a standard cost system to better control costs of the soy milk product line. Financial reports for tracking performance are issued monthly, and any unfavorable cost variances are investigated by management.
Recently, the production manager of the soy milk line complained to Chang that the standards were unrealistic, that they have a negative impact on motivation (because the system focuses only on unfavorable variances), and that, because of global forces of supply and demand, they quickly become out of date. The production manager noted that his recent switch to a newly available homogenizing agent resulted in higher material-acquisition costs but decreased labor hours to produce the soy milk. These two changes, when combined, had a negligible effect on manufacturing cost per unit. However, the monthly performance reports continued to show a favorable labor variance (despite evidence that the workers were slowing down or slacking off a bit) and an unfavorable materials variance.
Required
1. Describe several ways that a standard cost system could improve (i.e., strengthen) an overall management control system.
2. Give at least two reasons how a standard cost system could have a negative impact on employee motivation.
3. Explain strategic issues regarding the decision to adopt a standard costing system, particularly in light of competitive forces confronting this company. ( Hint: Think in terms of the costs and benefits associated with the use of standard costs as part of a comprehensive management accounting and control system.)
(CMA Adapted)
Recently, the production manager of the soy milk line complained to Chang that the standards were unrealistic, that they have a negative impact on motivation (because the system focuses only on unfavorable variances), and that, because of global forces of supply and demand, they quickly become out of date. The production manager noted that his recent switch to a newly available homogenizing agent resulted in higher material-acquisition costs but decreased labor hours to produce the soy milk. These two changes, when combined, had a negligible effect on manufacturing cost per unit. However, the monthly performance reports continued to show a favorable labor variance (despite evidence that the workers were slowing down or slacking off a bit) and an unfavorable materials variance.
Required
1. Describe several ways that a standard cost system could improve (i.e., strengthen) an overall management control system.
2. Give at least two reasons how a standard cost system could have a negative impact on employee motivation.
3. Explain strategic issues regarding the decision to adopt a standard costing system, particularly in light of competitive forces confronting this company. ( Hint: Think in terms of the costs and benefits associated with the use of standard costs as part of a comprehensive management accounting and control system.)
(CMA Adapted)
فتح الحزمة
افتح القفل للوصول البطاقات البالغ عددها 54 في هذه المجموعة.
فتح الحزمة
k this deck
27
Discuss behavioral concerns in establishing and implementing a standard cost system.
فتح الحزمة
افتح القفل للوصول البطاقات البالغ عددها 54 في هذه المجموعة.
فتح الحزمة
k this deck
28
Flexible Budget and Operating Income Variances Assume that in June Schmidt Machinery Company (Exhibit 14.1) manufactured and sold 950 units for $835 each. During this month the company incurred $475,000 total variable expenses and $180,000 total fixed expenses.
Required for the Month of June:
1. Prepare a flexible budget for the production and sale of 950 units.
2. Compute for June:
a. The sales volume variance, in terms of operating income.
b. The sales volume variance, in terms of contribution margin.
3. Calculate for June:
a. The total flexible-budget (FB) variance.
b. The total variable cost flexible-budget variance.
c. The total fixed cost flexible-budget (FB) variance.
d. The selling price variance.
EXHIBIT 14.1 Comparison of Actual and Budgeted Operating Income
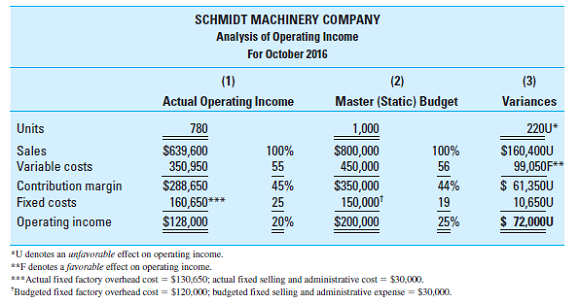
Required for the Month of June:
1. Prepare a flexible budget for the production and sale of 950 units.
2. Compute for June:
a. The sales volume variance, in terms of operating income.
b. The sales volume variance, in terms of contribution margin.
3. Calculate for June:
a. The total flexible-budget (FB) variance.
b. The total variable cost flexible-budget variance.
c. The total fixed cost flexible-budget (FB) variance.
d. The selling price variance.
EXHIBIT 14.1 Comparison of Actual and Budgeted Operating Income
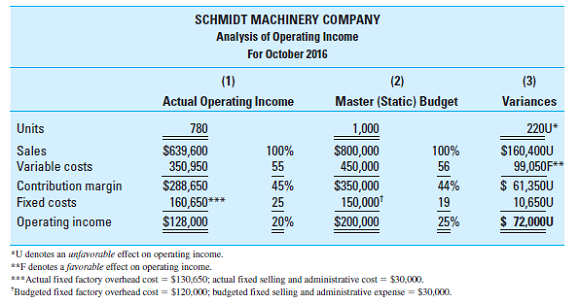
فتح الحزمة
افتح القفل للوصول البطاقات البالغ عددها 54 في هذه المجموعة.
فتح الحزمة
k this deck
29
Control of Operating Processes; Nonfinancial Performance Indicators This chapter deals with the design of effective control systems associated with business, including operating processes. As indicated in the text, a comprehensive management accounting and control system will have both financial indicators and nonfinancial performance indicators. Financial indicators can include the operating-income variances that can be calculated each period by using standard costs and flexible budgets. This question deals with the use of nonfinancial performance indicators as a complement to the financial-performance indicators that are useful for controlling operating processes.
Required
1. List and define the primary business processes in which organizations engage in their attempt to meet customer expectations.
2. Fundamentally, control systems (including management accounting and control systems) collect information regarding the extent to which specified objectives are being accomplished. For each of the operating processes identified in (1), provide a listing of possible objectives that the organization might pursue. For each listed objective, provide one or more relevant nonfinancial performance indicators (performance metrics) that the organization's management accounting and control system might collect and report to management.
Required
1. List and define the primary business processes in which organizations engage in their attempt to meet customer expectations.
2. Fundamentally, control systems (including management accounting and control systems) collect information regarding the extent to which specified objectives are being accomplished. For each of the operating processes identified in (1), provide a listing of possible objectives that the organization might pursue. For each listed objective, provide one or more relevant nonfinancial performance indicators (performance metrics) that the organization's management accounting and control system might collect and report to management.
فتح الحزمة
افتح القفل للوصول البطاقات البالغ عددها 54 في هذه المجموعة.
فتح الحزمة
k this deck
30
This chapter deals with control systems associated with business processes, such as operating processes. Provide a definition and some examples of operating processes. In what other processes would an organization engage in the normal course of business
فتح الحزمة
افتح القفل للوصول البطاقات البالغ عددها 54 في هذه المجموعة.
فتح الحزمة
k this deck
31
Direct Materials and Direct Labor Variances Schmidt Machinery Company (Exhibit 14.5) used 3,450 pounds of aluminum in June to manufacture 920 units. The company paid $28.50 per pound during the month to purchase aluminum. On June 1, the company had 50 pounds of aluminum on hand. At the end of June, the company had only 30 pounds of aluminum in its warehouse. Schmidt used 4,200 direct labor hours in June, at an average cost of $41.50 per hour.
Required Compute for June:
1. Schmidt's purchase-price and usage variances for aluminum.
2. Schmidt's direct labor rate and efficiency variances.
EXHIBIT 14.5 Standard Cost Sheet, Product XV-1
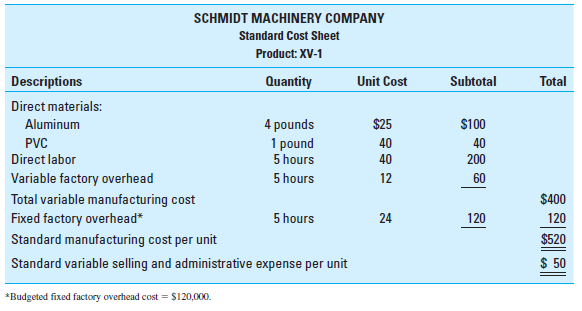
Required Compute for June:
1. Schmidt's purchase-price and usage variances for aluminum.
2. Schmidt's direct labor rate and efficiency variances.
EXHIBIT 14.5 Standard Cost Sheet, Product XV-1
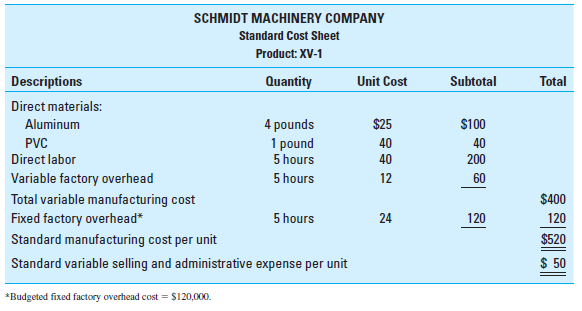
فتح الحزمة
افتح القفل للوصول البطاقات البالغ عددها 54 في هذه المجموعة.
فتح الحزمة
k this deck
32
JIT and Process Cycle Efficiency (PCE) Zodiac Sound Co. manufactures audio systems, both made-to-order and more mass-produced systems that are typically sold to large-scale manufacturers of electronics equipment. For competitive reasons, the company is trying to increase its processing cycle efficiency (PCE) measure. As a strategy for improving its PCE performance, the company is considering a switch to JIT manufacturing. While the company managers have a fairly good feel for the cost of implementing JIT, they are unsure about the benefits of such a move, both in financial and nonfinancial terms. To help inform the ultimate decision regarding a move to a JIT system, you've been asked to provide some input. Fortunately, you've recently attended a continuing professional education (CPE) workshop on the costs and benefits of moving to JIT and therefore feel comfortable responding to management's request.
Required
1. Define the terms value-added time, non-value-added time, and process cycle efficiency (PCE). Conceptually, how are activities included in the first two categories determined (That is, how does one know what activities are considered "value-added" )
2. Define the terms cycle time and processing (manufacturing) time. How can processing time be broken down further
3. Given the estimated data below, calculate and interpret the PCE for both the current manufacturing process and the proposed process after implementing JIT:
4. What is the percentage change in average PCE anticipated under JIT
5. What additional nonfinancial performance indicators might management monitor in conjunction with the move to JIT
Required
1. Define the terms value-added time, non-value-added time, and process cycle efficiency (PCE). Conceptually, how are activities included in the first two categories determined (That is, how does one know what activities are considered "value-added" )
2. Define the terms cycle time and processing (manufacturing) time. How can processing time be broken down further
3. Given the estimated data below, calculate and interpret the PCE for both the current manufacturing process and the proposed process after implementing JIT:
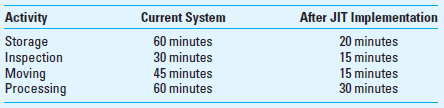
4. What is the percentage change in average PCE anticipated under JIT
5. What additional nonfinancial performance indicators might management monitor in conjunction with the move to JIT
فتح الحزمة
افتح القفل للوصول البطاقات البالغ عددها 54 في هذه المجموعة.
فتح الحزمة
k this deck
33
Describe how a just-in-time (JIT) manufacturing system is fundamentally different from a conventional manufacturing system. List two primary financial benefits associated with a shift to JIT manufacturing. What effect does the adoption of JIT have on the design of management accounting and control systems
فتح الحزمة
افتح القفل للوصول البطاقات البالغ عددها 54 في هذه المجموعة.
فتح الحزمة
k this deck
34
Standard Labor Rate and Labor Efficiency Variance Information regarding Maxwell's direct labor cost for the month of January follows:
Required Compute the following (show calculations):
1. Standard direct labor wage rate per hour in January.
2. Direct labor efficiency variance.

Required Compute the following (show calculations):
1. Standard direct labor wage rate per hour in January.
2. Direct labor efficiency variance.
فتح الحزمة
افتح القفل للوصول البطاقات البالغ عددها 54 في هذه المجموعة.
فتح الحزمة
k this deck
35
Master Budget, Flexible Budget, and Profit-Variance Analysis; Spreadsheet Application Going into the period just ended, Ortiz Co., manufacturer of a moderately priced espresso maker for retail sale, had planned to produce and sell 3,900 units at $100 per unit. Budgeted variable manufacturing costs per unit are $50. Ortiz pays its salespeople a 10% sales commission, which is the only variable nonmanufacturing cost for the company. Fixed costs are budgeted as follows: manufacturing, $50,000, marketing, $36,000.
Actual financial results for the period were disappointing. While sales volume was up (4,000 units sold), actual operating profit was only $20,000 for the period. Fixed manufacturing costs were as budgeted, but fixed marketing expenses exceeded budget by $4,000. Actual sales revenue for the period was $390,000, and actual variable costs were $70 per unit (the actual sales commission was 10% of sales revenue generated).
Required
1. Develop an Excel spreadsheet that is able to produce a profit-variance report similar to the one presented in text Exhibit 14.4.
2. Use the spreadsheet you developed in (1) and the data presented above to complete the profit-variance report for the period. Below the table you create, show separately the following variances:
a. Total master (static) budget variance (i.e., the total operating-income variance for the period).
b. Total flexible-budget variance.
c. Flexible-budget variance for total variable costs, plus the flexible-budget variance for:
(1) Variable manufacturing costs.
(2) Variable nonmanufacturing costs.
d. Flexible-budget variance for total fixed costs, plus the flexible-budget variance for:
(1) Fixed manufacturing costs.
(2) Fixed nonmanufacturing costs.
3. Provide a concise interpretation for each of the variances calculated above in (2).
4. Using the variances you calculated above in (2) and, in as much detail as the data allow, prepare a separate summary report similar to text Exhibit 14.2.
EXHIBIT 14.4 Breakdown of Total Operating Income Variance
EXHIBIT 14.2 Operating-Income Variances (Single-Product Example: Product XV-1)
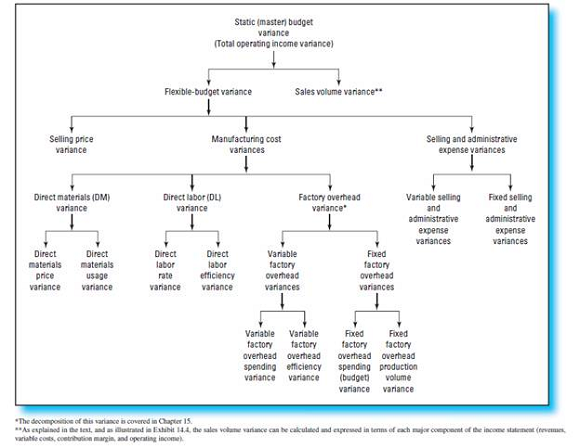
Actual financial results for the period were disappointing. While sales volume was up (4,000 units sold), actual operating profit was only $20,000 for the period. Fixed manufacturing costs were as budgeted, but fixed marketing expenses exceeded budget by $4,000. Actual sales revenue for the period was $390,000, and actual variable costs were $70 per unit (the actual sales commission was 10% of sales revenue generated).
Required
1. Develop an Excel spreadsheet that is able to produce a profit-variance report similar to the one presented in text Exhibit 14.4.
2. Use the spreadsheet you developed in (1) and the data presented above to complete the profit-variance report for the period. Below the table you create, show separately the following variances:
a. Total master (static) budget variance (i.e., the total operating-income variance for the period).
b. Total flexible-budget variance.
c. Flexible-budget variance for total variable costs, plus the flexible-budget variance for:
(1) Variable manufacturing costs.
(2) Variable nonmanufacturing costs.
d. Flexible-budget variance for total fixed costs, plus the flexible-budget variance for:
(1) Fixed manufacturing costs.
(2) Fixed nonmanufacturing costs.
3. Provide a concise interpretation for each of the variances calculated above in (2).
4. Using the variances you calculated above in (2) and, in as much detail as the data allow, prepare a separate summary report similar to text Exhibit 14.2.
EXHIBIT 14.4 Breakdown of Total Operating Income Variance
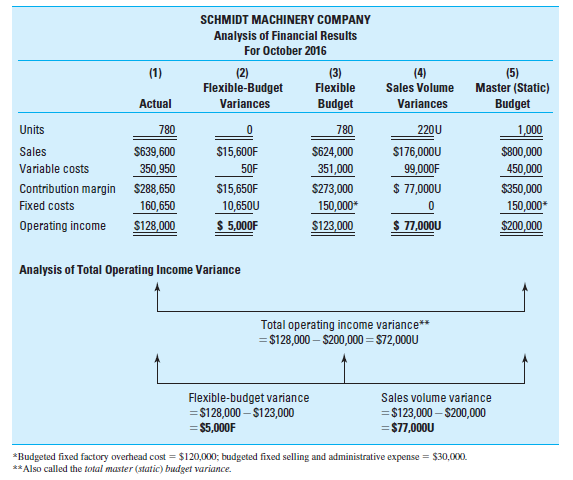
EXHIBIT 14.2 Operating-Income Variances (Single-Product Example: Product XV-1)
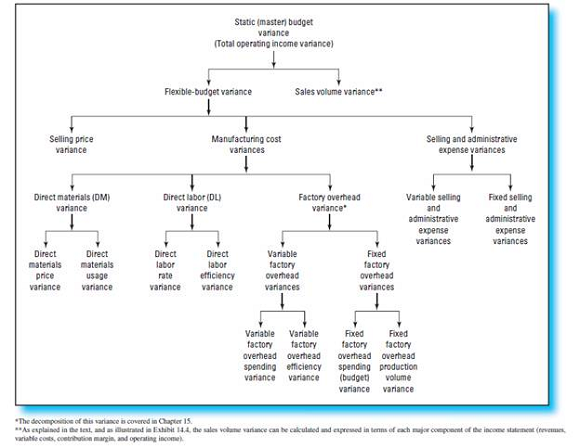
فتح الحزمة
افتح القفل للوصول البطاقات البالغ عددها 54 في هذه المجموعة.
فتح الحزمة
k this deck
36
One of the purported benefits of moving to a JIT system is improvements in customer-response time (CRT). Define the following terms: total customer-response time; manufacturing (production) cycle time; cycle-time efficiency; value-added time; and non-value-added time.
فتح الحزمة
افتح القفل للوصول البطاقات البالغ عددها 54 في هذه المجموعة.
فتح الحزمة
k this deck
37
Generating a Flexible Budget; Spreadsheet Application Crane Corporation's master (static) budget for the year is shown below:
Required
1. During the year the company manufactured and sold 55,000 units of product. Prepare an Excel spreadsheet that contains a flexible budget for this level of output.
2. Now suppose, that the actual level of output was 65,000 units. Rerun your spreadsheet to generate a flexible budget for this level of output.
3. Of what relevance is the notion of "relevant range" when preparing pro forma budgets or a flexible budget for control purposes
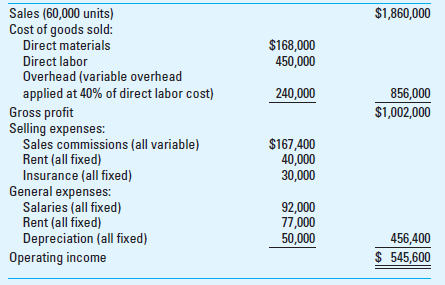
Required
1. During the year the company manufactured and sold 55,000 units of product. Prepare an Excel spreadsheet that contains a flexible budget for this level of output.
2. Now suppose, that the actual level of output was 65,000 units. Rerun your spreadsheet to generate a flexible budget for this level of output.
3. Of what relevance is the notion of "relevant range" when preparing pro forma budgets or a flexible budget for control purposes
فتح الحزمة
افتح القفل للوصول البطاقات البالغ عددها 54 في هذه المجموعة.
فتح الحزمة
k this deck
38
Materials Purchase-Price Variance and Foreign Exchange Rates Jonas Materials Science (JMS) purchases its materials from several countries. As part of its cost-control program, JMS uses a standard cost system for all aspects of its operations including materials purchases. The company establishes standard costs for materials at the beginning of each fiscal year.
Pat Butch, the purchasing manager, is happy with the result of the year just ended. He believes that the purchase-price variance for the year will be favorable and is very confident that his department has at least met the standard prices. The preliminary report from the controller's office confirms his jubilation. Following is a portion of the preliminary report:
In the fourth quarter, the purchasing department increased purchases from the budgeted normal volume of 5,000 to 25,000 kilograms to meet the increased demands, which was a result of the firm's unexpected success in a fiercely competitive bidding. The substantial increase in the volume to be purchased forced the purchasing department to search for alternative suppliers. After frantic searches, it found suppliers in several foreign countries that could meet the firm's needs and could provide materials with higher quality than that of JMS's regular supplier. The purchasing department was very reluctant to make the purchase because the negotiated price was $77 per kilogram, including shipping and import duty. However, this original reluctance disappeared upon learning that the actual cost of the purchases would be much lower than expected due to currency devaluations (the result of financial turmoil in several of the countries in the region).
Patricia Rice, the controller, does not share the purchasing department's euphoria. She is fully aware of the following quarterly purchases:
Required
1. Calculate purchase-price variances for the fourth quarter and for the year. How much of the price variance is attributable to changes in foreign currency exchange rates
2. Evaluate the purchasing department's performance.
Pat Butch, the purchasing manager, is happy with the result of the year just ended. He believes that the purchase-price variance for the year will be favorable and is very confident that his department has at least met the standard prices. The preliminary report from the controller's office confirms his jubilation. Following is a portion of the preliminary report:
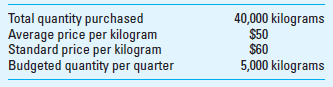
In the fourth quarter, the purchasing department increased purchases from the budgeted normal volume of 5,000 to 25,000 kilograms to meet the increased demands, which was a result of the firm's unexpected success in a fiercely competitive bidding. The substantial increase in the volume to be purchased forced the purchasing department to search for alternative suppliers. After frantic searches, it found suppliers in several foreign countries that could meet the firm's needs and could provide materials with higher quality than that of JMS's regular supplier. The purchasing department was very reluctant to make the purchase because the negotiated price was $77 per kilogram, including shipping and import duty. However, this original reluctance disappeared upon learning that the actual cost of the purchases would be much lower than expected due to currency devaluations (the result of financial turmoil in several of the countries in the region).
Patricia Rice, the controller, does not share the purchasing department's euphoria. She is fully aware of the following quarterly purchases:

Required
1. Calculate purchase-price variances for the fourth quarter and for the year. How much of the price variance is attributable to changes in foreign currency exchange rates
2. Evaluate the purchasing department's performance.
فتح الحزمة
افتح القفل للوصول البطاقات البالغ عددها 54 في هذه المجموعة.
فتح الحزمة
k this deck
39
The Baldwin Company, in its master budget for 2016, predicted total sales of $160,000, variable costs of $48,000, and fixed costs of $52,000 ($24,000 manufacturing and $28,000 nonmanufacturing). Actual sales revenue for 2016 turned out to be $180,000. Actual costs were as follows: variable, $54,000, and fixed, $50,000. What was the total static budget (operating-income) variance for 2016 Was this total variance favorable (F) or unfavorable (U)
فتح الحزمة
افتح القفل للوصول البطاقات البالغ عددها 54 في هذه المجموعة.
فتح الحزمة
k this deck
40
Behavioral Considerations and Continuous-Improvement Standards At a recent seminar you attended, the invited speaker was discussing some of the advantages and disadvantages of standard costs in terms of evaluating performance and motivating goal-congruent behavior on the part of employees. One criticism of standard costs in particular caught your attention: The use of conventional standard costs may not provide appropriate incentives for improvements needed to compete effectively with world-class organizations. The speaker then discussed so-called "continuous-improvement standard costs." Such standards embody systematically lower costs over time. For example, on a monthly basis, it might be appropriate to budget a 1% reduction in per-unit direct labor cost.
Assume that the standard wage rate into the foreseeable future is $30 per hour. Assume, too, that the budgeted labor hour standard for October of the current year is 1.50 hours and that this standard is reduced each month by 1%. During December of the current year the company produced 10,000 units of XL-10, using 14,800 direct labor hours. The actual wage rate per hour in December was $32.00.
Required
1. Prepare a table that contains the standard labor-hour requirement per unit and standard direct labor cost per unit for the four months, October through January. Note: Carry the labor hour requirement per unit to five decimal places and the standard labor costs per unit to two decimal places.
2. Compute the direct labor efficiency variance for December. (Show calculations.)
3. What behavioral considerations apply to the decision to use continuous-improvement standards
Assume that the standard wage rate into the foreseeable future is $30 per hour. Assume, too, that the budgeted labor hour standard for October of the current year is 1.50 hours and that this standard is reduced each month by 1%. During December of the current year the company produced 10,000 units of XL-10, using 14,800 direct labor hours. The actual wage rate per hour in December was $32.00.
Required
1. Prepare a table that contains the standard labor-hour requirement per unit and standard direct labor cost per unit for the four months, October through January. Note: Carry the labor hour requirement per unit to five decimal places and the standard labor costs per unit to two decimal places.
2. Compute the direct labor efficiency variance for December. (Show calculations.)
3. What behavioral considerations apply to the decision to use continuous-improvement standards
فتح الحزمة
افتح القفل للوصول البطاقات البالغ عددها 54 في هذه المجموعة.
فتح الحزمة
k this deck
41
Joint Direct Materials Variance Acme Mfg. produces corrugated board containers that the nearby wine industry uses to package wine in bulk. Acme buys kraft paper by the ton, converts it to heavy-duty paperboard on its corrugator, and then cuts and glues it into folding boxes. The boxes are opened and filled with a plastic liner and then with the wine.
Many other corrugated board converters are in the area and competition is strong. Acme is eager to keep its costs under control. The company has used a standard cost system for several years. Responsibility for variances has been established. For example, the purchasing agent is responsible for the direct materials price variance, and the general supervisor answers for the direct materials usage variance.
Recently, the industrial engineer and the company's management accountant participated in a workshop sponsored by the Institute of Management Accountants (IMA) at which there was some discussion of variance analysis. They noted that the workshop proposed that the responsibility for some variances was properly dual. The accountant and engineer reviewed Acme's system and were not sure how to adapt the new information to it.
Acme has the following standards for its direct materials:
During May, the accountant assembled the following data about direct materials:
Required Determine the following for Acme:
1. Direct materials price variance, calculated at point of production.
2. Direct materials efficiency (usage) variance.
3. Direct materials joint price-quantity variance (defined as: [AP - SP] × [AQ - SQ]).
(CMA Adapted)
Many other corrugated board converters are in the area and competition is strong. Acme is eager to keep its costs under control. The company has used a standard cost system for several years. Responsibility for variances has been established. For example, the purchasing agent is responsible for the direct materials price variance, and the general supervisor answers for the direct materials usage variance.
Recently, the industrial engineer and the company's management accountant participated in a workshop sponsored by the Institute of Management Accountants (IMA) at which there was some discussion of variance analysis. They noted that the workshop proposed that the responsibility for some variances was properly dual. The accountant and engineer reviewed Acme's system and were not sure how to adapt the new information to it.
Acme has the following standards for its direct materials:
![Joint Direct Materials Variance Acme Mfg. produces corrugated board containers that the nearby wine industry uses to package wine in bulk. Acme buys kraft paper by the ton, converts it to heavy-duty paperboard on its corrugator, and then cuts and glues it into folding boxes. The boxes are opened and filled with a plastic liner and then with the wine. Many other corrugated board converters are in the area and competition is strong. Acme is eager to keep its costs under control. The company has used a standard cost system for several years. Responsibility for variances has been established. For example, the purchasing agent is responsible for the direct materials price variance, and the general supervisor answers for the direct materials usage variance. Recently, the industrial engineer and the company's management accountant participated in a workshop sponsored by the Institute of Management Accountants (IMA) at which there was some discussion of variance analysis. They noted that the workshop proposed that the responsibility for some variances was properly dual. The accountant and engineer reviewed Acme's system and were not sure how to adapt the new information to it. Acme has the following standards for its direct materials: During May, the accountant assembled the following data about direct materials: Required Determine the following for Acme: 1. Direct materials price variance, calculated at point of production. 2. Direct materials efficiency (usage) variance. 3. Direct materials joint price-quantity variance (defined as: [AP - SP] × [AQ - SQ]). (CMA Adapted)](https://d2lvgg3v3hfg70.cloudfront.net/SM1607/11eb9774_187f_5374_a72e_79ef6e7c14d8_SM1607_00.jpg)
During May, the accountant assembled the following data about direct materials:
![Joint Direct Materials Variance Acme Mfg. produces corrugated board containers that the nearby wine industry uses to package wine in bulk. Acme buys kraft paper by the ton, converts it to heavy-duty paperboard on its corrugator, and then cuts and glues it into folding boxes. The boxes are opened and filled with a plastic liner and then with the wine. Many other corrugated board converters are in the area and competition is strong. Acme is eager to keep its costs under control. The company has used a standard cost system for several years. Responsibility for variances has been established. For example, the purchasing agent is responsible for the direct materials price variance, and the general supervisor answers for the direct materials usage variance. Recently, the industrial engineer and the company's management accountant participated in a workshop sponsored by the Institute of Management Accountants (IMA) at which there was some discussion of variance analysis. They noted that the workshop proposed that the responsibility for some variances was properly dual. The accountant and engineer reviewed Acme's system and were not sure how to adapt the new information to it. Acme has the following standards for its direct materials: During May, the accountant assembled the following data about direct materials: Required Determine the following for Acme: 1. Direct materials price variance, calculated at point of production. 2. Direct materials efficiency (usage) variance. 3. Direct materials joint price-quantity variance (defined as: [AP - SP] × [AQ - SQ]). (CMA Adapted)](https://d2lvgg3v3hfg70.cloudfront.net/SM1607/11eb9774_187f_7a85_a72e_2f5c2008b776_SM1607_00.jpg)
Required Determine the following for Acme:
1. Direct materials price variance, calculated at point of production.
2. Direct materials efficiency (usage) variance.
3. Direct materials joint price-quantity variance (defined as: [AP - SP] × [AQ - SQ]).
(CMA Adapted)
فتح الحزمة
افتح القفل للوصول البطاقات البالغ عددها 54 في هذه المجموعة.
فتح الحزمة
k this deck
42
Edwards and Bell market a single line of home computer, dubbed the XL-98. The master budget for the coming year contained the following items: sales revenue, $400,000; variable costs, $250,000; fixed costs, $100,000. Actual results for the year were as follows: sales revenue, $350,000; variable costs, $225,000; fixed costs, $95,000. The flexible-budget operating income for the year was $35,000. What is the total static (master) budget variance in operating profit for the period What portion of the total static (master) budget variance is attributable to actual sales volume being different from planned sales volume What portion is due to a combination of selling price and costs (variable cost per unit and total fixed costs) being different from budgeted amounts
فتح الحزمة
افتح القفل للوصول البطاقات البالغ عددها 54 في هذه المجموعة.
فتح الحزمة
k this deck
43
Flexible Budget and Operating-Income Variances RTI Company's master budget calls for production and sale of 18,000 units for $81,000; variable costs of $30,600; and fixed costs of $20,000. During the most recent period, the company incurred $32,000 of variable costs to produce and sell 20,000 units for $85,000. During this same period, the company earned $25,000 of operating income.
Required
1. Determine the following for RTI Company:
a. Flexible-budget operating income.
b. Flexible-budget variance, in terms of contribution margin.
c. Flexible-budget variance, in terms of operating income.
d. Sales volume variance, in terms of contribution margin.
e. Sales volume variance, in terms of operating income.
2. Explain why the contribution margin sales volume variance and the operating income sales volume variance for the same period are likely to be identical.
3. Explain why the contribution margin flexible-budget variance is likely to differ from the operating income flexible-budget variance for the same period.
Required
1. Determine the following for RTI Company:
a. Flexible-budget operating income.
b. Flexible-budget variance, in terms of contribution margin.
c. Flexible-budget variance, in terms of operating income.
d. Sales volume variance, in terms of contribution margin.
e. Sales volume variance, in terms of operating income.
2. Explain why the contribution margin sales volume variance and the operating income sales volume variance for the same period are likely to be identical.
3. Explain why the contribution margin flexible-budget variance is likely to differ from the operating income flexible-budget variance for the same period.
فتح الحزمة
افتح القفل للوصول البطاقات البالغ عددها 54 في هذه المجموعة.
فتح الحزمة
k this deck
44
Standard Cost Sheet and Use of Variance Data Tastyfreeze Company is a small producer of fruit-flavored frozen desserts. For many years, its products have had strong regional sales because of brand recognition; however, other companies have begun marketing similar products in the area, and price competition has become increasingly important. Dan O'Mara, the company's controller, is planning to implement a standard cost system for Tastyfreeze and has gathered considerable information from his co-workers about production and materials requirements for Tastyfreeze's products. Dan believes that the use of standard costs will allow the company to improve cost control, make better pricing decisions, and enhance strategic management.
Tastyfreeze's most popular product is raspberry sherbet. The sherbet is produced in 10-gallon batches, each of which requires 6 quarts of good raspberries and 10 gallons of other ingredients. The fresh raspberries are sorted by hand before they enter the production process. Because of imperfections in the raspberries and normal spoilage, one quart of berries is discarded for every four accepted. The standard direct labor time for sorting to obtain one quart of acceptable raspberries is 4 minutes. The acceptable raspberries are then blended with the other ingredients; blending requires 12 minutes of direct labor time per batch. After blending, the sherbet is packaged in quart containers. Dan has gathered the following price information:
• Tastyfreeze purchases raspberries for $5.00 per quart. All other ingredients cost $2.50 per gallon.
• Direct labor is paid at the rate of $16 per hour.
• The total packaging cost (labor and materials) for the sherbet is $0.75 per quart.
Required
1. Develop the standard cost for the direct cost components of a 10-gallon batch of raspberry sherbet. For each direct cost component, the standard cost should identify the following:
a. Standard quantity.
b. Standard rate (or price).
c. Standard cost per batch.
2. As part of the implementation of a standard cost system at Tastyfreeze, Dan plans to train those responsible for maintaining the standards to use variance analysis. He is particularly concerned with the causes of unfavorable variances.
a. Discuss the possible causes of unfavorable materials price variances, identify the individuals who should be held responsible for them, and comment on the implications of these variances on strategic cost management.
b. Discuss the possible causes of unfavorable labor efficiency variances, identify the individuals who should be held responsible for them, and comment on the implications of these variances on strategic cost management.
(CMA Adapted)
Tastyfreeze's most popular product is raspberry sherbet. The sherbet is produced in 10-gallon batches, each of which requires 6 quarts of good raspberries and 10 gallons of other ingredients. The fresh raspberries are sorted by hand before they enter the production process. Because of imperfections in the raspberries and normal spoilage, one quart of berries is discarded for every four accepted. The standard direct labor time for sorting to obtain one quart of acceptable raspberries is 4 minutes. The acceptable raspberries are then blended with the other ingredients; blending requires 12 minutes of direct labor time per batch. After blending, the sherbet is packaged in quart containers. Dan has gathered the following price information:
• Tastyfreeze purchases raspberries for $5.00 per quart. All other ingredients cost $2.50 per gallon.
• Direct labor is paid at the rate of $16 per hour.
• The total packaging cost (labor and materials) for the sherbet is $0.75 per quart.
Required
1. Develop the standard cost for the direct cost components of a 10-gallon batch of raspberry sherbet. For each direct cost component, the standard cost should identify the following:
a. Standard quantity.
b. Standard rate (or price).
c. Standard cost per batch.
2. As part of the implementation of a standard cost system at Tastyfreeze, Dan plans to train those responsible for maintaining the standards to use variance analysis. He is particularly concerned with the causes of unfavorable variances.
a. Discuss the possible causes of unfavorable materials price variances, identify the individuals who should be held responsible for them, and comment on the implications of these variances on strategic cost management.
b. Discuss the possible causes of unfavorable labor efficiency variances, identify the individuals who should be held responsible for them, and comment on the implications of these variances on strategic cost management.
(CMA Adapted)
فتح الحزمة
افتح القفل للوصول البطاقات البالغ عددها 54 في هذه المجموعة.
فتح الحزمة
k this deck
45
The Ace Company sells a single product at a budgeted selling price per unit of $20. Budgeted fixed manufacturing costs for the coming period are $10,000, while budgeted fixed marketing expenses for the period are $24,000. Budgeted variable costs per unit include $2 of selling expenses (commission) and $4 of manufacturing costs. What is the budgeted operating income if the anticipated sales volume for the period is (a) 10,000 units, and (b) 15,000 units
فتح الحزمة
افتح القفل للوصول البطاقات البالغ عددها 54 في هذه المجموعة.
فتح الحزمة
k this deck
46
Applicability of Standard Cost Systems Portfolio management is a powerful concept in finance and marketing. The marketing application of the concept is to develop and manage a balanced portfolio of products. Market share and market growth can be used to classify products for portfolio purposes, and the product classifications often are extended to the organizational units that make the product. The market share/growth classifications can be depicted as follows:
The question mark is the classification for products that show high growth rates but have small market shares, such as new products that are similar to their competitors. A rising star is a high-growth, high-market-share product that tends to mature into a cash cow. A cash cow is a slow-growing established product that can be milked for cash to help the question mark and introduce new products. The dog is a low-growth, low-market-share item that is a candidate for elimination or segmentation. Understanding where a product falls within this market share/growth structure is important when applying a standard cost system.
Required
1. Discuss the major advantages of using a standard cost accounting system.
2. Describe the types of information that are useful in setting standards and the conditions that must be present to support the use of standard costing.
3. Discuss the applicability or nonapplicability of using standard costing for a product classified as (a) a cash cow, and (b) a question mark.
4. What are some primary criticisms of using standard cost systems in today's manufacturing environment
(CMA Adapted)
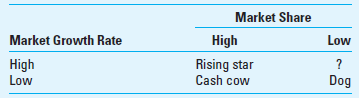
The question mark is the classification for products that show high growth rates but have small market shares, such as new products that are similar to their competitors. A rising star is a high-growth, high-market-share product that tends to mature into a cash cow. A cash cow is a slow-growing established product that can be milked for cash to help the question mark and introduce new products. The dog is a low-growth, low-market-share item that is a candidate for elimination or segmentation. Understanding where a product falls within this market share/growth structure is important when applying a standard cost system.
Required
1. Discuss the major advantages of using a standard cost accounting system.
2. Describe the types of information that are useful in setting standards and the conditions that must be present to support the use of standard costing.
3. Discuss the applicability or nonapplicability of using standard costing for a product classified as (a) a cash cow, and (b) a question mark.
4. What are some primary criticisms of using standard cost systems in today's manufacturing environment
(CMA Adapted)
فتح الحزمة
افتح القفل للوصول البطاقات البالغ عددها 54 في هذه المجموعة.
فتح الحزمة
k this deck
47
Standard Cost System-Behavioral Considerations Mark-Wright Inc. (MWI) is a specialty frozen food processor located in the midwestern states. Since its founding in 1982, MWI has enjoyed a loyal local clientele willing to pay premium prices for the high-quality frozen foods prepared from special recipes. In the last two years, MWI has experienced rapid sales growth in its operating region and has had many inquiries about supplying its products on a national basis. To meet this growth, MWI expanded its processing capabilities, which resulted in increased production and distribution costs. Furthermore, MWI has been encountering pricing pressure from competitors outside its normal marketing region.
Because MWI desires to continue its expansion, Jim Condon, CEO, has engaged a consulting firm to assist the company in determining its best course of action. The consulting firm concluded that, although premium pricing is sustainable in some areas, MWI must make some price concessions if sales growth is to be achieved. Also, to maintain profit margins, the company must reduce and control its costs. The consulting firm recommended using a standard cost system that would facilitate a flexible budgeting system to better accommodate the changes in demand that can be expected when serving an expanding market area.
Jim met with his management team and explained the consulting firm's recommendations. He then assigned the team the task of establishing standard costs. After discussing the situation with their respective staffs, the management team met to review the matter.
Jane Morgan, purchasing manager, noted that meeting expanded production would necessitate obtaining basic food supplies from sources other than MWI's traditional ones. This would entail increased raw materials and shipping costs and could result in supplies of lower quality. Consequently, the processing department would have to make up these increased costs if current cost levels are to be maintained or reduced.
Alan Chen, processing manager, countered that the need to accelerate processing cycles to increase production, coupled with the possibility of receiving lower-grade supplies, could result in a slip in quality and a higher product rejection rate. Under these circumstances, per-unit labor utilization cannot be maintained or reduced, and forecasting future unit labor content becomes very difficult.
Tina Lopez, production engineer, advised that failure to properly maintain and thoroughly clean the equipment at prescribed daily intervals could affect the quality and unique taste of the frozen food products. Jack Reid, vice president of sales, stated that if quality could not be maintained, MWI could not expect to increase sales to the levels projected.
When the management team reported these problems to Jim, he said that if agreement could not be reached on appropriate standards, he would arrange to have the consulting firm set the standards, and everyone would have to live with the results.
Required
1. With respect to a standard cost system, list:
a. Its major advantages.
b. Its disadvantages.
2. Identify those who should participate in setting standards and describe the benefits of their participation.
3. Explain the general features and characteristics associated with the introduction and operation of a standard cost system that make it an effective tool for cost control.
4. What could the consequences be if Jim Condon, CEO, has the outside consulting firm set MWI's standards
(CMA Adapted)
Because MWI desires to continue its expansion, Jim Condon, CEO, has engaged a consulting firm to assist the company in determining its best course of action. The consulting firm concluded that, although premium pricing is sustainable in some areas, MWI must make some price concessions if sales growth is to be achieved. Also, to maintain profit margins, the company must reduce and control its costs. The consulting firm recommended using a standard cost system that would facilitate a flexible budgeting system to better accommodate the changes in demand that can be expected when serving an expanding market area.
Jim met with his management team and explained the consulting firm's recommendations. He then assigned the team the task of establishing standard costs. After discussing the situation with their respective staffs, the management team met to review the matter.
Jane Morgan, purchasing manager, noted that meeting expanded production would necessitate obtaining basic food supplies from sources other than MWI's traditional ones. This would entail increased raw materials and shipping costs and could result in supplies of lower quality. Consequently, the processing department would have to make up these increased costs if current cost levels are to be maintained or reduced.
Alan Chen, processing manager, countered that the need to accelerate processing cycles to increase production, coupled with the possibility of receiving lower-grade supplies, could result in a slip in quality and a higher product rejection rate. Under these circumstances, per-unit labor utilization cannot be maintained or reduced, and forecasting future unit labor content becomes very difficult.
Tina Lopez, production engineer, advised that failure to properly maintain and thoroughly clean the equipment at prescribed daily intervals could affect the quality and unique taste of the frozen food products. Jack Reid, vice president of sales, stated that if quality could not be maintained, MWI could not expect to increase sales to the levels projected.
When the management team reported these problems to Jim, he said that if agreement could not be reached on appropriate standards, he would arrange to have the consulting firm set the standards, and everyone would have to live with the results.
Required
1. With respect to a standard cost system, list:
a. Its major advantages.
b. Its disadvantages.
2. Identify those who should participate in setting standards and describe the benefits of their participation.
3. Explain the general features and characteristics associated with the introduction and operation of a standard cost system that make it an effective tool for cost control.
4. What could the consequences be if Jim Condon, CEO, has the outside consulting firm set MWI's standards
(CMA Adapted)
فتح الحزمة
افتح القفل للوصول البطاقات البالغ عددها 54 في هذه المجموعة.
فتح الحزمة
k this deck
48
Davidson Corp. produces a single product: fireproof safety deposit boxes for home use. The budget going into the current year anticipated a selling price of $55 per unit. Because of competitive pressures, the company had to cut selling prices by 10% during the year. Budgeted variable costs per unit are $32, and budgeted total fixed costs are $156,000 for the year. Anticipated sales volume for the year was 10,000 units. Actual sales volume was 5% less than budget. What was the sales price variance for the year Label this variance F (favorable) or U (unfavorable), as appropriate.
فتح الحزمة
افتح القفل للوصول البطاقات البالغ عددها 54 في هذه المجموعة.
فتح الحزمة
k this deck
49
Determining Standard Direct Materials Cost Agrichem manufactures Insect-Be-Gone. Each bag of the product contains 60 pounds of direct materials. Twenty-five percent of the materials evaporate during manufacturing. The budget allows the direct materials to be purchased at $2.50 a pound under terms of 2/10, n/30. The company's stated policy is to take all available cash discounts. Determine the standard direct materials cost for one bag of Insect-Be-Gone.
فتح الحزمة
افتح القفل للوصول البطاقات البالغ عددها 54 في هذه المجموعة.
فتح الحزمة
k this deck
50
Standard Cost in Process Costing; All Variances and Journal Entries Dash Company adopted a standard costing system several years ago. The standard costs for the prime costs (i.e., direct materials and direct labor) of its single product are:
All materials are added at the beginning of processing. The following data were taken from the company's records for November:
Required
1. Compute for November (show calculations):
a. The labor efficiency variance.
b. The labor rate variance.
c. The actual number of kilograms of material used in the production process during the month.
d. The actual price paid per kilogram of material during the month.
e. The amount of direct material cost and direct labor cost transferred to the Finished Goods account.
f. The total amount of direct material and direct labor cost in the Work-in-Process Inventory account at the end of the month.
2. Prepare journal entries to record all transactions, including the variances in requirement 1.
(CMA Adapted)

All materials are added at the beginning of processing. The following data were taken from the company's records for November:
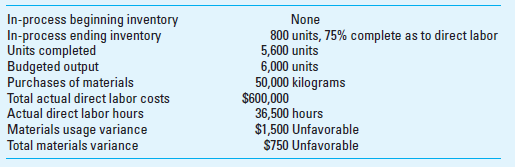
Required
1. Compute for November (show calculations):
a. The labor efficiency variance.
b. The labor rate variance.
c. The actual number of kilograms of material used in the production process during the month.
d. The actual price paid per kilogram of material during the month.
e. The amount of direct material cost and direct labor cost transferred to the Finished Goods account.
f. The total amount of direct material and direct labor cost in the Work-in-Process Inventory account at the end of the month.
2. Prepare journal entries to record all transactions, including the variances in requirement 1.
(CMA Adapted)
فتح الحزمة
افتح القفل للوصول البطاقات البالغ عددها 54 في هذه المجموعة.
فتح الحزمة
k this deck
51
What is the difference between a master budget, pro forma budgets, and a flexible budget
فتح الحزمة
افتح القفل للوصول البطاقات البالغ عددها 54 في هذه المجموعة.
فتح الحزمة
k this deck
52
Chapman, Inc., sells a single product, Zud, which has a budgeted selling price of $24 per unit and a budgeted variable cost of $12 per unit. Budgeted fixed costs for the year amount to $45,000. Actual sales volume for the year (47,000) fell 3,000 units short of budgeted sales volume. Actual fixed costs were $46,000. With everything else held constant, what impact did the shortfall in volume have on profitability for the year
فتح الحزمة
افتح القفل للوصول البطاقات البالغ عددها 54 في هذه المجموعة.
فتح الحزمة
k this deck
53
Ethical Considerations A number of ethical issues arise in the design of management control systems. For example, such issues might arise when an individual's performance relative to budget or standard cost affects the individual's compensation or reward. Assume you are the cost accountant for a manufacturing firm. The reward system at your firm is such that the purchasing manager earns a financial reward when a significant favorable materials purchase-price variance is realized. Suppose, too, that this manager has an opportunity to get an extremely low price on raw materials that the manager knows are of substandard quality. Finally, assume that the purchasing manager believes that any problems attributable to the low-grade materials are not likely to surface until the product from which these materials is made has been in use for a while by consumers.
Required
1. Access the IMA's Statement of Ethical Professional Practice (www.imanet.org). Which, if any, of the IMA standards contained in the statement are at issue in this case, from the standpoint of the purchasing manager and/or the cost accountant
2. Assume you are the cost accountant at the manufacturing plant where the preceding scenario takes place. According to the IMA's Statement of Ethical Professional Practice, what are your obligations in this situation
Required
1. Access the IMA's Statement of Ethical Professional Practice (www.imanet.org). Which, if any, of the IMA standards contained in the statement are at issue in this case, from the standpoint of the purchasing manager and/or the cost accountant
2. Assume you are the cost accountant at the manufacturing plant where the preceding scenario takes place. According to the IMA's Statement of Ethical Professional Practice, what are your obligations in this situation
فتح الحزمة
افتح القفل للوصول البطاقات البالغ عددها 54 في هذه المجموعة.
فتح الحزمة
k this deck
54
Flexible Budget and Operating-Profit Variances Phoenix Management helps rental property owners find renters and charges the owners one-half of the first month's rent for this service. For August 2016, Phoenix expects to find renters for 100 apartments with an average first month's rent of $700. Budgeted cost data per tenant application for 2016 follow:
• Professional labor: 1.5 hours at $20 per hour
• Credit checks: $50
Phoenix expects other costs, including lease payment for the building, secretarial help, and utilities, to be $3,000 per month. On average, Phoenix is successful in placing one tenant for every three applicants.
Actual rental applications in August 2016 were 270. Phoenix paid $9,500 for 400 hours of professional labor. Credit checks went up to $55 per application. Other support costs in August 2016 were $3,600. The average first monthly rentals for August 2016 were $800 per apartment unit for 90 units.
Required
1. Prepare a profit-variance report similar to text Exhibit 14.4. Compute the total flexible-budget variance and the sales volume variance for Phoenix's operations in August 2016.
2. Determine the professional labor rate and labor efficiency variances for August 2016.
3. What nonfinancial factors should Phoenix consider in evaluating the effectiveness and efficiency of professional labor
EXHIBIT 14.4 Breakdown of Total Operating Income Variance
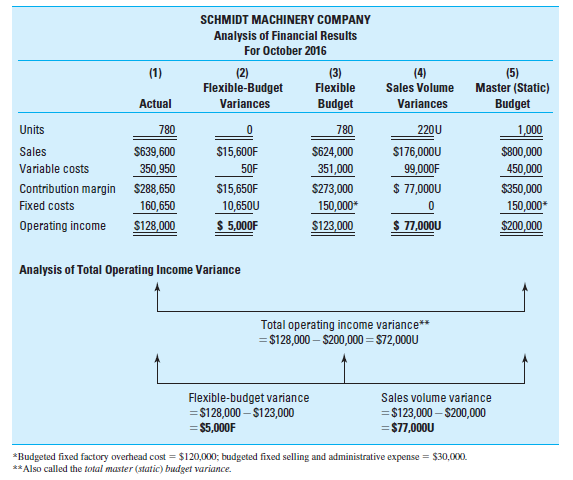
• Professional labor: 1.5 hours at $20 per hour
• Credit checks: $50
Phoenix expects other costs, including lease payment for the building, secretarial help, and utilities, to be $3,000 per month. On average, Phoenix is successful in placing one tenant for every three applicants.
Actual rental applications in August 2016 were 270. Phoenix paid $9,500 for 400 hours of professional labor. Credit checks went up to $55 per application. Other support costs in August 2016 were $3,600. The average first monthly rentals for August 2016 were $800 per apartment unit for 90 units.
Required
1. Prepare a profit-variance report similar to text Exhibit 14.4. Compute the total flexible-budget variance and the sales volume variance for Phoenix's operations in August 2016.
2. Determine the professional labor rate and labor efficiency variances for August 2016.
3. What nonfinancial factors should Phoenix consider in evaluating the effectiveness and efficiency of professional labor
EXHIBIT 14.4 Breakdown of Total Operating Income Variance
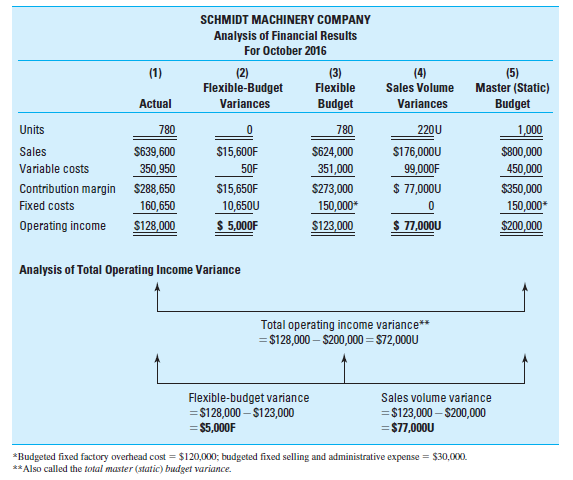
فتح الحزمة
افتح القفل للوصول البطاقات البالغ عددها 54 في هذه المجموعة.
فتح الحزمة
k this deck