Deck 11: Criticisms of Absorption Cost Systems: Inaccurate Product Costs
سؤال
سؤال
سؤال
سؤال
سؤال
سؤال
سؤال
سؤال
سؤال
سؤال
سؤال
سؤال
سؤال
سؤال
سؤال
سؤال
سؤال
فتح الحزمة
قم بالتسجيل لفتح البطاقات في هذه المجموعة!
Unlock Deck
Unlock Deck
1/19
العب
ملء الشاشة (f)
Deck 11: Criticisms of Absorption Cost Systems: Inaccurate Product Costs
1
ABC Systems Can Still Produce Inaccurate Product Costs
Accurate Cost Manufacturing, Inc., manufactures and sells large business equipment for the office and business markets. The primary function of Manufacturing is to provide components and subassemblies for the profit centers within the company. To maintain competitiveness, each profit center can purchase parts either from Manufacturing or from outside firms. Manufacturing operates as a cost center and charges the profit centers for the full cost of the parts. Costs are computed once a year using full absorption costing. The volume of parts used to calculate costs is provided by the profit centers to Manufacturing in August; the fiscal year begins in January. With these numbers, Manufacturing projects costs per part for the year. These cost estimates are then used throughout the year to charge the profit centers. Any over/under-absorbed overhead goes directly to the bottom line of the company, not to any of the profit centers.
Within Manufacturing there is a department called finishing. The finishing department provides a service to other Manufacturing departments and profit centers as well as generating some external sales. Types of finishing include painting and plating. The facility has large investments in fixed assets in both automation and environmental compliance for finishing. The finishing operation believes it provides value to customers through its high quality and its close location to the manufacturing departments.
During the past year, the profit centers have begun taking work away from Manufacturing and giving it to outside vendors with lower quoted costs. Manufacturing then has lower volumes and has to raise the prices on the products it is producing, causing the profit centers to send even more work out. Manufacturing feels it is caught in a death spiral.
The death spiral situation has affected finishing the most. The finishing department is currently operating at 30 percent of capacity and has facilities that are too large for the low volume of work. Table 1 summarizes the data pertaining to finishing. Fixed costs make up 71 percent of the current cost structure. Other manufacturing departments are beginning to tell finishing that they will be sending their work out to get plating and painting so as not to lose any work because of the high internal cost of finishing.
Finishing is trying to attract business from outside Accurate Cost Manufacturing. The external sales guidelines require a 35 percent profit margin applied to the full cost for all external work. With the current low level of work and high fixed costs, finishing cannot attract external sales due to cost.
In an effort to gain control of the true cost drivers of the business, the manager of the finishing operation has implemented activity-based costing. Tables 2 and 3 project the cost for products and volumes for one plating operation. The problem that the finishing manager now faces is that the manufacturing departments are about to send the 12-inch and 18-inch work to an outside shop due to lower costs.
In implementing activity-based costing, the manager thinks he has truly identified the proper system. The larger parts tend to run in smaller lot sizes and generate more paperwork. Smaller parts tend to be run in larger lot sizes and generate less paperwork.
In a recent meeting with the management of the manufacturing department and profit centers, it was stated that the installation of activity-based costing is in direct conflict with the change in the mix of work from small parts to large parts and the need to run smaller lot sizes. The manufacturing department and profit centers would like to pursue just-in-time manufacturing and further reduce the lot sizes for both small and large parts. During this meeting, the profit centers and manufacturing departments said the implementation of activity-based costing would force them to move their work out of the finishing department to outside shops.
Required:
a. Analyze the current situation in this company. What should be done?
b. Compare and comment on the costs before and after ABC is implemented.
c. Has finishing management made a mistake by installing activity-based costing?
Accurate Cost Manufacturing, Inc., manufactures and sells large business equipment for the office and business markets. The primary function of Manufacturing is to provide components and subassemblies for the profit centers within the company. To maintain competitiveness, each profit center can purchase parts either from Manufacturing or from outside firms. Manufacturing operates as a cost center and charges the profit centers for the full cost of the parts. Costs are computed once a year using full absorption costing. The volume of parts used to calculate costs is provided by the profit centers to Manufacturing in August; the fiscal year begins in January. With these numbers, Manufacturing projects costs per part for the year. These cost estimates are then used throughout the year to charge the profit centers. Any over/under-absorbed overhead goes directly to the bottom line of the company, not to any of the profit centers.
Within Manufacturing there is a department called finishing. The finishing department provides a service to other Manufacturing departments and profit centers as well as generating some external sales. Types of finishing include painting and plating. The facility has large investments in fixed assets in both automation and environmental compliance for finishing. The finishing operation believes it provides value to customers through its high quality and its close location to the manufacturing departments.
During the past year, the profit centers have begun taking work away from Manufacturing and giving it to outside vendors with lower quoted costs. Manufacturing then has lower volumes and has to raise the prices on the products it is producing, causing the profit centers to send even more work out. Manufacturing feels it is caught in a death spiral.
The death spiral situation has affected finishing the most. The finishing department is currently operating at 30 percent of capacity and has facilities that are too large for the low volume of work. Table 1 summarizes the data pertaining to finishing. Fixed costs make up 71 percent of the current cost structure. Other manufacturing departments are beginning to tell finishing that they will be sending their work out to get plating and painting so as not to lose any work because of the high internal cost of finishing.
Finishing is trying to attract business from outside Accurate Cost Manufacturing. The external sales guidelines require a 35 percent profit margin applied to the full cost for all external work. With the current low level of work and high fixed costs, finishing cannot attract external sales due to cost.
In an effort to gain control of the true cost drivers of the business, the manager of the finishing operation has implemented activity-based costing. Tables 2 and 3 project the cost for products and volumes for one plating operation. The problem that the finishing manager now faces is that the manufacturing departments are about to send the 12-inch and 18-inch work to an outside shop due to lower costs.
In implementing activity-based costing, the manager thinks he has truly identified the proper system. The larger parts tend to run in smaller lot sizes and generate more paperwork. Smaller parts tend to be run in larger lot sizes and generate less paperwork.
In a recent meeting with the management of the manufacturing department and profit centers, it was stated that the installation of activity-based costing is in direct conflict with the change in the mix of work from small parts to large parts and the need to run smaller lot sizes. The manufacturing department and profit centers would like to pursue just-in-time manufacturing and further reduce the lot sizes for both small and large parts. During this meeting, the profit centers and manufacturing departments said the implementation of activity-based costing would force them to move their work out of the finishing department to outside shops.
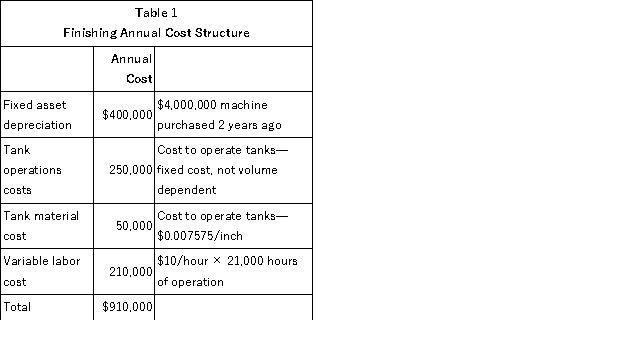
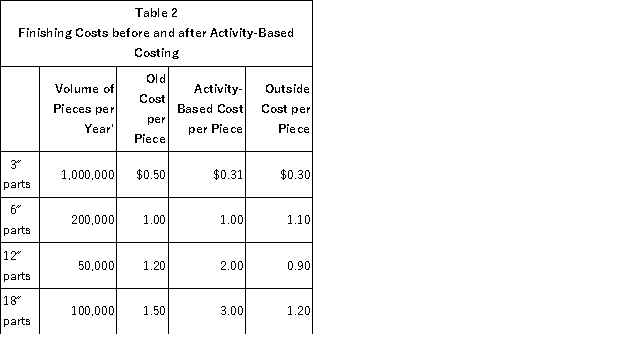
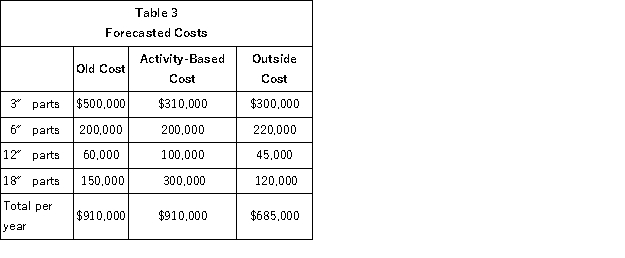
a. Analyze the current situation in this company. What should be done?
b. Compare and comment on the costs before and after ABC is implemented.
c. Has finishing management made a mistake by installing activity-based costing?
This case study illustrates that poorly designed ABC systems trying to recover the cost of excess capacity can fail.
a. The problem is they are trying to recover a sunk cost - fixed asset depreciation of $400,000. Because volumes have fallen, the original decision to acquire this much capacity turns out to have been wrong. They should take a one-time charge to profits by writing off some or most of the $400,000 machine. This will then lower unit costs. Other issues include:
• The volume-related death spiral. When volume decreases you raise prices, volume decreases more, you raise prices more, etc.
• Is the accounting system broken? They are installing ABC to fix a broken accounting system but that is not the major problem. Allocating the historical cost of excess capacity is the problem.
• Unitized transfer price. Unitization of fixed costs provides the wrong decision information to management for short-run decision making such as pricing special orders. Beware of unitized costs.
• Both the old absorption and new ABC accounting systems are sending the wrong signal for short-run decisions. Both systems are signaling higher costs and thus the apparent necessity to raise prices. Given the high fixed costs and decreasing volume, this is an incorrect inference.
• Allocation of decision rights (decision management versus decision control). How should management change the allocation and what will the systems' changes do to the focus of management? Are the benefits of the imperfect decentralized system outweighing the costs?
b. In reviewing the data provided in Table 2, the apparent cost drivers have been identified and "properly" allocated to the parts using ABC costing. What is not apparent is that the unitized costs are misleading in the first place. Unitizing the fixed costs will cause the apparent profitability of parts to vary with volume. This unitization is misleading and should be avoided. Since the firm has so much excess capacity, the opportunity cost of this capacity is close to zero. Thus, none of the depreciation on the plant should be charged to products.
The details of the cost drivers are not provided, although one can see shifts in parts costs of up to 100 percent. The question to be asked is what effect the changes in cost will have on the workload and whether the costs of these drivers should be reduced. If no action or effort is placed on using the data obtained from the ABC system to reduce the cost of the elements, then why incur the expense of implementing ABC? The cost and benefits of the system need to be evaluated.
c. If management is gaining a better understanding of the cost drivers of the business and implementing cost reduction activities, and the reductions outweigh the cost of ABC, then they have not made a mistake.
They may have made a mistake in the implementation process. The ABC costing system is aimed at decision management. However, the finishing department did not understand the implications of the signals that ABC costs send to the rest of the firm (decision control) for short-run decisions. If the department management operated the ABC system in parallel to the old system then they could have the information required to reduce costs and not send the misleading signals within the firm.
a. The problem is they are trying to recover a sunk cost - fixed asset depreciation of $400,000. Because volumes have fallen, the original decision to acquire this much capacity turns out to have been wrong. They should take a one-time charge to profits by writing off some or most of the $400,000 machine. This will then lower unit costs. Other issues include:
• The volume-related death spiral. When volume decreases you raise prices, volume decreases more, you raise prices more, etc.
• Is the accounting system broken? They are installing ABC to fix a broken accounting system but that is not the major problem. Allocating the historical cost of excess capacity is the problem.
• Unitized transfer price. Unitization of fixed costs provides the wrong decision information to management for short-run decision making such as pricing special orders. Beware of unitized costs.
• Both the old absorption and new ABC accounting systems are sending the wrong signal for short-run decisions. Both systems are signaling higher costs and thus the apparent necessity to raise prices. Given the high fixed costs and decreasing volume, this is an incorrect inference.
• Allocation of decision rights (decision management versus decision control). How should management change the allocation and what will the systems' changes do to the focus of management? Are the benefits of the imperfect decentralized system outweighing the costs?
b. In reviewing the data provided in Table 2, the apparent cost drivers have been identified and "properly" allocated to the parts using ABC costing. What is not apparent is that the unitized costs are misleading in the first place. Unitizing the fixed costs will cause the apparent profitability of parts to vary with volume. This unitization is misleading and should be avoided. Since the firm has so much excess capacity, the opportunity cost of this capacity is close to zero. Thus, none of the depreciation on the plant should be charged to products.
The details of the cost drivers are not provided, although one can see shifts in parts costs of up to 100 percent. The question to be asked is what effect the changes in cost will have on the workload and whether the costs of these drivers should be reduced. If no action or effort is placed on using the data obtained from the ABC system to reduce the cost of the elements, then why incur the expense of implementing ABC? The cost and benefits of the system need to be evaluated.
c. If management is gaining a better understanding of the cost drivers of the business and implementing cost reduction activities, and the reductions outweigh the cost of ABC, then they have not made a mistake.
They may have made a mistake in the implementation process. The ABC costing system is aimed at decision management. However, the finishing department did not understand the implications of the signals that ABC costs send to the rest of the firm (decision control) for short-run decisions. If the department management operated the ABC system in parallel to the old system then they could have the information required to reduce costs and not send the misleading signals within the firm.
2
When traditional absorption costing is employed, which of the following is false?
A)In a multi-product organization, product costs are properly reported for financial reporting purposes
B)In a single product organization, product costs are properly reported for financial reporting purposes
C)In a multi-product organization, product costs are accurately reported for decision-making purposes
D)In a single product organization, product costs are accurately reported for decision-making purposes
E)None of the above
A)In a multi-product organization, product costs are properly reported for financial reporting purposes
B)In a single product organization, product costs are properly reported for financial reporting purposes
C)In a multi-product organization, product costs are accurately reported for decision-making purposes
D)In a single product organization, product costs are accurately reported for decision-making purposes
E)None of the above
C
3
Different Overhead Allocation Bases
Step Up Inc. produces blue things and gray things. Blue things are in much greater demand in the market and the firm sells 120,000 blue things a year. Step Up Inc. sells 6,000 gray things per year in small boutiques. Things have a short shelf life. They must be distributed, sold, and consumed within two months of manufacture.
Both things use the identical production process and production facilities. Direct labor is $0.50 per thing and direct material is $0.50 per thing. Things are produced in batches. Blue things are produced in batches of 600 units and gray things in batches of 30. Each batch of things goes through the thingamajig, which is the machine that converts raw inputs into things. Each batch requires engineers to reset the machine for the next batch, calibrate settings, and test the first 10 things for product quality and conformity to standards. Even if sequential batches of the same things are made, setups must be performed for each new batch. All the overhead costs are incurred in setups. Indirect labor, indirect materials, and supplies consumed during setup cost $360,000 per year. The only costs of producing things are direct labor, direct materials, and the overhead of setups. The company is currently allocating setup costs to things based on direct labor cost.
The firm has been selling blue things for $4 per unit and gray things for $6 per unit. But foreign competition for blue things is starting to put pressure on the $4 price. Some competitors are selling blue things for as low as $3 per unit. Management is considering putting more emphasis on selling gray things, whose margins are higher. On the other hand, management worries that the current system for allocating overhead costs is misrepresenting the costs of the two products because direct labor costs are not representative of the time spent by each product on the thingamajig. Management is considering allocating setup costs using machine hours on the thingamajig. A batch of gray things requires one hour of machine time and a batch of blue things requires 20 hours of machine time.
Required:
Analyze the present situation. Is there anything wrong with the costing system? If so, should management change to the proposed allocation base of machine hours?
Step Up Inc. produces blue things and gray things. Blue things are in much greater demand in the market and the firm sells 120,000 blue things a year. Step Up Inc. sells 6,000 gray things per year in small boutiques. Things have a short shelf life. They must be distributed, sold, and consumed within two months of manufacture.
Both things use the identical production process and production facilities. Direct labor is $0.50 per thing and direct material is $0.50 per thing. Things are produced in batches. Blue things are produced in batches of 600 units and gray things in batches of 30. Each batch of things goes through the thingamajig, which is the machine that converts raw inputs into things. Each batch requires engineers to reset the machine for the next batch, calibrate settings, and test the first 10 things for product quality and conformity to standards. Even if sequential batches of the same things are made, setups must be performed for each new batch. All the overhead costs are incurred in setups. Indirect labor, indirect materials, and supplies consumed during setup cost $360,000 per year. The only costs of producing things are direct labor, direct materials, and the overhead of setups. The company is currently allocating setup costs to things based on direct labor cost.
The firm has been selling blue things for $4 per unit and gray things for $6 per unit. But foreign competition for blue things is starting to put pressure on the $4 price. Some competitors are selling blue things for as low as $3 per unit. Management is considering putting more emphasis on selling gray things, whose margins are higher. On the other hand, management worries that the current system for allocating overhead costs is misrepresenting the costs of the two products because direct labor costs are not representative of the time spent by each product on the thingamajig. Management is considering allocating setup costs using machine hours on the thingamajig. A batch of gray things requires one hour of machine time and a batch of blue things requires 20 hours of machine time.
Required:
Analyze the present situation. Is there anything wrong with the costing system? If so, should management change to the proposed allocation base of machine hours?
In this problem, there are three possible overhead allocation bases: direct labor (present system), machine hours (the proposed system), and number of batches. First, calculate product costs under each of the three allocation schemes:
1. Direct labor cost as the allocation base (present system):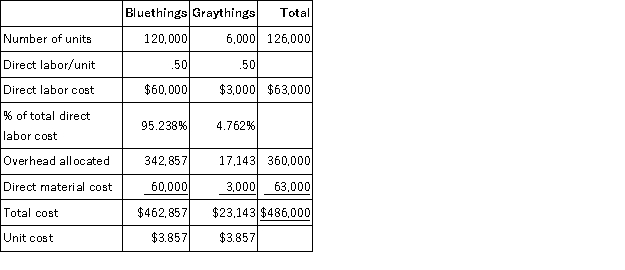
1. Direct labor cost as the allocation base (present system):
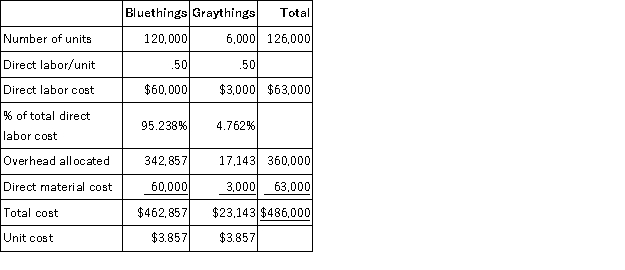
4
This is a comprehensive problem comparing absorption costing and ABC. It is suggested that as you progress through the problem, keep track of the correct solutions, because these values will be used again later in the problem set. Dehli Inkstone specializes in inkstone creation. Each finished inkstone needs 1½ pounds of special materials which cost $20 a pound. (One pound contains 16 ounces.) Drilling requires 1 direct labor hours, for which workers are paid $10 per hour, and 40 minutes of machine time. The preliminary product (a 'basic') is inspected to ensure that it is sound. Fifteen percent of the basics are rejected. It is not possible to rework these, and they have no salvage value. Each approved stone is handed to a master craftsperson who spends two hours making a 'Standard' product or three hours creating a 'Masterpiece'. Standards use half an hour of machine time and Masterpieces one hour. Finished inkstones are inspected again before packing. Four percent of finished products fail the final quality control assessment and are destroyed. Crafts persons are paid $18 per hour. It takes a 'basic' worker six minutes to package each inkstone in bubble wrap and a shipping carton, which cost 50 cents in materials and weigh 6 ounces in total.
Total overheads are estimated to be $587,400 per year and 97,900 direct labor hours are budgeted. Production plans for the year call for 60% of output to be Standard inkstones and the balance Masterpieces.
Which is the full (absorption) cost of a Standard inkstone, if machine hours are used as the cost driver? (Allow a little for rounding errors).
A)$94.81
B)$101.89
C)$107.25
D)$107.88
E)None of the above
Total overheads are estimated to be $587,400 per year and 97,900 direct labor hours are budgeted. Production plans for the year call for 60% of output to be Standard inkstones and the balance Masterpieces.
Which is the full (absorption) cost of a Standard inkstone, if machine hours are used as the cost driver? (Allow a little for rounding errors).
A)$94.81
B)$101.89
C)$107.25
D)$107.88
E)None of the above
فتح الحزمة
افتح القفل للوصول البطاقات البالغ عددها 19 في هذه المجموعة.
فتح الحزمة
k this deck
5
This is a comprehensive problem comparing absorption costing and ABC. It is suggested that as you progress through the problem, keep track of the correct solutions, because these values will be used again later in the problem set. Dehli Inkstone specializes in inkstone creation. Each finished inkstone needs 1½ pounds of special materials which cost $20 a pound. (One pound contains 16 ounces.) Drilling requires 1 direct labor hours, for which workers are paid $10 per hour, and 40 minutes of machine time. The preliminary product (a 'basic') is inspected to ensure that it is sound. Fifteen percent of the basics are rejected. It is not possible to rework these, and they have no salvage value. Each approved stone is handed to a master craftsperson who spends two hours making a 'Standard' product or three hours creating a 'Masterpiece'. Standards use half an hour of machine time and Masterpieces one hour. Finished inkstones are inspected again before packing. Four percent of finished products fail the final quality control assessment and are destroyed. Crafts persons are paid $18 per hour. It takes a 'basic' worker six minutes to package each inkstone in bubble wrap and a shipping carton, which cost 50 cents in materials and weigh 6 ounces in total.
Total overheads are estimated to be $587,400 per year and 97,900 direct labor hours are budgeted. Production plans for the year call for 60% of output to be Standard inkstones and the balance Masterpieces.
Dehli Inkstone recently employed a cost analyst, who recommended the adoption of an ABC system to obtain a more accurate understanding of the costs of the Standard and Masterpiece products. She has classified the overheads into the following four cost pools and identified the appropriate cost drivers: Independent of your answers above, assume total planned output is 25,595 units. What is the correct materials handling cost rate?
A)$2.209 per lb.
B)$2.521 per lb.
C)$2.136 per lb.
D)$2.572 per lb.
E)None of the above
Total overheads are estimated to be $587,400 per year and 97,900 direct labor hours are budgeted. Production plans for the year call for 60% of output to be Standard inkstones and the balance Masterpieces.
Dehli Inkstone recently employed a cost analyst, who recommended the adoption of an ABC system to obtain a more accurate understanding of the costs of the Standard and Masterpiece products. She has classified the overheads into the following four cost pools and identified the appropriate cost drivers: Independent of your answers above, assume total planned output is 25,595 units. What is the correct materials handling cost rate?
A)$2.209 per lb.
B)$2.521 per lb.
C)$2.136 per lb.
D)$2.572 per lb.
E)None of the above
فتح الحزمة
افتح القفل للوصول البطاقات البالغ عددها 19 في هذه المجموعة.
فتح الحزمة
k this deck
6
Describe ABC
Required:
a. What is activity-based costing and how does it differ from traditional absorption costing?
b. Describe the advantages and disadvantages of activity-based costing systems.
Required:
a. What is activity-based costing and how does it differ from traditional absorption costing?
b. Describe the advantages and disadvantages of activity-based costing systems.
فتح الحزمة
افتح القفل للوصول البطاقات البالغ عددها 19 في هذه المجموعة.
فتح الحزمة
k this deck
7
ABC versus Traditional Absorption Costing
Last year CCB Medical Technologies (CCB) introduced a proprietary orthopedic surgical saw that is used in a variety of orthopedic applications. However, its largest demand is in hip replacement surgeries. The electric reciprocating saw's patented technology (including the blade) reduces noise and vibration and increases precision cutting, thereby reducing postoperative complications. CCB manufactures and sells both the saw and blades. CCB blades are designed and engineered specifically for the CCB saw, and CCB saws are designed to only be used with CCB blades. When an orthopedic surgeon performs a surgery, each blade is dedicated to one particular patient and, once used, the blade is discarded. Surgeons often use two or three blades during surgery on a patient. CCB saws sell for $2,000 each and CCB blades sell for $450 per blade.
CCB manufactures both the saw and blades in the same factory. The following table summarizes the variable and direct costs of the saws and blades and the number of units of each product produced and sold last year. CCB uses an activity-based costing system to assign fixed manufacturing overhead to the saws and blades. There are three fixed manufacturing overhead cost pools in the ABC system: batch costs, product-line engineering costs, and other factory overhead. The following describes the ABC methodology:
• Batch costs ($173,000 last year): Batch costs are allocated to the two product lines based on the number of batches manufactured during the year. Saws are produced in batch sizes of 10 saws per batch and blades are manufactured in batch sizes of 500 blades per batch.
• Product-line engineering costs ($724,000 last year): Product-line engineering costs are assigned to the two product lines (saws and blades) after a survey of the engineers inquiring how they spent their time. Based on last year's survey, $289,000 was assigned to saws and $435,000 was assigned to blades.
• Other factory overhead ($330,000): Other factory overhead consists of all other fixed manufacturing overhead not included in either batch costs or product-line engineering costs. These costs are allocated to the saws and blades based on direct labor cost.
Required:
a. Compute CCB's unit manufacturing costs and operating margins (revenues less cost of goods sold) for last year for the saws and blades using the activity-based costing methodology described above.
b. Having seen the ABC income statements prepared in part (a), CCB management wants to see how the operating margins (revenues less cost of goods sold) for the saws and blades would look if traditional absorption costing is used where the total fixed factory overhead is allocated to the saws and blades using direct labor dollars.
c. Make a recommendation to management as to whether ABC (part a) or traditional absorption costing (part b) should be used. Justify your recommendation.
Last year CCB Medical Technologies (CCB) introduced a proprietary orthopedic surgical saw that is used in a variety of orthopedic applications. However, its largest demand is in hip replacement surgeries. The electric reciprocating saw's patented technology (including the blade) reduces noise and vibration and increases precision cutting, thereby reducing postoperative complications. CCB manufactures and sells both the saw and blades. CCB blades are designed and engineered specifically for the CCB saw, and CCB saws are designed to only be used with CCB blades. When an orthopedic surgeon performs a surgery, each blade is dedicated to one particular patient and, once used, the blade is discarded. Surgeons often use two or three blades during surgery on a patient. CCB saws sell for $2,000 each and CCB blades sell for $450 per blade.
CCB manufactures both the saw and blades in the same factory. The following table summarizes the variable and direct costs of the saws and blades and the number of units of each product produced and sold last year. CCB uses an activity-based costing system to assign fixed manufacturing overhead to the saws and blades. There are three fixed manufacturing overhead cost pools in the ABC system: batch costs, product-line engineering costs, and other factory overhead. The following describes the ABC methodology:
• Batch costs ($173,000 last year): Batch costs are allocated to the two product lines based on the number of batches manufactured during the year. Saws are produced in batch sizes of 10 saws per batch and blades are manufactured in batch sizes of 500 blades per batch.
• Product-line engineering costs ($724,000 last year): Product-line engineering costs are assigned to the two product lines (saws and blades) after a survey of the engineers inquiring how they spent their time. Based on last year's survey, $289,000 was assigned to saws and $435,000 was assigned to blades.
• Other factory overhead ($330,000): Other factory overhead consists of all other fixed manufacturing overhead not included in either batch costs or product-line engineering costs. These costs are allocated to the saws and blades based on direct labor cost.
Required:
a. Compute CCB's unit manufacturing costs and operating margins (revenues less cost of goods sold) for last year for the saws and blades using the activity-based costing methodology described above.
b. Having seen the ABC income statements prepared in part (a), CCB management wants to see how the operating margins (revenues less cost of goods sold) for the saws and blades would look if traditional absorption costing is used where the total fixed factory overhead is allocated to the saws and blades using direct labor dollars.
c. Make a recommendation to management as to whether ABC (part a) or traditional absorption costing (part b) should be used. Justify your recommendation.
فتح الحزمة
افتح القفل للوصول البطاقات البالغ عددها 19 في هذه المجموعة.
فتح الحزمة
k this deck
8
This is a comprehensive problem comparing absorption costing and ABC. It is suggested that as you progress through the problem, keep track of the correct solutions, because these values will be used again later in the problem set. Dehli Inkstone specializes in inkstone creation. Each finished inkstone needs 1½ pounds of special materials which cost $20 a pound. (One pound contains 16 ounces.) Drilling requires 1 direct labor hours, for which workers are paid $10 per hour, and 40 minutes of machine time. The preliminary product (a 'basic') is inspected to ensure that it is sound. Fifteen percent of the basics are rejected. It is not possible to rework these, and they have no salvage value. Each approved stone is handed to a master craftsperson who spends two hours making a 'Standard' product or three hours creating a 'Masterpiece'. Standards use half an hour of machine time and Masterpieces one hour. Finished inkstones are inspected again before packing. Four percent of finished products fail the final quality control assessment and are destroyed. Crafts persons are paid $18 per hour. It takes a 'basic' worker six minutes to package each inkstone in bubble wrap and a shipping carton, which cost 50 cents in materials and weigh 6 ounces in total.
Total overheads are estimated to be $587,400 per year and 97,900 direct labor hours are budgeted. Production plans for the year call for 60% of output to be Standard inkstones and the balance Masterpieces.
Which is the full (absorption) cost of a Masterpiece inkstone, if direct labor hours are used as the cost driver? (Allow a little for rounding errors).
A)$133.47
B)$106.47
C)$102.55
D)$96.10
E)None of the above
Total overheads are estimated to be $587,400 per year and 97,900 direct labor hours are budgeted. Production plans for the year call for 60% of output to be Standard inkstones and the balance Masterpieces.
Which is the full (absorption) cost of a Masterpiece inkstone, if direct labor hours are used as the cost driver? (Allow a little for rounding errors).
A)$133.47
B)$106.47
C)$102.55
D)$96.10
E)None of the above
فتح الحزمة
افتح القفل للوصول البطاقات البالغ عددها 19 في هذه المجموعة.
فتح الحزمة
k this deck
9
For Dehli Inkstone, is it worth implementing a full-fledged ABC system, based upon the findings for these two products?
A)No, for Standard the cost difference between using machine hours and ABC is less than 30 cents per unit, so adoption of the ABC system is not cost-beneficial
B)Yes, all of the single-base allocation systems over cost the Masterpiece
C)No, for Masterpiece the cost difference between using labor hours and ABC is less than 40 cents per unit, so adoption of the ABC system is not cost-beneficial
D)No, the ABC system has failed to reduce total overheads
E)No, the proportions of the different inputs consumed by each product are not sufficiently different to make ABC worthwhile
A)No, for Standard the cost difference between using machine hours and ABC is less than 30 cents per unit, so adoption of the ABC system is not cost-beneficial
B)Yes, all of the single-base allocation systems over cost the Masterpiece
C)No, for Masterpiece the cost difference between using labor hours and ABC is less than 40 cents per unit, so adoption of the ABC system is not cost-beneficial
D)No, the ABC system has failed to reduce total overheads
E)No, the proportions of the different inputs consumed by each product are not sufficiently different to make ABC worthwhile
فتح الحزمة
افتح القفل للوصول البطاقات البالغ عددها 19 في هذه المجموعة.
فتح الحزمة
k this deck
10
Which of the following is a correct matching of terms?
A)Depreciation of equipment is a batch-level cost
B)Cutting a table leg is a unit-level cost
C)Insurance is a product-level cost
D)Package design is a production-sustaining cost
E)None of the above
A)Depreciation of equipment is a batch-level cost
B)Cutting a table leg is a unit-level cost
C)Insurance is a product-level cost
D)Package design is a production-sustaining cost
E)None of the above
فتح الحزمة
افتح القفل للوصول البطاقات البالغ عددها 19 في هذه المجموعة.
فتح الحزمة
k this deck
11
This is a comprehensive problem comparing absorption costing and ABC. It is suggested that as you progress through the problem, keep track of the correct solutions, because these values will be used again later in the problem set. Dehli Inkstone specializes in inkstone creation. Each finished inkstone needs 1½ pounds of special materials which cost $20 a pound. (One pound contains 16 ounces.) Drilling requires 1 direct labor hours, for which workers are paid $10 per hour, and 40 minutes of machine time. The preliminary product (a 'basic') is inspected to ensure that it is sound. Fifteen percent of the basics are rejected. It is not possible to rework these, and they have no salvage value. Each approved stone is handed to a master craftsperson who spends two hours making a 'Standard' product or three hours creating a 'Masterpiece'. Standards use half an hour of machine time and Masterpieces one hour. Finished inkstones are inspected again before packing. Four percent of finished products fail the final quality control assessment and are destroyed. Crafts persons are paid $18 per hour. It takes a 'basic' worker six minutes to package each inkstone in bubble wrap and a shipping carton, which cost 50 cents in materials and weigh 6 ounces in total.
Total overheads are estimated to be $587,400 per year and 97,900 direct labor hours are budgeted. Production plans for the year call for 60% of output to be Standard inkstones and the balance Masterpieces.
For a Standard inkstone, which is true of the materials input needed (to 3 significant figures)?
A)Total weight is 2.279 pounds
B)Total weight is 2.213 pounds
C)Total weight is 2.140 pounds
D)Total weight is 1.875 pounds
E)None of the above
Total overheads are estimated to be $587,400 per year and 97,900 direct labor hours are budgeted. Production plans for the year call for 60% of output to be Standard inkstones and the balance Masterpieces.
For a Standard inkstone, which is true of the materials input needed (to 3 significant figures)?
A)Total weight is 2.279 pounds
B)Total weight is 2.213 pounds
C)Total weight is 2.140 pounds
D)Total weight is 1.875 pounds
E)None of the above
فتح الحزمة
افتح القفل للوصول البطاقات البالغ عددها 19 في هذه المجموعة.
فتح الحزمة
k this deck
12
Honey Lake Summer Camp
For many years the Honey Lake Summer Camp had used the number of campers per week to estimate weekly costs. The summer camp is open for ten weeks during the summer with a different number of campers each week. July is busiest with June and the end of August least busy. Costs from the last week of summer camp in Year 1 are used to estimate costs for Year 2 for pricing purposes. The following costs occurred during the last week of Year 1 and the costs of each cost category are expected to be the same for Year 2:
Cost per camper: $12,200/50 campers = $244/camper
The Honey Lake Summer Camp expects 75 campers during the second week of July.
Required:
a. What is the expected cost of that week using the average cost?
b. What is the expected cost of that week using ABC?
For many years the Honey Lake Summer Camp had used the number of campers per week to estimate weekly costs. The summer camp is open for ten weeks during the summer with a different number of campers each week. July is busiest with June and the end of August least busy. Costs from the last week of summer camp in Year 1 are used to estimate costs for Year 2 for pricing purposes. The following costs occurred during the last week of Year 1 and the costs of each cost category are expected to be the same for Year 2:
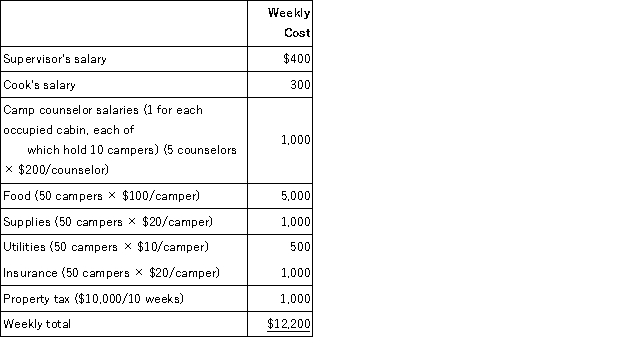
The Honey Lake Summer Camp expects 75 campers during the second week of July.
Required:
a. What is the expected cost of that week using the average cost?
b. What is the expected cost of that week using ABC?
فتح الحزمة
افتح القفل للوصول البطاقات البالغ عددها 19 في هذه المجموعة.
فتح الحزمة
k this deck
13
This is a comprehensive problem comparing absorption costing and ABC. It is suggested that as you progress through the problem, keep track of the correct solutions, because these values will be used again later in the problem set. Dehli Inkstone specializes in inkstone creation. Each finished inkstone needs 1½ pounds of special materials which cost $20 a pound. (One pound contains 16 ounces.) Drilling requires 1 direct labor hours, for which workers are paid $10 per hour, and 40 minutes of machine time. The preliminary product (a 'basic') is inspected to ensure that it is sound. Fifteen percent of the basics are rejected. It is not possible to rework these, and they have no salvage value. Each approved stone is handed to a master craftsperson who spends two hours making a 'Standard' product or three hours creating a 'Masterpiece'. Standards use half an hour of machine time and Masterpieces one hour. Finished inkstones are inspected again before packing. Four percent of finished products fail the final quality control assessment and are destroyed. Crafts persons are paid $18 per hour. It takes a 'basic' worker six minutes to package each inkstone in bubble wrap and a shipping carton, which cost 50 cents in materials and weigh 6 ounces in total.
Total overheads are estimated to be $587,400 per year and 97,900 direct labor hours are budgeted. Production plans for the year call for 60% of output to be Standard inkstones and the balance Masterpieces.
For a Standard inkstone, which is true of the machine hours (MH) needed (to 3 decimal places)?
A)Total MH are 1.188
B)Total MH are 1.305
C)Total MH are 1.338
D)Total MH are 1.397
E)None of the above
Total overheads are estimated to be $587,400 per year and 97,900 direct labor hours are budgeted. Production plans for the year call for 60% of output to be Standard inkstones and the balance Masterpieces.
For a Standard inkstone, which is true of the machine hours (MH) needed (to 3 decimal places)?
A)Total MH are 1.188
B)Total MH are 1.305
C)Total MH are 1.338
D)Total MH are 1.397
E)None of the above
فتح الحزمة
افتح القفل للوصول البطاقات البالغ عددها 19 في هذه المجموعة.
فتح الحزمة
k this deck
14
This is a comprehensive problem comparing absorption costing and ABC. It is suggested that as you progress through the problem, keep track of the correct solutions, because these values will be used again later in the problem set. Dehli Inkstone specializes in inkstone creation. Each finished inkstone needs 1½ pounds of special materials which cost $20 a pound. (One pound contains 16 ounces.) Drilling requires 1 direct labor hours, for which workers are paid $10 per hour, and 40 minutes of machine time. The preliminary product (a 'basic') is inspected to ensure that it is sound. Fifteen percent of the basics are rejected. It is not possible to rework these, and they have no salvage value. Each approved stone is handed to a master craftsperson who spends two hours making a 'Standard' product or three hours creating a 'Masterpiece'. Standards use half an hour of machine time and Masterpieces one hour. Finished inkstones are inspected again before packing. Four percent of finished products fail the final quality control assessment and are destroyed. Crafts persons are paid $18 per hour. It takes a 'basic' worker six minutes to package each inkstone in bubble wrap and a shipping carton, which cost 50 cents in materials and weigh 6 ounces in total.
Total overheads are estimated to be $587,400 per year and 97,900 direct labor hours are budgeted. Production plans for the year call for 60% of output to be Standard inkstones and the balance Masterpieces.
For a Masterpiece inkstone, which is true of the direct labor hours (DLH) needed (to 3 decimal places)?
A)Total DLH are 4.100
B)Total DLH are 4.401
C)Total DLH are 4.406
D)Total DLH are 4.450
E)None of the above
Total overheads are estimated to be $587,400 per year and 97,900 direct labor hours are budgeted. Production plans for the year call for 60% of output to be Standard inkstones and the balance Masterpieces.
For a Masterpiece inkstone, which is true of the direct labor hours (DLH) needed (to 3 decimal places)?
A)Total DLH are 4.100
B)Total DLH are 4.401
C)Total DLH are 4.406
D)Total DLH are 4.450
E)None of the above
فتح الحزمة
افتح القفل للوصول البطاقات البالغ عددها 19 في هذه المجموعة.
فتح الحزمة
k this deck
15
Decision Management vs. Decision Control of ABC
فتح الحزمة
افتح القفل للوصول البطاقات البالغ عددها 19 في هذه المجموعة.
فتح الحزمة
k this deck
16
What is true when ABC is used?
A)The full cost of the Masterpiece is $132.96
B)Prime cost of the Standard is $50.75
C)The full cost of the Standard is $107.43
D)ABC overheads allocated to Masterpiece total $25.52
E)None of the above
A)The full cost of the Masterpiece is $132.96
B)Prime cost of the Standard is $50.75
C)The full cost of the Standard is $107.43
D)ABC overheads allocated to Masterpiece total $25.52
E)None of the above
فتح الحزمة
افتح القفل للوصول البطاقات البالغ عددها 19 في هذه المجموعة.
فتح الحزمة
k this deck
17
This is a comprehensive problem comparing absorption costing and ABC. It is suggested that as you progress through the problem, keep track of the correct solutions, because these values will be used again later in the problem set. Dehli Inkstone specializes in inkstone creation. Each finished inkstone needs 1½ pounds of special materials which cost $20 a pound. (One pound contains 16 ounces.) Drilling requires 1 direct labor hours, for which workers are paid $10 per hour, and 40 minutes of machine time. The preliminary product (a 'basic') is inspected to ensure that it is sound. Fifteen percent of the basics are rejected. It is not possible to rework these, and they have no salvage value. Each approved stone is handed to a master craftsperson who spends two hours making a 'Standard' product or three hours creating a 'Masterpiece'. Standards use half an hour of machine time and Masterpieces one hour. Finished inkstones are inspected again before packing. Four percent of finished products fail the final quality control assessment and are destroyed. Crafts persons are paid $18 per hour. It takes a 'basic' worker six minutes to package each inkstone in bubble wrap and a shipping carton, which cost 50 cents in materials and weigh 6 ounces in total.
Total overheads are estimated to be $587,400 per year and 97,900 direct labor hours are budgeted. Production plans for the year call for 60% of output to be Standard inkstones and the balance Masterpieces.
What is true when ABC is used in Dehli Inkstone?
A)Machine operations costs run $5.025 per machine hour
B)Labor-related costs are $0.143 per direct labor dollar
C)Inspection costs are $1.891 per inspection
D)Labor-based overheads are 19.6% per direct labor dollar
E)None of the above
Total overheads are estimated to be $587,400 per year and 97,900 direct labor hours are budgeted. Production plans for the year call for 60% of output to be Standard inkstones and the balance Masterpieces.
What is true when ABC is used in Dehli Inkstone?
A)Machine operations costs run $5.025 per machine hour
B)Labor-related costs are $0.143 per direct labor dollar
C)Inspection costs are $1.891 per inspection
D)Labor-based overheads are 19.6% per direct labor dollar
E)None of the above
فتح الحزمة
افتح القفل للوصول البطاقات البالغ عددها 19 في هذه المجموعة.
فتح الحزمة
k this deck